Revision Notes for CBSE Class 12 Chemistry Chapter 6 (Principles and Processes of Isolation of Elements) - Free PDF Download
NCERT Class 12 Chemistry Chapter 6 Notes - Metallurgy is extremely important for your class 12 Inorganic Chemistry syllabus. Metallurgy is one of those chapters with the most practical applications. Class 12 Chemistry General Principles And Processes of Isolation of Elements Notes by Vedantu will help you score better marks in your CBSE Class 12 Chemistry exams. These notes were prepared by experts to guarantee your success. Download the Metallurgy Class 12 NCERT Notes PDF and start studying smarter today.
Download CBSE Class 12 Chemistry Notes 2024-25 PDF
Also, check CBSE Class 12 Chemistry revision notes for other chapters:
CBSE Class 12 Chemistry Chapter-wise Notes | |
Chapter 6 - General Principles and Processes of Isolation of Elements | |
Important Principles and Processes of Isolation of Elements Related Links
Explore a compilation of valuable links related to Principles and Processes of Isolation of Elements topic, offering comprehensive study materials, solved examples, and practice questions for Class 12 students studying chemistry.
Principles and Processes of Isolation of Elements Related Study Materials |
Principles and Processes of Isolation of Elements Important Questions |
Principles and Processes of Isolation of Elements NCERT Solutions |
Important Class 12 Study Materials Links
Find a curated selection of study resources for Class 12 subjects, helping students prepare effectively and excel in their academic pursuits.
Important Class 12 Related Links |
General Principles and Processes of Isolation of Elements Class 12 Notes Chemistry - Basic Subjective Questions
Section-A (1 Mark Questions)
1. What is added as flux in extraction of iron?
Ans. Limestone is used as flux in extraction of iron.
2. What is Blister copper?
Ans. The solidified copper obtained after extraction has blister appearance due to evolution of SO2 is called blister copper.
3. What is the role of cryolite in the metallurgy of aluminium?
Ans. Cryolite (Na3AlF6) has two roles in the metallurgy of aluminium:
1. To decrease the melting point of the mixture from 2323 K to 1140 K.
2. To increase the electrical conductivity of Al2O3.
4. Why is zinc not extracted from zinc oxide through reduction using CO?
Ans. The standard Gibbs free energy of formation of ZnO from Zn is lower than that of CO2 from CO. Therefore, CO cannot reduce ZnO to Zn. Hence, Zn is not extracted from ZnO through reduction using CO.
5. Give name of most abundant metal in earth’s crust.
Ans. Aluminium (8.3% by weight) is most abundant metal in earth's crust.
6. Are all minerals ores?
Ans. No, all minerals are not ores.
7. Name the ore used for extraction of iron.
Ans. Haematite, Magnetite etc. are used for the extraction of iron.
8. From which ore Cu is extracted?
Ans. Copper pyrite, Cuprite etc. are used for the extraction of copper.
9. Write the principle of Hydraulic washing.
Ans. Hydraulic washing is based on the principle that when upward stream of running water is used to wash the ore, lighter gangue particle washed away and heavier ores are left behind.
10. Name the furnace used in extraction of iron from its oxides.
Ans. Blast furnace is used in the extraction of iron from its oxides.
Section-B (2 Marks Questions)
11. How are gold and silver extracted?
Ans. Gold and silver are extracted by leaching the metal with CN–. The metal is later recovered by displacement method in which zinc acts as reducing agent.
$4Au(s)+8CN(aq)+2H_{2}O(aq)+O_{2}(g)\rightarrow 4\left [ Au\left ( CN_{2} \right ) \right ]^{-}(aq)+4OH^{-}(aq)$
$2\left [ Au(CN)_{2} \right ]^{-}(aq)+Zn(s)\rightarrow 2Au(s)+\left [ Zn\left ( CN \right )_{4} \right ]^{2-}(aq)$
12. What is the principle behind chromatography? Name some types of chromatographic techniques.
Ans. The principle behind chromatography is that different components of a mixture are differently adsorbed on an adsorbent. Some of the chromatographic techniques are paper chromatography, column chromatography, gas chromatography etc.
13. Give the basic requirement for vapour phase refining.
Ans. The metal is treated with a suitable reagent to form a volatile compound.
Then the volatile compound is decomposed to give the pure metal at high temperature.
14. What is collector used in froth floatation process? Name any one collector.
Ans. Substances which enhance the non - wettability of mineral particles are collectors, e.g. pine oils, xanthates, fatty acid, etc.
15. What is the composition of copper matte?
Ans. Copper matte is a mixture of copper sulfide (Cu2S) and some iron sulfide (FeS).
16. Name the main components of the following: (i) Brass (ii) German silver.
Ans. (i) Brass - (Cu = 60%, Zn = 40%)
(ii) German silver [Cu = 25-30%, Zn = 25-30%, Ni = 40-50%]
17. Why is copper matte put in silica lined converter?
Ans. Copper matte mainly contains Cu2S and FeS. When a hot air blast is blown through molten matter taken in a silica lined converter, FeS is oxidized to FeO. Silica (SiO2) present as lining acts as flux and combines with FeO to form slag.
2FeS + 3O2 → 2FeO + 2SO2
FeO + SiO2 → FeSiO3 (slag).
18. (i) Which solution is used for the leaching of silver metal in the presence of air in the metallurgy of silver?
(ii) Which is the cheapest and most abundant reducing agent which is used in the extraction of metals ?
Ans. (i) The 0.5% solution of sodium or potassium cyanide is used for the leaching of silver metal.
4Ag + 8NaCN + 2H2O + O2 → 4Na[Ag(CN)2] + 4NaOH
(ii) Carbon in the from of coke.
19. State the principle of the method of zone refining of metals.
Ans. Zone refining: It is based on the principle that the impurities are more soluble in molten state than in the solid state of the metal.
20. Describe the principle controlling the following process: Froth floatation method of concentration of a sulphide.
Ans. Froth floatation method: This method is used for removing gangue from sulphide ores. In this powdered ore is mixed with collectors (e.g. pine oils, fatty acids etc.) and froth stabilizers (e.g. cresols, aniline) which enhance non-wettability of the mineral particles and froth stabilization respectively. As a result of which ore comes with froth and gangue remain in the solution.
PDF Summary - Class 12 Chemistry General Principles and Processes of Isolation of Elements Notes (Chapter 6)
1. Introduction:
Mineral is the natural compound of a metal and non-metal. Metals can be extracted from minerals. A naturally existing solid material from which a valuable metal or mineral can be commercially mined is called an ore. Ore is contaminated with impurities or undesired material known as gangue. All ores are minerals, but the reverse is not true.
Some Important Ores of Metals
Metals | Ores | Composition |
Aluminum | Bauxite Corundum | ${{\text{A}}{{\text{l}}_2}{{\text{O}}_3} \cdot 2{{\text{H}}_2}} \\$ ${{\text{A}}{{\text{l}}_2}{{\text{O}}_3} \cdot {{\text{H}}_2}} \\$ ${{\text{A}}{{\text{l}}_2}{{\text{O}}_3}}$ |
Iron | Hematite Magnetite Siderite Iron Pyrite | ${{\text{F}}{{\text{e}}_2}{{\text{O}}_3}} \\$ ${{\text{F}}{{\text{e}}_3}{{\text{O}}_4}} \\$ ${{\text{FeC}}{{\text{O}}_3}} \\$ ${{\text{Fe}}{{\text{S}}_2}} \\$ ${{\text{F}}{{\text{e}}_2}{{\text{O}}_3}.3{{\text{H}}_2}}$ |
Copper | Copper pyrite Copper glance Cuprite Malachite Azurite | ${{\text{CuFe}}{{\text{S}}_2}} \\$ ${{\text{C}}{{\text{u}}_2}{\text{S}}} \\$ ${{\text{C}}{{\text{u}}_2}} \\$ ${{\text{CuC}}{{\text{O}}_3} \cdot {\text{Cu}}{{({\text{OH}})}_2}} \\$ ${2{\text{CuC}}{{\text{O}}_3} \cdot {\text{Cu}}{{({\text{OH}})}_2}}$ |
Zinc | Zinc blende or Sphalerite Calamine Zincite | ${{\text{ZnS}}} \\$ ${{\text{ZnC}}{{\text{O}}_3}} \\$ ${{\text{ZnO}}}$ |
Lead | Galena Anglesite Cerussite | ${{\text{PbS}}} \\$ ${{\text{PbS}}{{\text{O}}_4}} \\$ ${{\text{PbC}}{{\text{O}}_3}}$ |
Magnesium | Carnallite Magnesite Dolomite Epsom salt (Epsomite) | ${{\text{KCl}}.{\text{MgC}}{{\text{l}}_2}6{{\text{H}}_2}{\text{O}}\left( {{{\text{K}}_2}{\text{MgC}}{{\text{l}}_4} \cdot 6{{\text{H}}_2}{\text{O}}} \right)} \\$ ${{\text{MgC}}{{\text{O}}_3}} \\$ ${{\text{MgC}}{{\text{O}}_3}{\text{CaC}}{{\text{O}}_3}} \\$ ${{\text{MgS}}{{\text{O}}_4}7{{\text{H}}_2}} \\$ $4{{{\text{K}}_2}{\text{M}}{{\text{g}}_2}{{\left( {{\text{S}}{{\text{O}}_4}} \right)}_3}}$ |
Tin | Cassiterite (Tin Stone) | ${\text{Sn}}{{\text{O}}_2}$ |
Silver | Silver glance (Argentite) Pyrargyrite (Ruby Silver) Chlorargyrite (Horn silver) Stefinite Proustite | ${{\text{A}}{{\text{g}}_2}{\text{S}}} \\$ ${{\text{A}}{{\text{g}}_3}{\text{Sb}}{{\text{S}}_3}} \\$ ${{\text{AgCl}}} \\$ ${{\text{A}}{{\text{g}}_5}{\text{Sb}}{{\text{S}}_4}} \\$ ${{\text{A}}{{\text{g}}_3}{\text{As}}{{\text{S}}_3}}$ |
2. Metallurgy
The process used for the extraction of metal from its ore is known as metallurgy. The isolation and extraction of metal can be done in the following 4 steps:
Crushing of the ore, Dressing or concentration of the ore, Isolation of the crude metal from its ore, Purification of refining of the metal.
2.1 Crushing and Grinding
Jaw crushers first crushes the ore and then is grinded to a powder form(pulverisation of the ore) in equipment like ball mills.
2.2 Concentration
The removal of undesired material from ore is known as dressing or beneficiation of ore.
2.2.1 Hydraulic Washing
It is based on the density differences between the gangue and or particles. The ore is agitated with water or washed with an upward stream of running water, and the lighter particles of sand, clay, and other impurities are washed away, leaving the heavier ore particles behind.
2.2.2 Electromagnetic Separation
It's based on the magnetic characteristics of the ore's constituents. When the ore or the contaminants connected with it are magnetic, this method is utilized. A magnetic separator is made up of a belt (made of leather or brass) that moves over two rollers, one on each side. When the powdered ore is dumped on the belt at the other end, the magnetic component of the ore is drawn to the magnetic roller and falls closer to it, while non-magnetic impurities fall away. For example, chromite ore is separated from non-magnetic siliceous material.
2.2.3 Froth Floatation Process:
Low grade sulfide ores such as galena, copper iron pyrite, zinc blend are usually concentrated from this method. It is based on the fact that the degree of wet ability with water varies in gangue and ore. Generally, the gangue particles are wetted by water and ore particles are wetted by oil.
