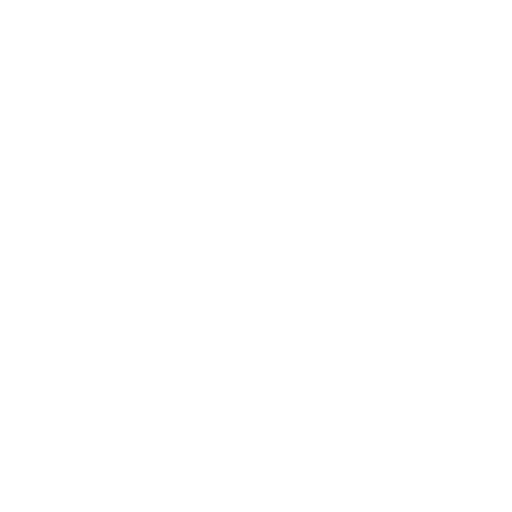
An Introduction
Till the 1970s, the primitive reverberatory furnace innovation remained the most extensively utilised technique for generating copper matte when it started to be knocked out and is now almost obsolete. The generation of huge quantities of dust and gases comprising SO2 at small doses has been the toughest issue with reverberatory smelting. Undoubtedly, because SO2 removal from such gases is complicated and costly, effluent regulation issues have forced the backup of several reverberatory furnaces with electronics, flash, or ongoing copper-making mechanisms. However, as each era passed, the development components altered, resulting in higher manufacturing capabilities, and the modern reverberatory furnace was utilised for smelting metals other than copper. So, this article gives overall information on reverberatory furnaces.
What is a Reverberatory Furnace?
A reverberatory furnace is a type of metallurgy or process furnace that separates the substance getting processed from the gasoline but not from the combustion gases. The word reverberation is utilised in the broad context of recovering or reflecting, as opposed to echoing in an acoustic way.
The modern reverberatory furnace is indeed a kind of furnace that is predominantly utilised to recover the metals copper, aluminium, tin, and nickel as well as to make specific varieties of concrete and cement. The furnace can primarily be utilised to refine and smelt these resources.
Reverberatory Furnace Construction and Process
The reverberatory furnace comprises 2 single-chimney dome-shaped furnaces that are heated by a charcoal grill that reverberates against the roofs and sides of the furnaces, dissolving the iron inside. The reverberatory furnace diagram implies typical, casteless, or refractory blocks containing non-wetting properties border a rectangular steel box utilised to create modern reverberatory furnaces. The entrance at one extremity of the furnace raises vertically, and the burners are typically on the other end. The exhaust gas duct and a pour spout are placed across from the burners. Blocks made of refractory material are generally utilised to build rooftops since they are durable and help to produce high temperatures.
In a reverberatory furnace, heat is typically delivered over the surface that holds the ore mixture. The principal means of heat exchange is radiation through the refractory blocks utilised on the sides and rooftops. The burner provides further heating for the ore. In order to divert the fire for reverberation, the furnace's roof is likewise somewhat arching and slanted towards the flue bridges. The mix is cooked continually until melting occurs.
The thick hearth, which is constructed of a sturdy material which could survive slag breakdown, is where the melted unclean metal is being collected in the meantime. This process is repeated in the furnace till the ore concentration is routinely emptied. The material is then moved to converters for an additional reverberatory furnace process.
Example of Reverberatory Furnace
Chemical extraction of the reverberatory furnace process of dust in an ozone-sulfuric acid media is explained here. Hydrogen peroxide (1.77 V) and chlorine (1.4 V) have substantially lower oxidation potentials (2.07 V) than ozone. The accompanying reverberatory furnace reaction describes how it can convert sulphide species, like chalcopyrite, to soluble sulphates.
3CuFeS2 + 8O3 → 3CuSO4 + 3FeSO4
From the above reverberatory furnace equation, it is clear that when ozone is present, no sulphur layer forms on the particles.