When a mineral has impurities such as other minerals. The presence of these substances helps to separate the impurities by activating or depressing the flotation property of other minerals present as impurities. Zinc blended and pyrites are present as impurities in galena. Potassium ethyl xanthate is used as a collector and ${\text{NaCN}}$ and ${\text{N}}{{\text{a}}_{\text{2}}}{\text{C}}{{\text{O}}_{\text{3}}}$ is used as a depressant in the flotation process.
2.2.4 Leaching of Alumina from Bauxite:
Bauxite, the primary source of aluminium, typically contains impurities such as ${\text{SiO}}$ iron oxides, and titanium oxide. The powdered ore is digested with a concentrated solution of ${\text{NaOH}}$ at ${\text{473}} - {\text{523 K}}$ and $35 - 36{\text{ bar}}$ pressure to concentrate it. ${\text{A}}{{\text{l}}_{\text{2}}}{{\text{O}}_{\text{3}}}$ is leached out as sodium aluminate in this fashion leaving behind the impurities present.
${\text{A}}{{\text{l}}_{\text{2}}}{{\text{O}}_{\text{3}}} + {\text{2NaOH}} + {\text{3}}{{\text{H}}_{\text{2}}}{\text{O}} \to {\text{2Na}}\left[ {{\text{Al}}{{\left( {{\text{OH}}} \right)}_{\text{4}}}} \right]$
By passing carbon-dioxide gas through the solution, the aluminate is neutralized, and hydrated ${\text{A}}{{\text{l}}_{\text{2}}}{{\text{O}}_{\text{3}}}$ is precipitated. The solution is seeded with freshly prepared samples of hydrated ${\text{A}}{{\text{l}}_{\text{2}}}{{\text{O}}_{\text{3}}}$ at this point, causing ${\text{Al}}{\left( {{\text{OH}}} \right)_{\text{3}}}$ to precipitate.
${\text{2Na}}\left[ {{\text{Al}}{{\left( {{\text{OH}}} \right)}_{\text{4}}}} \right] + {\text{C}}{{\text{O}}_2} \to {\text{A}}{{\text{l}}_{\text{2}}}{{\text{O}}_{\text{3}}}{\text{.x}}{{\text{H}}_{\text{2}}}{\text{O}} + 2{\text{NaHC}}{{\text{O}}_{\text{3}}}$
${\text{A}}{{\text{l}}_{\text{2}}}{{\text{O}}_{\text{3}}}{\text{.x}}{{\text{H}}_{\text{2}}}{\text{O}}\xrightarrow{\Delta }{\text{A}}{{\text{l}}_{\text{2}}}{{\text{O}}_{\text{3}}} + {\text{x}}{{\text{H}}_{\text{2}}}{\text{O}}$
The corresponding metal/ore is leached with a dilute solution of ${\text{NaCN}}$ or ${\text{KCN}}$ in the presence of air in the metallurgy of silver and gold, and the metal is recovered subsequently by displacement with zinc scrap. The Mac-Arthur Forrest Cyanide process is another name for it.
2.3 Extraction of Crude Metal from Concentrated Ore
The concentrated ore must be transformed into a form that can be reduced. Before reduction, the sulfide ore is usually transformed to oxide. Oxides are a lot easier to get rid of. As a result, the separation of metals from concentrated ore is divided into two key phases, as shown below.
(I) Conversion to oxide; (ii) Conversion of oxide to metal.
2.3.1 Conversion to Oxide:
The process of converting ore to oxide is carried out in two ways depending on the nature of ore.
2.3.1.1 Calcination:
Calcination is the process of rapidly heating the mined ore in the absence of air or with a limited supply of air. The following changes occur as a result of the calcination process:
(a) The carbonate ore decomposes to generate the metal's oxide. For example,
${\text{FeC}}{{\text{O}}_{\text{3}}}\xrightarrow{\Delta }{\text{FeO }} + {\text{ C}}{{\text{O}}_{\text{2}}} \uparrow $
${\text{CaC}}{{\text{O}}_{\text{3}}}\xrightarrow{\Delta }{\text{CaO }} + {\text{ C}}{{\text{O}}_{\text{2}}} \uparrow $
(b) Water of crystallization in the hydrated oxide ore is lost as moisture, for example
\[{\text{2F}}{{\text{e}}_2}{{\text{O}}_{\text{3}}}.3{{\text{H}}_{\text{2}}}{\text{O}}\xrightarrow{\Delta }{\text{2F}}{{\text{e}}_2}{{\text{O}}_3}{\text{ }} + {\text{ 3}}{{\text{H}}_2}{\text{O}}\]
(c) Organic stuff in the ore is ejected, causing the ore to become porous. Impurities that are volatile are eliminated.
2.3.1.2 Roasting:
It is a method of severely heating the concentrated ore (usually sulphide ore) below its melting point in an abundance of air. Once the roasting and exothermic process has begun, no extra heat is required.
${\text{2PbS + 3}}{{\text{O}}_2}\xrightarrow{\Delta }{\text{2PbO }} + {\text{ 2S}}{{\text{O}}_{\text{2}}}$
${\text{2ZnS + 3}}{{\text{O}}_2}\xrightarrow{\Delta }{\text{2ZnO }} + {\text{ 2S}}{{\text{O}}_{\text{2}}}$
${\text{2CuFe}}{{\text{S}}_{\text{2}}} + 4{{\text{O}}_{\text{2}}} \to {\text{C}}{{\text{u}}_{\text{2}}}{\text{S}} + {\text{2FeO}} + 3{\text{S}}{{\text{O}}_{\text{2}}}$
Self-reduction, auto-reduction, and air-reduction are among the terms used to describe the direct reduction of sulphide ore into metal by heating it in air. The ${\text{S}}{{\text{O}}_{\text{2}}}$ generated is used in the production of ${{\text{H}}_{\text{2}}}{\text{S}}{{\text{O}}_{\text{4}}}{\text{.}}$
2.3.2 Reduction of Metal Oxide to the Metal
After that, the calcined or roasted ore is converted to a metallic form in one of two ways.
2.3.2.1 Reduction by Carbon(Smelting)
Smelting is the process of reducing an oxide with carbon at a high temperature. The oxides of less electropositive metals such as ${\text{Pb,Zn,Fe,Cu}}$ and others are reduced in the blast furnace by heating them vigorously with coal or coke. Slag is a flammable substance that forms during the reduction process. Slag is made up of two parts: gangue and substance (for removing gangue) Fluxes are substances that are used to remove gangue. Acidic fluxes: \[{\text{Si}}{{\text{O}}_{\text{2}}}{\text{,}}\] borax (remove basic impurity). ${\text{MgO,MgC}}{{\text{O}}_{\text{3}}}{\text{,CaC}}{{\text{O}}_{\text{3}}}$ are basic fluxes (remove acidic impurity).
When the melting point of a compound is too high, Al powder is used as a reducing agent, and the result is thermite, which is referred to as the Gold-Schmidt Alumino Thermite method. Coke isn’t helpful for s-block oxide and ${\text{A}}{{\text{l}}_{\text{2}}}{{\text{O}}_{\text{3}}}$ isn’t helpful for d-block oxide due to the presence of metal carbides. ${\text{CaO }} + {\text{ 2C}} \to {\text{Ca}}{{\text{C}}_{\text{2}}}{\text{ }} + {\text{ CO}}$
Examples of Some Reaction are:
${\text{CuO }} + {\text{ CO}} \to {\text{C}}{{\text{O}}_{\text{2}}}{\text{ }} + {\text{ Cu}}$
${\text{ZnO }} + {\text{ CO}} \to {\text{C}}{{\text{O}}_{\text{2}}}{\text{ }} + {\text{ Zn}}$
\[{\text{PbO }} + {\text{ C}} \to {\text{CO }} + {\text{ Pb}}\]
Acidic fluxes: ${\text{Si}}{{\text{O}}_2}{\text{ }} + {\text{ CaC}}{{\text{O}}_{\text{3}}}\xrightarrow{\Delta }{\text{CaSi}}{{\text{O}}_3}{\text{ }} + {\text{ C}}{{\text{O}}_{\text{2}}} \uparrow $
Basic fluxes: ${\text{Si}}{{\text{O}}_2}{\text{ }} + {\text{ MgC}}{{\text{O}}_{\text{3}}}\xrightarrow{\Delta }{\text{MgSi}}{{\text{O}}_3}{\text{ }} + {\text{ C}}{{\text{O}}_{\text{2}}} \uparrow $
2.3.2.2: Self Reduction:
Certain metal compounds are reduced to metal without the use of additional reducing agents, such as ores of ${\text{Cu,Pb and Hg}}{\text{.}}$ To produce oxide, their sulfide ores are partially roasted. The residual sulfide ore now reduces this oxide to metal at high temperatures in the absence of air. Self-reduction is the term for this procedure. or automatic lowering. ${\text{Pb}}$ reduces through self-reduction. The reactions are shown below.
${\text{2PbS}} + {\text{3}}{{\text{O}}_{\text{2}}} \to {\text{2PbO}} + {\text{2S}}{{\text{O}}_{\text{2}}}$
${\text{PbS}} + {\text{2PbO}} \to 3{\text{Pb}} + {\text{S}}{{\text{O}}_{\text{2}}}$
2.3.2.3: Metal Displacement Method:
The ore is converted into a water soluble chemical in this technique. The compound's aqueous solution is reacted with a more electropositive metal, which causes the metal to be displaced from the solution. For example, (i) Zairvogel process of silver. (ii) Separation of silver by complex formation
Silver and gold are extracted using a complicated forming procedure. In the presence of air, powdered argentite is reacted with a dilute solution of sodium cyanide. The ore's silver dissolves in the cyanide solution, resulting in sodium argentocyanide.
${\text{A}}{{\text{g}}_{\text{2}}}{\text{S}} + {\text{4NaCN}} \to {\text{2Na}}\left[ {{\text{Ag}}{{\left( {{\text{CN}}} \right)}_{\text{2}}}} \right] + {\text{N}}{{\text{a}}_{\text{2}}}{\text{S}}$
When metallic zinc is introduced to the complex salt solution, it displaces silver from the solution since it is a more electropositive element than silver.
${\text{2Na}}\left[ {{\text{Ag}}{{\left( {{\text{CN}}} \right)}_{\text{2}}}} \right] + {\text{Zn}} \to {\text{N}}{{\text{a}}_2}\left[ {{\text{Zn}}{{\left( {{\text{CN}}} \right)}_{\text{4}}}} \right] + {\text{2Ag}}$
2.3.2.4: Electrolytic Reduction:
This method is typically used to extract highly electropositive metals. Electrolysis is performed in large cells with the addition of a small amount of another suitable electrolyte that: (a) lowers the melting point of the main electrolyte (b) improves its conductivity (c) reduces corrosion problems. For example, ${\text{Na,Mg,K,Al,Ca}}{\text{.}}$
(a) Manufacture of metallic sodium(Down’s process)
Between the graphite anode and the iron cathode, molten ${\text{NaCl}}$ with a trace of ${\text{CaC}}{{\text{l}}_{\text{2}}}$ is electrolyzed. The numerous reactions that occur are as follows:
On fusion: ${\text{NaCl}} \to {\text{N}}{{\text{a}}^ + } + {\text{C}}{{\text{l}}^ - }$
At cathode: ${\text{N}}{{\text{a}}^ + } + {{\text{e}}^ - } \to {\text{Na}}$
At anode: ${\text{2C}}{{\text{l}}^ - } \to {\text{C}}{{\text{l}}_{\text{2}}} + 2{{\text{e}}^ - }$
(b) Hall-Heroult process (electrolytic reduction):
Purified ${\text{A}}{{\text{l}}_{\text{2}}}{{\text{O}}_{\text{3}}}$ is combined with ${\text{N}}{{\text{a}}_{\text{3}}}{\text{Al}}{{\text{F}}_{\text{6}}}$ (cryolite) or ${\text{Ca}}{{\text{F}}_{\text{2}}}$ (fluorspar), lowering the melting point and increasing conductivity. Electrolysis is employed to dissolve the fused matrix. The cathode is steel, and the anode is graphite. The graphite anode is important for metal reduction. The entire reaction can be summarised as follows:
${\text{2A}}{{\text{l}}_2}{{\text{O}}_{\text{3}}} + 3{\text{C}}\xrightarrow{\Delta }{\text{4Al }} + {\text{ 3C}}{{\text{O}}_{\text{2}}} \uparrow $
Electrolysis of the molten mass takes place in an electrolytic cell with carbon electrodes. ${\text{CO}}$ and ${\text{C}}{{\text{O}}_{\text{2}}}$ are produced when the oxygen liberated at the anode reacts with the carbon of the anode. This method burns away around ${\text{0}}{\text{.5 kg}}$ of carbon anode for every kilogramme of aluminium produced. The electrolytic reactions are:
At cathode: ${\text{A}}{{\text{l}}^{3 + }} + 3{{\text{e}}^ - } \to {\text{Al}}$
At anode: ${\text{C}} + {\text{O}}_{\text{2}}^ - \to {\text{CO}} + 2{{\text{e}}^ - }$
2.4: Purification or Refining of Metals
Metals acquired through reduction methods still have some undesirable impurities and must be purified. Refining procedures differ greatly from metal to metal and also rely on the intended application of the metal.
2.4.1: Liquation process:
This procedure is used to purify a metal that is readily fusible in itself but not with the impurities existing in it, i.e. the impurities are infusible. To put it another way, the melting point of the pure metal should be lower than the melting point of each of the metal's impurities. his procedure is used to purify ${\text{Sn}}$ and ${\text{Zn,}}$ as well as to remove ${\text{Pb}}$ from ${\text{Zn}} - {\text{Hg}}$ alloy, which is produced by Parke's process and contains Pb as an impurity.
2.4.2 Distillation Process:
This procedure is used to purify metals that are volatile but contain non volatile contaminants, and vice versa. This procedure purifies ${\text{Cd,Zn and Hg}}{\text{.}}$
2.4.3 Zone Refining Method(Fractional Crystallization Method)
This method is employed when extremely pure metals are required for a specific application. Pure Si and Ge, for example, are utilized in semiconductors and are thus purified via this approach. The zone refining method works on the idea that an impure molten metal will deposit pure metal crystals as it cools, while the impurities will stay in the residual molten metal.
2.4.4 Chromatographic Methods:
This method is based on the idea that different components of a mixture are adsorbed on an adsorbent in distinct ways. The combination is poured into a liquid or gaseous media and passed through the adsorbent. At different levels on the column, different components are adsorbed. The adsorbed components are then eluted (removed) using a suitable solvent (eluant).
2.4.5 Electrolytic Refining: Electrolytic refining is used to refine some metals, such as ${\text{Cu,Ni and Al}}{\text{.}}$ The Hoope's technique is an electrolytic aluminium refining method. The Hooper's cell, which has three liquid layers, has impure aluminum as the anode and pure aluminum as the cathode. The bottom layer is molten impure ${\text{Al,}}$ the middle layer is a fused salt layer containing aluminium fluoride, and the top layer is a pure ${\text{Al}}{\text{.}}$ ${\text{Al}}$ flows through solution as aluminium ion $\left( {{\text{A}}{{\text{l}}^{3 + }}} \right)$ at the anode (bottom layer), and these ions are converted to pure metal at the cathode (top layer). When the cell is turned on, molten metal is added to the bottom and pure aluminium is extracted from the top. The recovered aluminium is 99.98 percent pure.
At cathode: ${\text{A}}{{\text{l}}^{3 + }} + 3{{\text{e}}^ - } \to {\text{Al}}$
At anode: ${\text{Al}} \to {\text{A}}{{\text{l}}^{3 + }} + 3{{\text{e}}^ - }$
2.4.6 Vapour Phase Refining:
This process involves converting the metal to its volatile component, which is subsequently collected. It is then heated until it decomposes, yielding pure metal. In order to refine the vapour phase, the following two prerequisites must be met.
(iThe metal should react with a reagent to generate a volatile chemical.
(ii) The volatile chemical should decompose easily, allowing for easy recovery.
Some Important Compounds, Minerals, Mixtures & The Formula
1. Epsom salt | ${\text{MgS}}{{\text{O}}_{\text{4}}}{\text{.7}}{{\text{H}}_{\text{2}}}{\text{O}}$ | 21. Nitrolium | ${\text{CaC}}{{\text{N}}_{\text{2}}}$ |
2. Gypsum salt | ${\text{CaS}}{{\text{O}}_{\text{4}}}{\text{.2}}{{\text{H}}_{\text{2}}}{\text{O}}$ | 22. Hydrolith | ${\text{Ca}}{{\text{H}}_{\text{2}}}$ |
3. Glauber’s salt | ${\text{N}}{{\text{a}}_2}{\text{S}}{{\text{O}}_{\text{4}}}{\text{.10}}{{\text{H}}_{\text{2}}}{\text{O}}$ | 23. Fusion mixture | ${\text{N}}{{\text{a}}_2}{\text{C}}{{\text{O}}_3} + {{\text{K}}_{\text{2}}}{\text{C}}{{\text{O}}_{\text{3}}}$ |
4. Lime water | ${\text{Ca}}{\left( {{\text{OH}}} \right)_{\text{2}}}$ | 24. Gun powder | ${\text{KN}}{{\text{O}}_3} + {{\text{K}}_{\text{2}}}{\text{C}}{{\text{O}}_{\text{3}}}$ |
5. Quick lime | ${\text{CaO}}$ | 25. Pink salt | ${\left( {{\text{N}}{{\text{H}}_{\text{4}}}} \right)_{\text{2}}}{\text{SnC}}{{\text{l}}_{\text{6}}}$ |
6. Washing Soda | ${\text{N}}{{\text{a}}_2}{\text{C}}{{\text{O}}_3}{\text{.10}}{{\text{H}}_{\text{2}}}{\text{O}}$ | 26. Laughing gas | ${{\text{N}}_{\text{2}}}{\text{O}}$ |
7. Crystal carbonate | ${\text{N}}{{\text{a}}_2}{\text{C}}{{\text{O}}_3}{\text{.}}{{\text{H}}_{\text{2}}}{\text{O}}$ | 27 Red Lead | ${\text{P}}{{\text{b}}_3}{{\text{O}}_4}$ |
8. Soda ash | ${\text{N}}{{\text{a}}_2}{\text{C}}{{\text{O}}_3}$ | 28 Blue vitriol | ${\text{CuS}}{{\text{O}}_{\text{4}}}{\text{.5}}{{\text{H}}_{\text{2}}}{\text{O}}$ |
9. Baking Soda | ${\text{NaHC}}{{\text{O}}_3}$ | 29. Green vitriol | ${\text{FeS}}{{\text{O}}_{\text{4}}}{\text{.7}}{{\text{H}}_{\text{2}}}{\text{O}}$ |
10. Turnbull’s blue | ${\text{F}}{{\text{e}}_{\text{3}}}{\left[ {{\text{Fe}}{{\left( {{\text{CN}}} \right)}_{\text{6}}}} \right]_{\text{2}}}$ | 30. Chiense white | ${\text{ZnO}}$ |
11. Chile saltpetre | ${\text{NaN}}{{\text{O}}_3}$ | 31. Philospher’s wool | ${\text{ZnO}}$ |
12. Indian salt petre | ${\text{KN}}{{\text{O}}_3}$ | 32. Potash alum | ${{\text{K}}_{\text{2}}}{\text{S}}{{\text{O}}_{\text{4}}}{\text{.A}}{{\text{l}}_{\text{2}}}{\left( {{\text{S}}{{\text{O}}_{\text{4}}}} \right)_{\text{3}}}{\text{.24}}{{\text{H}}_{\text{2}}}{\text{O}}$ |
13. Brine or Table salt | ${\text{NaCl}}$ | 33. Chrome alum | ${{\text{K}}_{\text{2}}}{\text{S}}{{\text{O}}_{\text{4}}}{\text{.C}}{{\text{r}}_{\text{2}}}{\left( {{\text{S}}{{\text{O}}_{\text{4}}}} \right)_{\text{3}}}{\text{.24}}{{\text{H}}_{\text{2}}}{\text{O}}$ |
14. Potash ash or pearl ash | ${{\text{K}}_2}{\text{C}}{{\text{O}}_3}$ | 34. Ferric alum | ${\text{F}}{{\text{e}}_{\text{2}}}{\left( {{\text{S}}{{\text{O}}_{\text{4}}}} \right)_{\text{3}}}{\text{.}}{\left( {{\text{N}}{{\text{H}}_{\text{4}}}} \right)_2}{\text{S}}{{\text{O}}_4}{\text{.24}}{{\text{H}}_{\text{2}}}{\text{O}}$ |
15. Salt Cake | ${{\text{K}}_2}{\text{S}}{{\text{O}}_4}$ | 35. Pyrolusite | ${\text{Mn}}{{\text{O}}_{\text{2}}}$ |
16.Carnallite | ${\text{KCl}}{\text{.MgC}}{{\text{l}}_2}.{\text{6}}{{\text{H}}_{\text{2}}}{\text{O}}$ | 36. Aqua Regia | ${\text{conc}}{\text{.HN}}{{\text{O}}_{\text{3}}} + {\text{conc}}{\text{.HCl}}$ |
17.Hypo | ${\text{N}}{{\text{a}}_{\text{2}}}{{\text{S}}_{\text{2}}}{{\text{O}}_{\text{3}}}{\text{.5}}{{\text{H}}_{\text{2}}}{\text{O}}$ | 37. Sodium alum | ${\text{N}}{{\text{a}}_{\text{2}}}{\text{S}}{{\text{O}}_{\text{4}}}{\text{.A}}{{\text{l}}_{\text{2}}}{\left( {{\text{S}}{{\text{O}}_{\text{4}}}} \right)_{\text{3}}}{\text{.24}}{{\text{H}}_{\text{2}}}{\text{O}}$ |
18.Borax | ${\text{N}}{{\text{a}}_{\text{2}}}{{\text{B}}_{\text{4}}}{{\text{O}}_{\text{7}}}{\text{.10}}{{\text{H}}_{\text{2}}}{\text{O}}$ | 38. Killed salt | ${\text{ZnC}}{{\text{l}}_{\text{2}}}{\text{.2}}{{\text{H}}_{\text{2}}}{\text{O}}$ |
19.Baryta water | ${\text{Ba}}{\left( {{\text{OH}}} \right)_{\text{2}}}$ | 39. Ammonium alum | ${\left( {{\text{N}}{{\text{H}}_{\text{4}}}} \right)_{\text{2}}}{\text{S}}{{\text{O}}_{\text{4}}}{\text{.A}}{{\text{l}}_{\text{2}}}{\left( {{\text{S}}{{\text{O}}_{\text{4}}}} \right)_{\text{3}}}{\text{.24}}{{\text{H}}_{\text{2}}}{\text{O}}$ |
20. Magnesia | ${\text{MgO}}$ | 40. Oxymuriate | ${\text{SnC}}{{\text{l}}_4}{\text{.5}}{{\text{H}}_{\text{2}}}{\text{O}}$ |
Extraction of Some Metals:
(A) Magnesium
Electrolysis of fused oxide of fused anhydrous magnesium chloride is commonly employed to remove it.
(i) From magnesite:
Magnesite $\left( {{\text{MgC}}{{\text{O}}_{\text{3}}}} \right)$ is calcined to produce magnesium oxide (magnesia).
${\text{MgC}}{{\text{O}}_{\text{3}}}\xrightarrow{\Delta }{\text{MgO }} + {\text{ C}}{{\text{O}}_{\text{2}}} \uparrow $
Magnesium can be extracted from magnesium oxide using electrolysis or thermal reduction. The oxide is dissolved in a molten combination of magnesium, barium, and sodium fluorides. At $650^\circ {\text{C,}}$ molten mixtures are electrolyzed employing carbon rods as anodes suspended in the molten mass and cast iron rods as cathodes. Magnesium is obtained in a molten state through electrolysis. Reducing agents such as carbon, silicon, aluminium, or calcium carbide can be used to thermally reduce magnesium oxide.
${\text{MgO }} + {\text{ C }} \to {\text{Mg }} + {\text{ CO}}$
${\text{2MgO }} + {\text{ Si }} \to 2{\text{Mg }} + {\text{ Si}}{{\text{O}}_2}$
The reduction takes place in a vacuum at $2000^\circ {\text{C}}.$ Magnesium vapours become condensed.
(ii) Anhydrous Magnesium Chloride Electrolysis:
Carnallite is a hydrated substance. It is heated in air first, then in a stream of ${\text{HCl}}$ gas to render it anhydrous.
$\text{MgC}{{\text{l}}_{\text{2}}}\text{.6}{{\text{H}}_{2}}\text{O}\to \text{MgC}{{\text{l}}_{\text{2}}}+\text{6}{{\text{H}}_{2}}\text{O}$
${\text{MgO}}$ or sea water can also be used to make anhydrous magnesium chloride. Chlorine is sprayed upon a red-hot ${\text{MgO}}$ and carbon combination.
${\text{MgO }} + {\text{ C }} + {\text{ C}}{{\text{l}}_{\text{2}}} \to {\text{MgC}}{{\text{l}}_{\text{2}}}{\text{ }} + {\text{ CO}}$
Because the water of crystallization reacts chemically with magnesium chloride to form magnesium oxychloride and finally magnesium oxide, it cannot be dehydrated by heating.
$\text{MgC}{{\text{l}}_{\text{2}}}\text{.6}{{\text{H}}_{2}}\text{O}\xrightarrow{\Delta }\text{MgC}{{\text{l}}_{\text{2}}}.2{{\text{H}}_{\text{2}}}\text{O}\xrightarrow{\Delta }\text{M}{{\text{g}}_{\text{2}}}\text{OCl}\to \text{MgO}\to \text{Mg}$
Magnesium compounds can be found in seawater. When magnesium hydroxide precipitates, it is treated with calcium hydroxide. It's dissolved in a weak ${\text{HCl}}$ solution. When the hydrated magnesium chloride crystallises, the solution becomes more concentrated. As previously said, it is dehydrated.
${\text{Seawater}} + {\text{Ca}}{\left( {{\text{OH}}} \right)_{\text{2}}} \to {\text{Mg}}{\left( {{\text{OH}}} \right)_{\text{2}}}$
${\text{Mg}}{\left( {{\text{OH}}} \right)_{\text{2}}} + 2{\text{HCl}} \to {\text{MgC}}{{\text{l}}_2}.{\text{6}}{{\text{H}}_{\text{2}}}{\text{O}}$
(B) Extraction of Aluminum
Extraction: Bauxite ore, which is commonly contaminated with ferric oxide and silica, is used to extract aluminium. The removal of ferric oxide and silica from bauxite ore is required before it can be electrolyzed. The following three steps are involved in extracting aluminium from bauxite ore. (I) Bauxite ore purification, i.e. elimination of ferric oxide and silica.
(a) Baeyer's Process: This method is mostly used on bauxite ore that contains ferric oxide as a major contaminant.
(b) Hall's Process: This method is mostly used on bauxite ore that contains ferric oxide as a major contaminant.
(c) Serpeck's Process: This method is mostly used on bauxite ore that has silica as a major contaminant.
(C) Extraction of Tin
Tin is obtained by extracting it from cassiterite ore. The ore is commonly found with siliceous debris, iron tungestates $\left( {{\text{FeW}}{{\text{O}}_{\text{4}}}} \right)$ and manganese $\left( {{\text{MnW}}{{\text{O}}_{\text{4}}}} \right).$
(image will be uploaded soon)
(D) Extraction of Lead
Extraction: Galena ore is used to extract lead $\left( {{\text{PbS}}} \right).$ The extraction process consists of the following steps: (I) Ore concentration (ii) Reduction (iii) Purification
(image will be uploaded soon)
(E) Extraction of Iron
The oxide ores of iron, particularly magnetite, haematite, and limonite, are used to extract the metal. The extraction process entails the phases outlined in the flow chart.
${\text{S}} + {{\text{O}}_2} \to {\text{S}}{{\text{O}}_2} \uparrow $
${\text{A}}{{\text{s}}_2}\;{{\text{S}}_3} + {{\text{O}}_2} \to {\text{A}}{{\text{s}}_2}{{\text{O}}_3} + {\text{S}}{{\text{O}}_2} \uparrow $
${\text{Sn}}{{\text{O}}_2} + {\text{C}} \to {\text{Sn}} + {\text{CO}}$
Extraction of Iron:
${Fe_2}{O_3}+CO\xrightarrow{400-700^\circ C}\underset{\text{Spongy iran}}{2Fe}+3CO_2$
$\text{3F}{{\text{e}}_{\text{2}}}{{\text{O}}_{\text{3}}}\text{+ CO}\xrightarrow{\text{300 - 40}{{\text{0}}^{\text{o}}}\text{C}}\text{2F}{{\text{e}}_{\text{3}}}{{\text{O}}_{\text{4}}}\text{+ C}{{\text{O}}_{\text{2}}} \\$
$ \text{F}{{\text{e}}_{\text{3}}}{{\text{O}}_{\text{4}}}\text{+ CO}\xrightarrow{\text{500 - 60}{{\text{0}}^{\text{o}}}\text{C}}\text{3FeO + C}{{\text{O}}_{\text{2}}} \\$
$\text{FeO + CO}\xrightarrow{\text{70}{{\text{0}}^{\text{o}}}\text{C}}\text{Fe + C}{{\text{O}}_{\text{2}}} \\$
${\text{CaC}}{{\text{O}}_3}\mathop \to \limits^{{{1000}^{ - {\text{C}}}}} {\text{CaO}} + {\text{C}}{{\text{O}}_2}$
${\text{CaO}} + {\text{Si}}{{\text{O}}_2} \to {\text{CaSi}}{{\text{O}}_3}$ (Slag)
${{\text{P}}_4}{{\text{O}}_{10}} + 10{\text{C}} \to 4{\text{P}} + 10{\text{CO}}$
${\text{Si}}{{\text{O}}_2} + 2{\text{C}} \to {\text{Si}} + 2{\text{CO}}$
${\text{Mn}}{{\text{O}}_2} + 2{\text{C}} \to {\text{Mn}} + 2{\text{CO}}$
${\text{Si}}{{\text{O}}_2} + {\text{CO}}\xrightarrow{{1200^\circ C}}{\text{Si}} + 2{\text{CO}}$
${\text{Mn}}{{\text{O}}_2} + 2{\text{C}} \to {\text{Mn}} + 2{\text{CO}}$
${{\text{P}}_4}{{\text{O}}_{10}} + 10{\text{C}} \to 4{\text{P}} + 10{\text{CO}}$
${\text{C}} + {{\text{O}}_2} \to {\text{C}}{{\text{O}}_2} \\$
${\text{C}}{{\text{O}}_2} + {\text{C}} \to 2{\text{CO}} \\ $
When molten pig iron is cooled quickly, it becomes white cast iron, which contains carbon in the form of cementite, ${\text{F}}{{\text{e}}_{\text{3}}}{\text{C,}}$ and when it is cooled slowly and steadily, it becomes grey cast iron, which contains carbon in the form of graphite. Cast Iron, sometimes known as pig iron, is the least pure form of commercial iron, with a carbon content of 2.5 to 4.5 percent and traces of impurities such as ${\text{S,P,Mn and Si}}{\text{.}}$
Wrought iron: It is the cleanest type of commercial iron, with a carbon content of 0.12 to 0.25 percent and impurities such as ${\text{S,P,Mn and Si}}$ of 0.3 percent.
(F) Extraction of Copper
Copper is mostly derived from copper pyrites $\left( {{\text{CUFe}}{{\text{S}}_2}} \right).$ The extraction process is broken down into the steps outlined in the flow chart.
${\text{S}} + {{\text{O}}_2} \to {\text{S}}{{\text{O}}_2}$
$2{\text{As}} + 3{{\text{O}}_2} \to 2{\text{A}}{{\text{s}}_2}{{\text{O}}_3}$
${\text{CuFe}}{{\text{S}}_2} + {{\text{O}}_2} \to {\text{C}}{{\text{u}}_2}\;{\text{S}} \cdot + 2{\text{FeS}} + {\text{S}}{{\text{O}}_5}$
$2{\text{FeS}} + 3{{\text{O}}_2} \to 2{\text{FeO}} + 2{\text{S}}{{\text{O}}_4}$
${\text{FeO}} + {\text{Si}}{{\text{O}}_2} \to {\text{FeSi}}{{\text{O}}_3}$
$2{\text{FeS}} + 3{{\text{O}}_2} \to 2{\text{FeO}} + 2{\text{S}}{{\text{O}}_2}$
${\text{FeO}} + {\text{Si}}{{\text{O}}_2} \to {\text{FeSi}}{{\text{O}}_3}$
$2{\text{C}}{{\text{u}}_2}\;{\text{S}} + 3{{\text{O}}_2} \to 2{\text{C}}{{\text{u}}_2}{\text{O}} + 2{\text{S}}{{\text{O}}_3}$
(G) Extraction of Silver
In the lead ore galena, silver is also present in the form of ${\text{A}}{{\text{g}}_{\text{2}}}{\text{S}}$ in the lead ore, galena $\left( {{\text{PbS}}} \right){\text{.}}$ The extracted lead is known as argentiferous lead because it generally contains silver. Prior to the usage of lead, silver is recovered.
${\text{A}}{{\text{g}}_2}\;{\text{S}} + 4{\text{NaCN}} \rightleftharpoons 2{\text{NaAg}}{({\text{CN}})_2} + {\text{N}}{{\text{a}}_2}\;{\text{S}}$
$4{\text{N}}{{\text{a}}_2}\;{\text{S}} + 5{{\text{O}}_2} + 2{{\text{H}}_2}{\text{O}} \to 2{\text{N}}{{\text{a}}_2}{\text{S}}{{\text{O}}_4} + 4{\text{NaOH}} + 2\;{\text{S}}$
$2{\text{NaAg}}({\text{CN}})2 + {\text{Zn}} \to 2{\text{Ag}} + {\text{N}}{{\text{a}}_2}{\text{Zn}}{({\text{CN}})_4}$
Black ppt. of ${\text{Ag}} + {\text{KN}}{{\text{O}}_3}\xrightarrow{{fuse}}$ Compact mass
Steel:
Steel is an iron alloy (ferrite) with 0.25 to 2.5 percent carbon (cementite, ${\text{F}}{{\text{e}}_3}{\text{C}}$) and traces of ${\text{S,P,Mn and Si}}{\text{.}}$ As a result, the carbon content of steel lies somewhere between that of wrought iron and that of cast iron. Sulfur and Phosphorus are unwanted contaminants. Depending on the process of steel production, the percentage of Sulfur and Phosphorus is usually less than 0.05 percent. ${\text{Si}}$ is found in the form of iron silicide, ${\text{FeSi,}}$ which is soluble in ferrite and has a concentration of 0.15 to 0.35 percent. Steel has a fibrous structure due to its high ${\text{Si}}$ concentration. ${\text{Mn}}$ is added to steel throughout the manufacturing process to act as a deoxidizer and to counteract the detrimental effects of sulphur by creating ${\text{MnS,}}$ which is inert, whereas, ${\text{FeS,}}$ causes steel to become brittle when heated.
Varieties of Steel: Steel comes in a variety of shapes and sizes, depending on the quantity of carbon in it.
1. Mild and Quenched Steels: Mild steel is a type of steel with a lower carbon content. It combines the qualities of wrought iron with steel's flexibility and toughness. Mild steel becomes as hard and brittle as glass when heated to a high temperature (i.e., bright redness) and then quickly cooled by plunging in oil or water. his is referred to as quenched steel, and the process is referred to as quenching or hardening.
2. Hard Steel: This type of steel has a greater carbon content. It's like glass in terms of hardness and brittleness.
3. Alloy Steels or Special Steels: Small amounts of nickel, cobalt, chromium, tungsten, molybdenum, manganese, and silicon are added to steel to give it unique qualities such as hardness, tenacity, corrosion resistance, and coefficient of expansion. These materials are known as special steels or alloy steels, and they are widely used in industry.
4. ${\text{S}}$ and ${\text{P}}$-containing steel. When iron or steel contains too much ${\text{S,}}$ it becomes brittle when hot (hot short), and when it contains too much ${\text{P,}}$ it becomes brittle when cold (cold short).
Steel Manufacturing
The carbon content of steel is halfway between that of cast iron and that of wrought iron, implying that steel can be made either by removing carbon from cast iron or by adding carbon to wrought iron. As a result, steel is made from either cast iron or wrought iron. Following are the methods:
(A) Bessemer’s Process: This method is based on the fact that imperfections in cast iron are totally oxidized in the presence of hot air blast, resulting in almost wrought iron. This is then combined with a known amount of spiegeleisen, a ${\text{Fe,Mn and C}}$ alloy, to produce steel.
The inside of the converter is lined with silica (acidic lining) or lime /magnesia depending on the type of the impurities contained in the cast iron (basic lining). If the cast iron contains impurities such as ${\text{S,C,Mn and Si}}$, silica lining is utilised, and the process is known as Bessemer's acid process. When cast iron contains ${\text{P}}$ as an impurity, however, a ${\text{CaO/MgO}}$ liner is utilised, and the technique is known as the basic Bessemer's process. In practise, basic lining is created by combining ${\text{CaO}}$ and ${\text{MgO}}$ with tar to bond them together. As will be seen in the following discussion, the materials utilised to line the convertor $\left( {{\text{CaO}},{\text{MgO,Si}}{{\text{O}}_2}} \right)$ operate as flux.
Reactions Involved in Bessemer’s Process: (i) In the beginning, ${{\text{O}}_2}$ oxidizes ${\text{P,Mn and Si}}$ (impurities) to their respective oxides.
${\text{Si}} + {{\text{O}}_{\text{2}}} \to {\text{Si}}{{\text{O}}_2}$
$2{\text{Mn}} + {{\text{O}}_{\text{2}}} \to 2{\text{MnO}}$
${\text{MnO}}$ generated in this manner interacts with the Bessemer's converter ${\text{Si}}{{\text{O}}_{\text{2}}}$ lining (acidic lining) to make ${\text{MnSi}}{{\text{O}}_{\text{3}}}$ slag, which is then removed. ${\text{MnO}}$ (basic impurity) + ${\text{Si}}{{\text{O}}_{\text{2}}}$ (acidic lining, which acts as an acidic flux) = ${\text{MnSi}}{{\text{O}}_{\text{3}}}$ (slag). ${{\text{P}}_{\text{2}}}{{\text{O}}_{\text{5}}}$ and ${\text{Si}}{{\text{O}}_{\text{2}}}$ created react with the Bessemer's convertor's ${\text{CaO}}$ liner (basic lining) to form ${\text{C}}{{\text{a}}_{\text{3}}}{\left( {{\text{P}}{{\text{O}}_{\text{4}}}} \right)_{\text{2}}}$ and ${\text{CaSi}}{{\text{O}}_{\text{3}}}$ slags, which are then removed. ${{\text{P}}_{\text{2}}}{{\text{O}}_{\text{5}}}$ (acidic impurity) + ${\text{CaO}}$ (basic lining acting as a basic flux) ${\text{C}}{{\text{a}}_{\text{3}}}{\left( {{\text{P}}{{\text{O}}_{\text{4}}}} \right)_{\text{2}}}$ (slag) ${\text{Si}}{{\text{O}}_{\text{2}}}$ (acidic impurity) + ${\text{CaO}}$ (basic lining acting as a basic flux) ${\text{CaSi}}{{\text{O}}_{\text{3}}}$ (acidic impurity) + ${\text{CaO}}$ (basic lining acting as a basic flux) ${\text{CaSi}}{{\text{O}}_{\text{3}}}$ (slag). Basic slag, which is a mixture of the three slags ${\text{MnSi}}{{\text{O}}_{\text{3}}}$ ${\text{C}}{{\text{a}}_{\text{3}}}{\left( {{\text{P}}{{\text{O}}_{\text{4}}}} \right)_{\text{2}}}$ and ${\text{CaSi}}{{\text{O}}_{\text{3}}}$ is used as a fertilizer. The fluxes ${\text{Si}}{{\text{O}}_{\text{2}}}$ ${\text{CaO}}$ and ${\text{MgO}}$ which are employed to line the convertor, are clearly seen in this discussion.
1. The Blast of Air Later Oxidizes
${\text{C}}$ and ${\text{S}}$ to ${\text{CO}}$ and ${\text{S}}{{\text{O}}_{\text{2}}}$ respectively.
${\text{S}}{{\text{O}}_{\text{2}}}$ escapes from the convertor's mouth, while ${\text{CO}}$ burns with a blue flame at the Bessmer convertor's mouth (Bessemer's condles). The burning of ${\text{CO}}$ at the convertor's mouth ceases after all of the carbon in the cast iron has been oxidised to ${\text{CO}}{\text{.}}$ The blowing of ${{\text{O}}_{\text{2}}}$ into the convertor comes to a halt at this point. The formation of slags should be mentioned here. Manganese steel is formed after the removal of impurities, and then a tiny amount of spiegeleisen alloy is mixed to the molten cast iron.
The manganese alloy formed has several functions. Some of them are:
(a. )It functions as a deoxidizer, as Mn in the alloy lowers oxidized iron if any is present.
(b). The alloy provides the necessary amount of carbon, \[{\text{Mn,}}\] and ${\text{Fe}}$ to produce steel with the desired composition. It's worth noting that carbon is a necessary component of all types of steel. \[{\text{Mn}}\] hardens steel and improves its tensile strength.
2. The Siemens-Martin Open-Hearth Process
This is the current method, and the furnace employed is known as an open-hearth furnace. This furnace is also known as a regenerative furnace since it operates on the regenerative principle of heat economy. Steel is made from cast iron via this technique. An open hearth is used in an open-hearth furnace. Depending on the nature of impurities present in pig or cast iron, the hearth is lined with silica or calcined dolomite. If the impurities are manganese, silicon, or other metals, silica lining is employed, and calcined dolomite lining is utilised if there is a lot of phosphorus.
Pig or cast iron, scraps, iron ore (haematite), and lime make up the charge. The charge is heated on the furnace's hearth. The iron ore oxidizes the impurities.
${\text{CaO}} + {\text{Si}}{{\text{O}}_{\text{2}}} \to {\text{CaSi}}{{\text{O}}_{\text{3}}}$
${\text{MnO}} + {\text{Si}}{{\text{O}}_{\text{2}}} \to {\text{MnSi}}{{\text{O}}_{\text{3}}}$
${\text{2F}}{{\text{e}}_2}{{\text{O}}_3} + 3{\text{Si}} \to 4{\text{Fe}} + 3{\text{Si}}{{\text{O}}_2}$
${\text{10F}}{{\text{e}}_2}{{\text{O}}_3} + 12{\text{P}} \to 20{\text{Fe}} + 3{{\text{P}}_4}{{\text{O}}_{10}}$
Steel samples are drawn and checked for carbon content on a regular basis. Finally, spiegleisen (an iron-manganese-carbon alloy) is added to the molten mass to produce the desired steel. The entire procedure takes approximately 8 to 10 hours to complete. The procedure is more time consuming than the Bessemer process. In comparison to Bessemer's process, the open-hearth process provides the following advantages.
(i). Because the heating is done externally, the temperature can be adjusted.
(ii). Because it is a slower process, it can be better regulated. Composition and quality can be carefully managed.
(iii). This method loses only 4% of the iron that Bessemer's process loses, whereas Bessemer's process loses roughly 15%.
3. The Duplex Method
Now-a-days Steel is manufactured in massive quantities using the duplex process. This method is a hybrid of Bessemer's and the open-hearth method. The molten pig iron is first processed in an acid Bessemer's converter to remove ${\text{Si,Mn}}$ and a portion of ${\text{C}}$ in this process. The molten pig iron is then transported to an open-hearth furnace with a basic lining to remove the remaining phosphorus and carbon before being completed as usual. Tata Iron and Steel Works manufactures steel using the Duplex process.
4. The Electric Procedure
Steel is prepared in an arc furnace (also known as Heroult's furnace) in this method. This crucible-shaped furnace is made out of a steel shell that is lined on the interior with dolomite magnesite and topped with heat-resistant bricks.
The Following Reactions Occur Throughout this Process:
(a) Oxidation and slag formation. The charge melts at the temperature of the electric arc, and a violent reaction begins. ${\text{P,C,Mn and Si}}$ are oxidized to ${\text{Si}}{{\text{O}}_{\text{2}}}$ ${\text{MnO}}$ ${\text{CO}}$ and ${{\text{P}}_4}{{\text{O}}_{10}}$ respectively, in this reaction, and ${\text{CaC}}{{\text{O}}_{\text{3}}}$ is decomposed.
${\text{C}}{{\text{O}}_2} + {\text{C}} \to 2{\text{CO}}$
${\text{5}}{{\text{O}}_2} + {{\text{P}}_{\text{4}}} \to {{\text{P}}_{\text{4}}}{{\text{O}}_{{\text{10}}}}$
The oxidized products formed are removed as slag.
${\text{MnO}} + {\text{Si}}{{\text{O}}_{\text{2}}} \to {\text{MnSi}}{{\text{O}}_{\text{3}}}$
${\text{CaO}} + {\text{Si}}{{\text{O}}_{\text{2}}} \to {\text{CaSi}}{{\text{O}}_{\text{3}}}$
${\text{FeO}} + {\text{Si}}{{\text{O}}_{\text{2}}} \to {\text{FeSi}}{{\text{O}}_{\text{3}}}$
Because it is lighter, this slag floats over the metallic component. The furnace is carefully tilted and the slag is poured out of it once the oxidation and production of slag is complete.
(b) Desulfurization and Deoxidation: Following the removal of the slag from the furnace, a charge of lime, sand, fluorspar, coke, and ferro-silicon is added to the furnace. Any ${\text{FeO}}$ present in the steel is reduced to ${\text{Fe}}$ with the addition of coke.
${\text{FeO}} + {\text{C}} \to {\text{Fe}} + {\text{CO}}$
By processing ${\text{FeS}}$ with ${\text{CaO,}}$ sulfur present as ${\text{FeS}}$ is converted to ${\text{CaS}}{\text{.}}$ The ${\text{FeO}}$ generated is immediately converted to ${\text{Fe,}}$, as before, and the ${\text{CaS}}$ is deposited in the slag. When the steel has been desulphurized (that is, the sulfur has been removed), it is put into moulds.
Alloy steels, tool steels, stainless steels, and special quality steels are all made using this procedure. The following are the key benefits of the procedure:
(i) A reduction in capital expenditure and an increase in productivity.
(ii) One batch can be treated in 45 minutes.
(iii) Lower operating costs and higher steel quality.
The process is carried out in a magnesite-lined converter, which varies from the Bessemer converter in that it does not have a perforated bottom and instead has a solid bottom. Through a copper lance, pure air is blown from the top.
Properties of Steel:
Mechanical Characteristics. Steel combines the advantages of cast and wrought iron by being both hard and elastic, and it can be forged and welded as long as the carbon content isn't too high.
Heat Action: Heat Treatment of Steel Steel has a unique property that separates it from other industrial forms of iron: its hardness and flexibility may be altered through adequate heat treatment. Consider the following example:
Annealing- When hard steel is heated to a bright red colour and then allowed to cool slowly, its hardness is greatly reduced and it becomes soft. This is referred to as annealing.
Hardening or Quenching. Mild steel becomes as hard and brittle as glass when heated to a high temperature (i.e., bright redness) and then quickly cooled by immersing it in oil or water. This is referred to as quenching.
Tempering. By heating quenched steel to different temperatures for different lengths of time, it can lose its brittleness. The method. Tempering is the term used to describe the process of bringing steel to a desired hardness and flexibility.
Steel Surface Treatment. The following procedure is used to treat the steel's surface:
Hardening of the Case: Case hardening is the process of applying a thin layer of hardened steel to the surface of mild steel. This is accomplished by first burning the mild steel with charcoal before submerging it in oil.
Nitriding: Nitriding is the process of applying a hard coating of iron nitride on the surface of steel. Steel is heated to $500 - 600^\circ {\text{C}}$ in a dry ammonia environment for 3–4 days, resulting in a hard covering of iron nitride on the surface.
Some Special Process for Silver:
Amalgamation Process: The powdered mineral comprising ${{\text{H}}_2}{\text{O}}$ and ${\text{NaCl}}$ is mixed with mercury and magistral (burnt pyrites-sulphates and copper and iron oxides). The combination is kept in the refrigerator for many days. The amalgam form of silver is created. Silver is collected through washing, drying, and subsequent distillation.
${\text{CuS}}{{\text{O}}_{\text{4}}} + {\text{2NaCl}} \to {\text{CuC}}{{\text{l}}_{\text{2}}} + {\text{2N}}{{\text{a}}_{\text{2}}}{\text{S}}{{\text{O}}_{\text{4}}}$
${\text{CuC}}{{\text{l}}_{\text{2}}} + {\text{2A}}{{\text{g}}_2}{\text{S}} \to {\text{C}}{{\text{u}}_2}{\text{C}}{{\text{l}}_{\text{2}}} + {\text{S}}$
${\text{C}}{{\text{u}}_2}{\text{C}}{{\text{l}}_{\text{2}}} + {\text{A}}{{\text{g}}_2}{\text{S}} \to {\text{C}}{{\text{u}}_2}{\text{S}} + 2{\text{AgCl}}$
$2{\text{AgCl}} + {\text{2Hg}} \to $
${\text{Ag}} + {\text{Hg}} \to {\text{Ag}}\left( {{\text{Hg}}} \right)\xrightarrow{{{\text{distillation}}}}{\text{Ag}} + {\text{Hg}}$
Desilverization of Lead: When a lead-silver alloy has a low silver content (such as argentiferous lead of galena), Parke's technique affects lead desilverisation. It depends on the fact that:
(i) When zinc is added to a melted silver-lead alloy, zinc removes silver from the alloy and forms an alloy with silver rather than lead.
(ii) When zinc is added to a melted silver-lead alloy, zinc removes silver from the alloy and forms an alloy with silver rather than lead.
(iii) When zinc is added to a melted silver-layers.
Pattinson's Method: It all comes down to the fact that a lead-silver alloy with less than 1.8 percent silver melts at a lower temperature than pure lead. When this sort of alloy is melted and allowed to cool, lead separates first, and by repeating the process, the silver content increases. Cupellation is used to complete the recuperation process.
Lead Process: This procedure is based on the fact that when silver ores are melted down with lead, a lead-silver alloy is created, which is then oxidised to remove the lead. Cupellation technique is used to make a silver-rich ${\text{Pb}} - {\text{Ag}}$ alloy. Parke's or Pattinson's technique is used to make a ${\text{Pb}} - {\text{Ag}}$ alloy that is low in silver.
3. Thermodynamic Principles of Metallurgy
The fundamental concepts of thermodynamics are extremely useful in determining which element will be the best reducing agent for a specific oxide during a metallurgical operation. It can also estimate the ideal temperature for the decrease to take place smoothly.
Gibb's Helmholtz free energy change $\left( {\Delta G} \right)$ is given by the equation for any reaction or process.
$\Delta G = \Delta H - T\Delta S$
where $\Delta H$ represents the enthalpy change, $\Delta S$ represents the entropy change, and $T$ represents the absolute temperature at which the change occurs. For the reaction to be spontaneous, the value of $\left( {\Delta G} \right)$ must be negative. The Gibbs free energy is also related to the equilibrium constant $K$ of the temperature.
$\Delta G = - RT\ln K$
In the equation, a negative $\left( {\Delta G} \right)$ implies a positive $K.$ This is only possible if the reaction progresses to the products. The following are some of the inferences that can be drawn:
The reaction is more spontaneous when the negative value of free energy change $\left( {\Delta G} \right)$ is greater.
If two reactions are combined in a system with a net $\left( {\Delta G} \right)$ of negative, the overall reaction will occur, i.e., a reaction with a positive $\left( {\Delta G} \right)$ can be made to occur by coupling it with another reaction with a significant negative $\left( {\Delta G} \right)$ so that the net $\left( {\Delta G} \right)$ of both reactions is negative. Ellingham diagrams make it simple to understand such coupling reactions.
Ellingham Diagram: An Ellingham diagram is a set of graphs that show how the standard free energy of the formation of oxides of various elements varies with temperature, i.e., $\left( {\Delta G} \right)$ versus $T.$ Plots that are similar can also be found. Sulfides and halides should be plotted. H.J.T. Ellingham was the first to plot these. These diagrams assist us in determining whether or not thermal reduction of an ore is feasible.
The metal oxide is formed by,
$2{\text{xM}} + {{\text{O}}_{\text{2}}} \to {\text{2}}{{\text{M}}_{\text{x}}}{\text{O}}$
In the above reaction, the value of $\Delta S$ decreases and, thus, the value of $\Delta S$ is negative.
The slope of the metal oxide formation curves is positive because $\left( {\Delta G} \right)$ becomes less negative or increases as temperature rises.
Except when there is a change in phase $\left( {s \to l,l \to g} \right)$ each curve is a straight line. An increase in the slope on the +ve side indicates the temperature at which such a change occurs. The melting of zinc, for example, is shown by a rapid increase in the positive slope at temperature $692{\text{ K,}}$ in the ${\text{Zn}} - {\text{ZnO}}$ curve.
At high temperatures, $\left( {\Delta G} \right)$ turns positive in less reactive metals such as silver and mercury. Both silver oxide $\left( {{\text{A}}{{\text{g}}_{\text{2}}}{\text{O}}} \right)$ and mercury oxide $\left( {{\text{HgO}}} \right)$ are unstable and breakdown at high temperatures.
$2{\text{A}}{{\text{g}}_{\text{2}}}{\text{O}}\xrightarrow{\Delta }4{\text{Ag}} + {{\text{O}}_{\text{2}}}$
\[2{\text{HgO}}\xrightarrow{\Delta }{\text{2Hg}} + {{\text{O}}_{\text{2}}}\]
As $\Delta S$ grows, $\left( {\Delta G} \right)$ drops in the ${\text{CO}}$ curve. The declining trend demonstrates this.
Any metal oxide with a lower $\left( {\Delta G} \right)$ value is more stable than one with a higher $\left( {\Delta G} \right)$ value. This means the metal oxide at the top of the diagram can be reduced by the metal involved in the production of the oxide at the bottom. ${\text{C}}{{\text{r}}_{\text{2}}}{{\text{O}}_{\text{3}}}$ can be reduced by ${\text{Al}}$ metal, whereas, ${\text{A}}{{\text{l}}_{\text{2}}}{{\text{O}}_{\text{3}}}$ cannot be reduced by ${\text{Cr}}{\text{.}}$
As a result, the relative proclivity of certain metals to serve as reducing agents is determined.
${\text{Ca}} > {\text{Mg}} > {\text{Al}} > {\text{Cr}} > {\text{Zn}} > {\text{Fe}} > {\text{Ni}}$
3.1 Reducing Nature of Carbon
In pyrometallurgical activities, carbon in the form of coke, charcoal, or carbon monoxide is utilized as a reducing agent. Smelting is the word for a reduction process used in metal extraction. The following three reactions are possible when carbon is used as a reducing agent:
${\text{C}} + {{\text{O}}_2} \to {\text{C}}{{\text{O}}_{\text{2}}}$
${\text{2C}} + {{\text{O}}_2} \to 2{\text{CO}}$
${\text{2CO}} + {{\text{O}}_2} \to 2{\text{C}}{{\text{O}}_2}$
(image will be uploaded soon)
There is almost little change in entropy in the first reaction (creation of ${\text{C}}{{\text{O}}_{\text{2}}}$), i.e.$\Delta S = 0,$ and hence $\left( {\Delta G} \right)$ remains virtually constant as temperature rises, i.e., $\left( {\Delta G} \right)$ is temperature independent. The entropy of the second process (the production of $\operatorname{CO} $) increases ($\Delta S$ is positive), therefore $\left( {\Delta G} \right)$ becomes more negative as the temperature rises. However, in the third reaction, entropy decreases ($\Delta S$ is negative), and so $\left( {\Delta G} \right)$ gets less negative as temperature rises.
The intersection of the three curves was discovered at ${\text{983 K}}{\text{.}}$ It means that the reaction (ii) is best suited above this temperature. It indicates that at extremely high temperatures, carbon may reduce any metal oxide and then be oxidized to $\operatorname{CO} .$ However, at high concentrations, the reduction of carbon is not possible in all the cases due to following reasons:
(a). It has a hefty price tag.
(b). At high temperatures, some metals react with carbon to generate carbides.
(c). Maintaining a high temperature poses numerous practical challenges.
(A) Theory of Haematite Reduction Three curves are depicted in the Ellingham diagram: formation of ferric oxide from iron, formation of carbon from carbon, and formation of ${\text{C}}{{\text{O}}_{\text{2}}}$ from carbon. The curve intersects each other at ${\text{1073 K}}.$ The value of $\left( {\Delta G} \right)$ for the formation of ${\text{FeO}}$ is less negative than oxygen above ${\text{1073 K}}.$ Above, ${\text{1073 K}}$ carbon coke can reduce ferric oxide. The $\left( {\Delta G} \right)$ for the reaction is negative.
${\text{F}}{{\text{e}}_{\text{2}}}{{\text{O}}_{\text{3}}} + {\text{3C}} \to {\text{2Fe}} + {\text{3CO}}$
$\left( {\Delta G} \right)$ for ${\text{CO}}$ formation from carbon is less negative below ${\text{1073 K}}$ than $\left( {\Delta G} \right)$ for ${\text{F}}{{\text{e}}_{\text{2}}}{{\text{O}}_{\text{3}}}$ formation. Alternatively, the reduction of ${\text{F}}{{\text{e}}_{\text{2}}}{{\text{O}}_{\text{3}}}$ with carbon will be positive, indicating that no reduction is feasible. However, the $\left( {\Delta G} \right)$ of ${\text{C}}{{\text{O}}_2}$ formation from ${\text{CO}}$ is more negative than $\left( {\Delta G} \right)$ of ${\text{F}}{{\text{e}}_{\text{2}}}{{\text{O}}_{\text{3}}}$ formation, as seen in the diagram. This suggests that ${\text{CO}}$ can reduce ${\text{F}}{{\text{e}}_{\text{2}}}{{\text{O}}_{\text{3}}}$ below ${\text{1073 K}}$ i.e., ${\text{F}}{{\text{e}}_{\text{2}}}{{\text{O}}_{\text{3}}}$ can be lowered by ${\text{CO}}{\text{.}}$
${\text{F}}{{\text{e}}_{\text{2}}}{{\text{O}}_{\text{3}}} + {\text{3CO}} \to {\text{2Fe}} + {\text{3C}}{{\text{O}}_2}$
(B) The Ellingham diagram of the theory of ${\text{ZnO}}$ reduction demonstrates that the curves involving the synthesis of ${\text{ZnO}}$ and carbon monoxide cross at about ${\text{1270 K}}{\text{.}}$ Above ${\text{1180 K,}}$ the value of $\left( {\Delta G} \right)$ for the formation of ${\text{ZnO}}$ increases dramatically. This is owing to the fact that at this temperature, zinc begins to boil. $\left( {\Delta G} \right)$ of the following equation above ${\text{1270 K}}{\text{.}}$
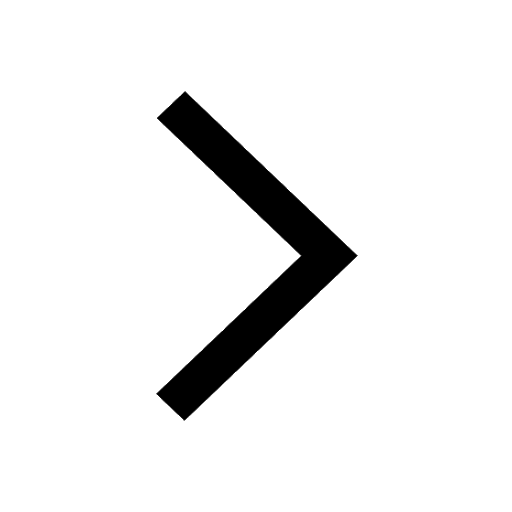
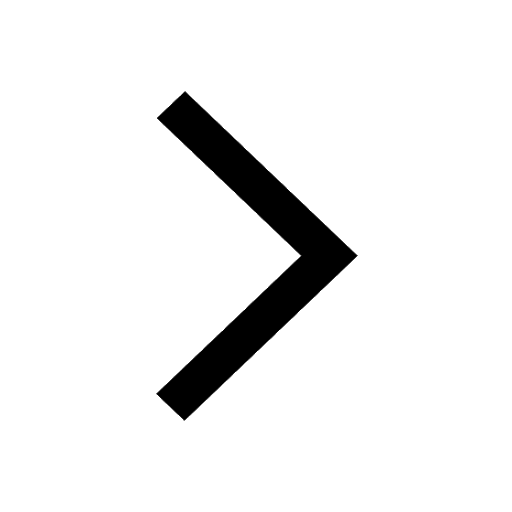
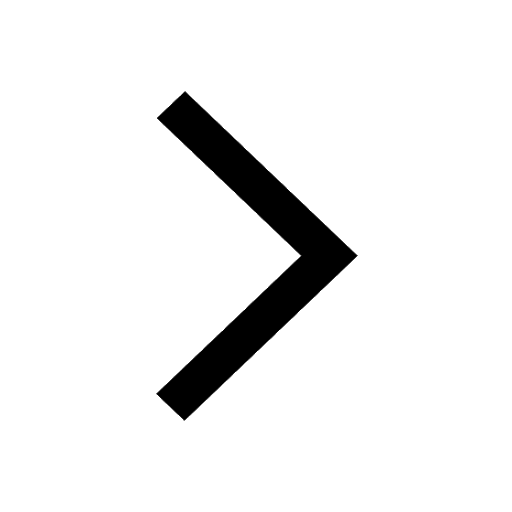
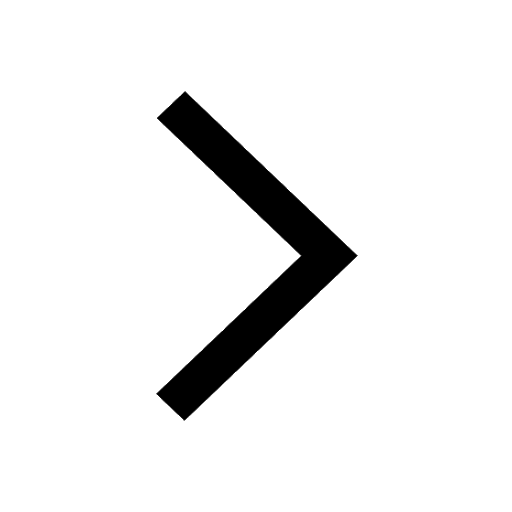
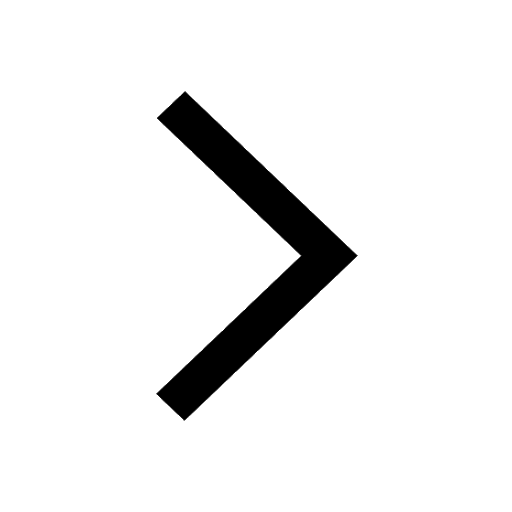
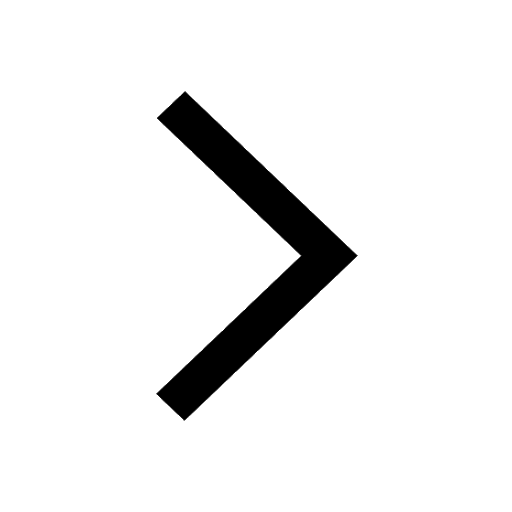
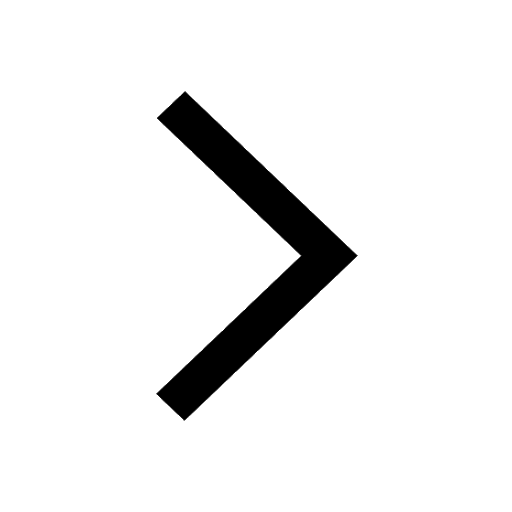
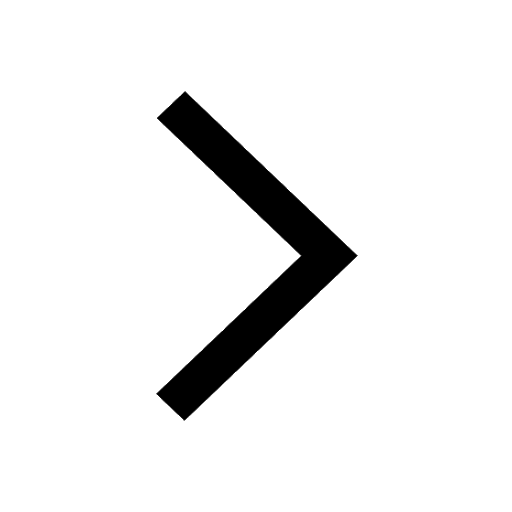
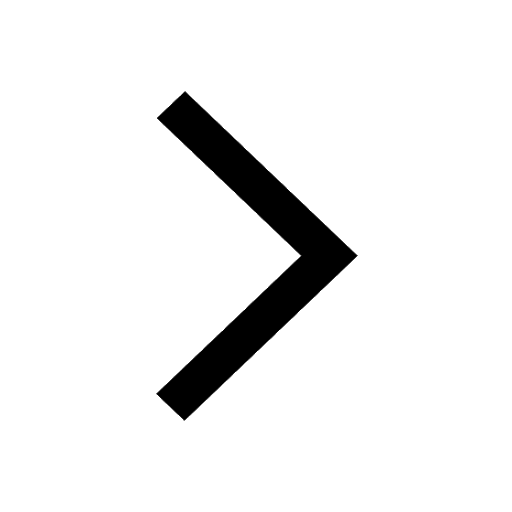
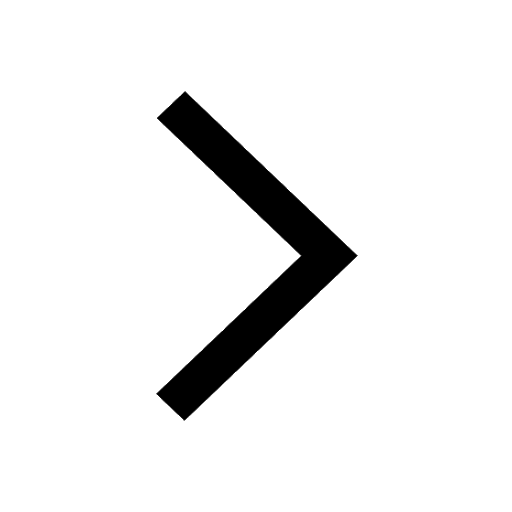
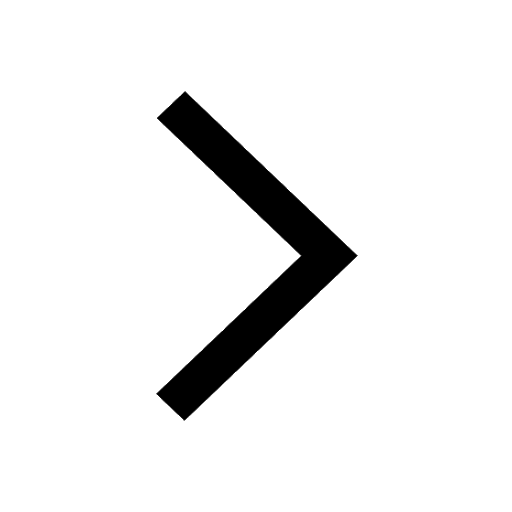
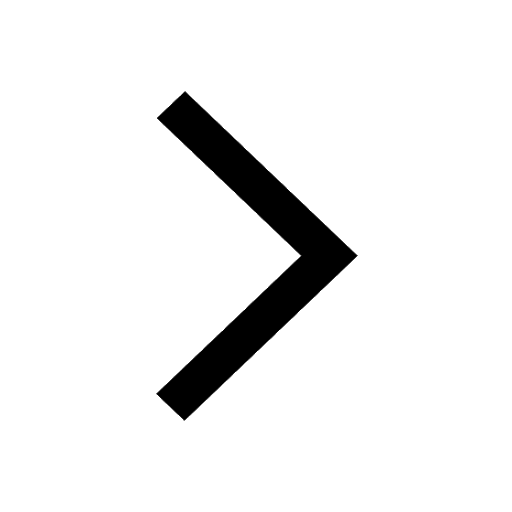
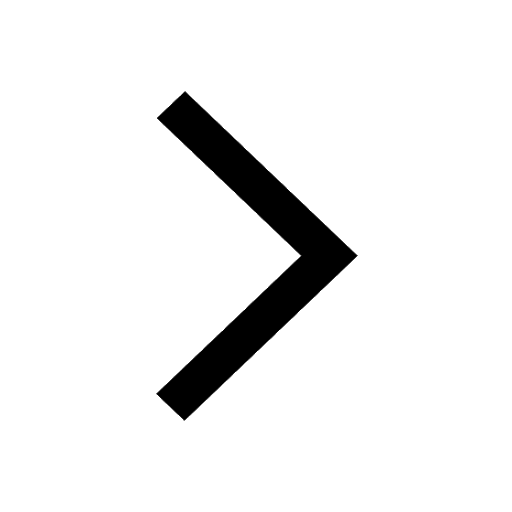
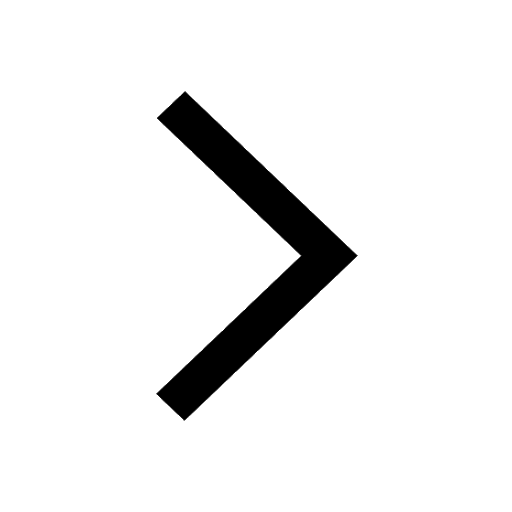
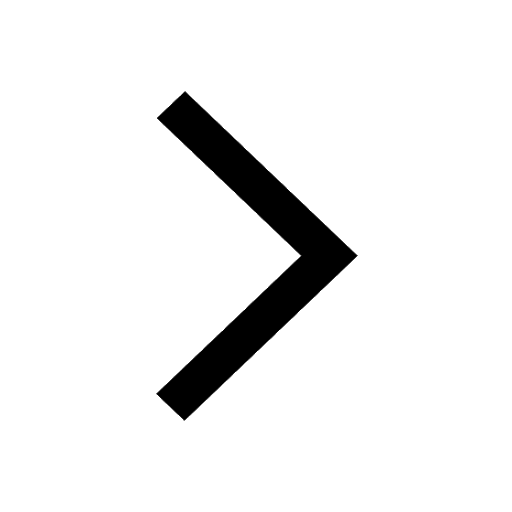
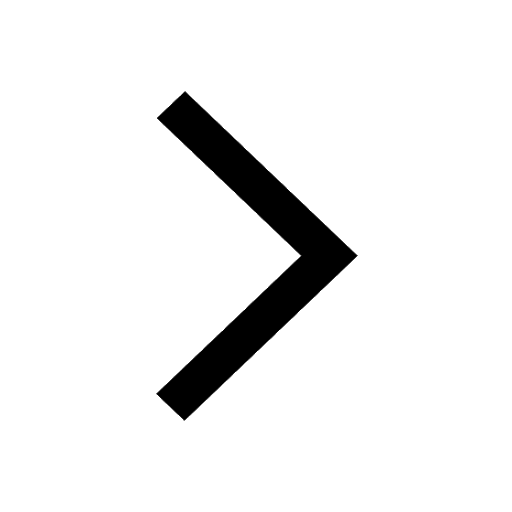
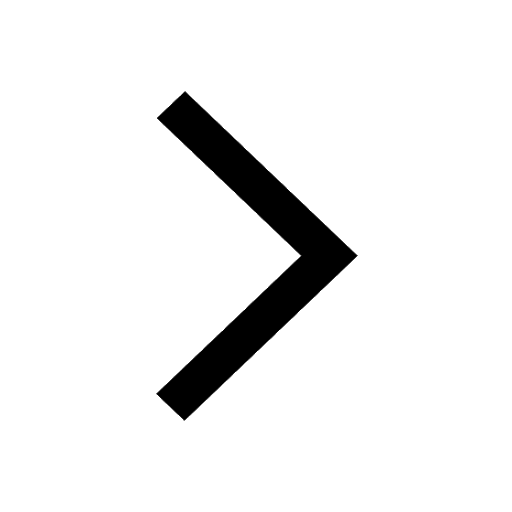
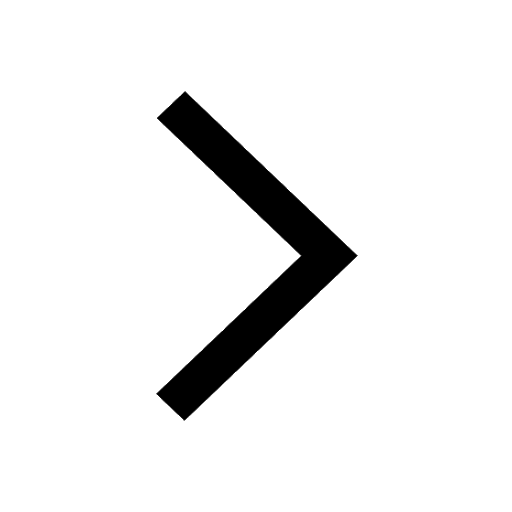
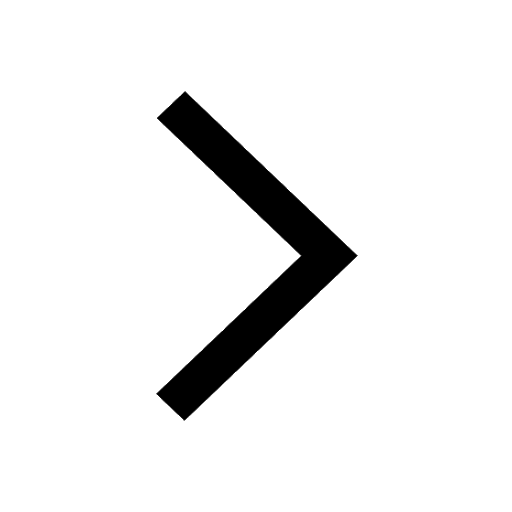
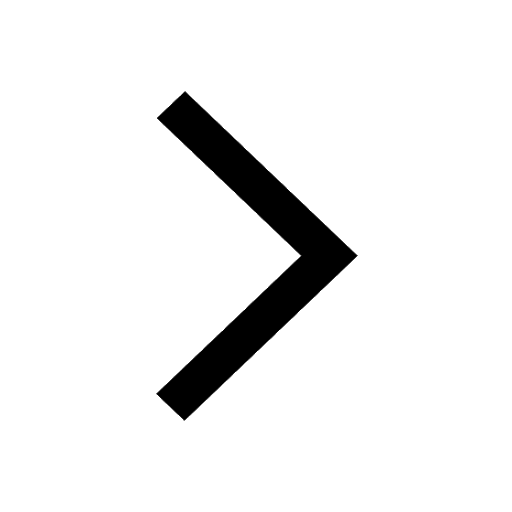
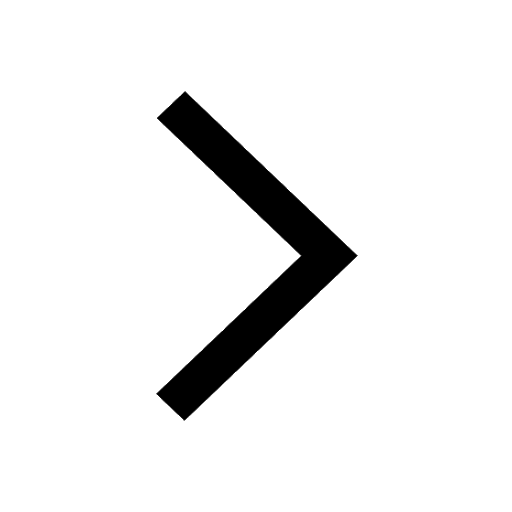
FAQs on General Principles and Processes of Isolation of Elements Class 12 Notes CBSE Chemistry Chapter 6 (Free PDF Download)
1. What are the different types of concentration methods?
The different types of concentration methods are:
Hydraulic washing- This principle is based on the dissimilarities or differences in gravities or densities of the gangue particles and the ore. In this process, a water stream is used to wash dirty ore. This removes lighter particles away leaving the heavy ore behind.
Magnetic separation- This method is based on dissimilarities in the magnetic properties of gangue and ore.
Froth floatation- It is based on the principle of wetting properties of gangue and ore.
Leaching- It depends on the sedimenting properties of ores and gangues.
2. Explain the process of calcination.
Calcination is the process of extracting crude metal from raw concentrated ore. In this process, the ore is heated below its melting point with a limited or no supply of oxygen. While heating the ore, the moisture is expelled into the environment. If the ore is hydrated, then it becomes anhydrous. Carbonated ores change into their respective oxides. For example, Bauxite is converted into alumina and water in the presence of heat. To know more download the Vedantu app.
3. What is roasting?
It is the process of converting ores into their oxides. In roasting, the ore is heated below its melting point in the presence of oxygen. During this process, the ore is treated with an excess amount of air. Changes occurring in this process are-
Moisture is removed from the ore.
Organic matter is destroyed.
Removes oxides of non-metallic impurities like phosphorus, sulphur, arsenic in the form of volatile gases.
Sulphide ores are changed into metal oxides.
4. Explain electrometallurgy.
Electrometallurgy is the process of separating metal from its fused salts through electrolysis. This technique is used to extract highly reactive elements like sodium, calcium, aluminium, etc. There are two methods of extracting highly reactive metals. They are-
Electrolytic reduction is carried out to reduce reactive metals in the solid-state. It’s used when chemical reduction can’t be done.
Electrolysis is done to reduce metals in their molten states.
To understand this process better, visit the page NCERT Notes for Class 12 Chemistry and download the revision notes for free.
5. What is flux?
It is a substance that is added to remove impurities from roasted or calcinated ores. It forms a fusible substance called slag when mixed with ores. Slag is insolvable in molten metal. It is lighter than molten metal and thus, floats on its surface. There are two types of flux.
Acidic flux- It removes alkaline impurities from ores. For example- lime (impurity) removes when silica(acidic flux) is added.
Basic flux- It eliminates acidic impurities like silica from ores. Limestone is an example of basic flux.