Utilising a responsive surface technique, this approach aims to create ideal circumstances that promote copper dissolving while minimising iron breakdown. Temperature, leaching period, original pH, pulp thickness, and ozone stream speed were considered to account for process parameters, while copper and iron levels in the leaching solutions were utilised as the performance characteristics. The leaching solution's allowed maximum iron level was set at 1 g/L.
Difference between Blast Furnace and Reverberatory Furnace
Interesting Facts
In 1678, Sir Clement Clerke and his son Talbot constructed cupolas or reverberatory furnaces.
Nearly 30 tonnes of copper dust with a copper concentration of around 25% are produced daily by reverberatory furnaces at the Sarcheshmeh Copper Complex in southeast Iran.
The majority of the copper dust's ingredients are sulphide minerals.
There is currently no effective method in place at Sarcheshmeh to recover copper from the flue dust.
Key Features to Remember
A reverberatory furnace is a metallurgy or process furnace that separates the substance getting processed in direct touch with the fuels but not from combust fumes.
It is likely that the initial reverberatory furnaces were utilised throughout the Middle Ages to melt copper for making bells.
In the reverberatory furnace, which consists of 2 single-chimney dome-shaped furnaces, charcoal-fuelled flame and steam reverberate across the sides and roofs of the furnaces, dissolving the iron inside.
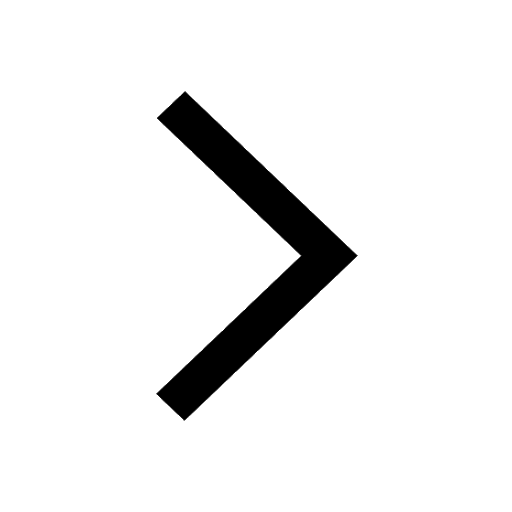
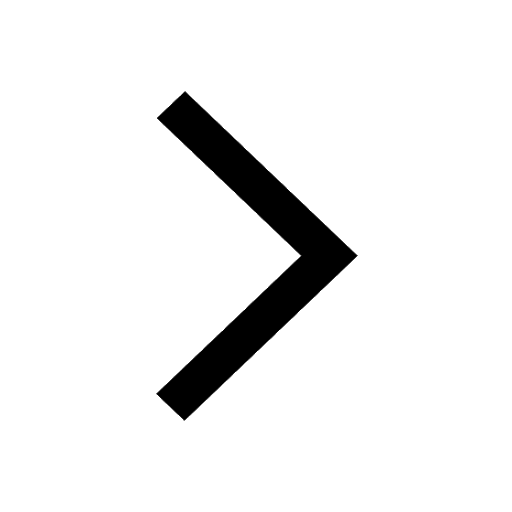
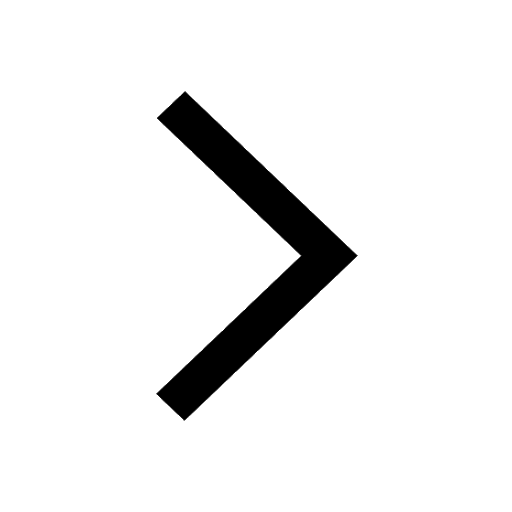
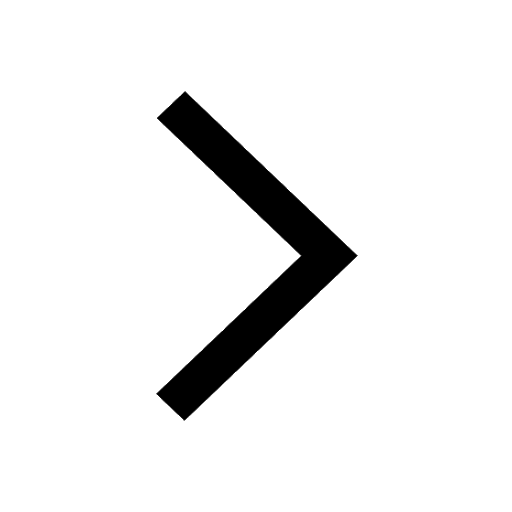
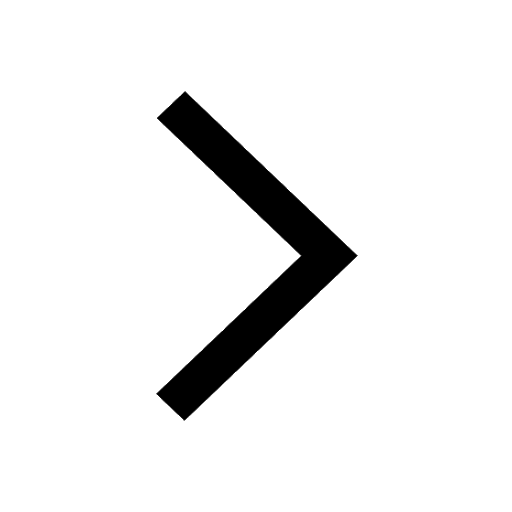
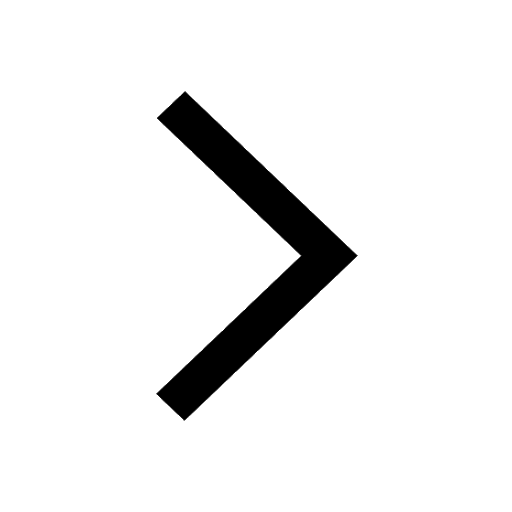
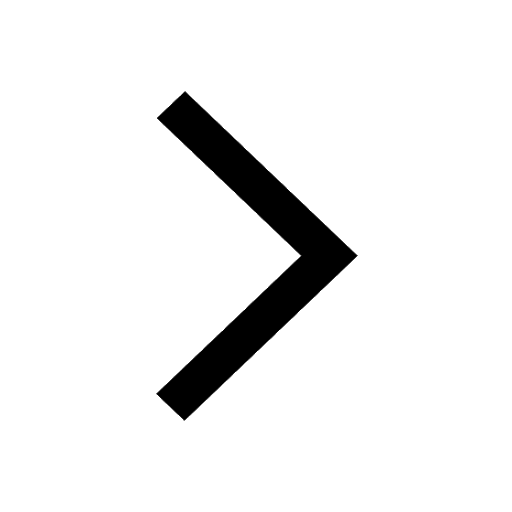
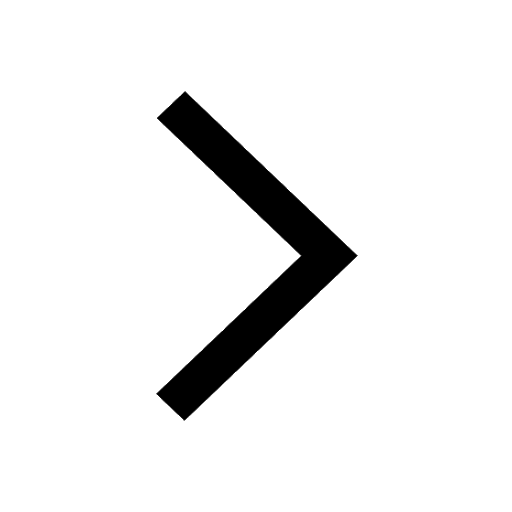
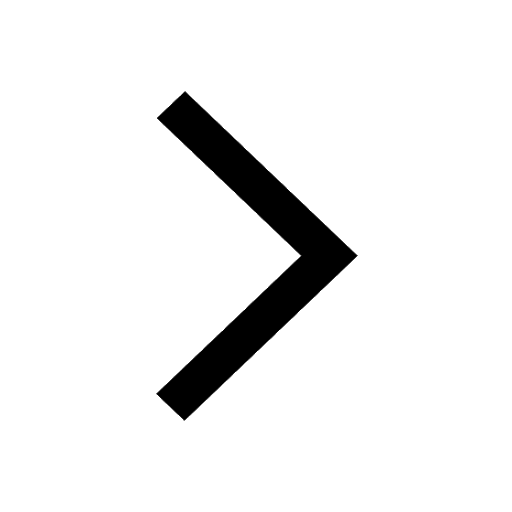
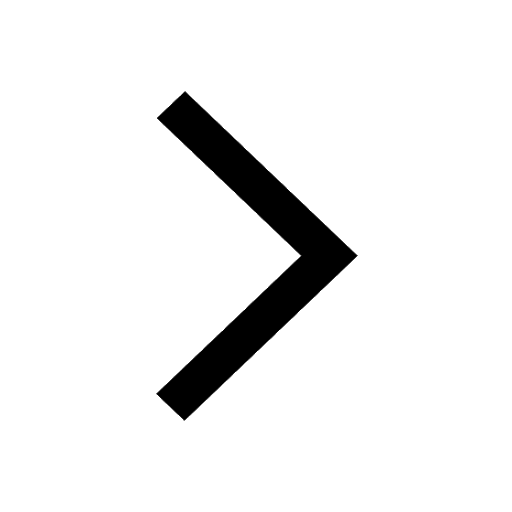
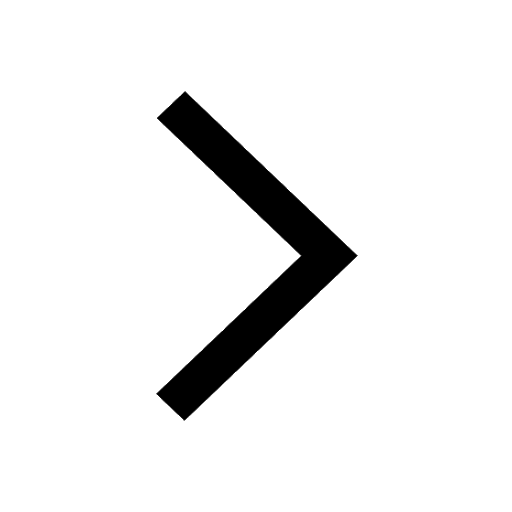
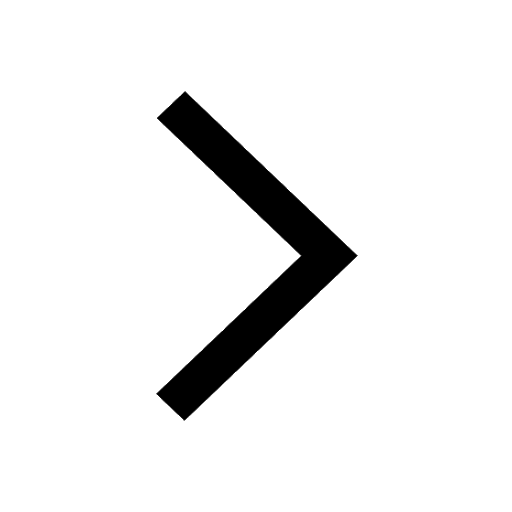
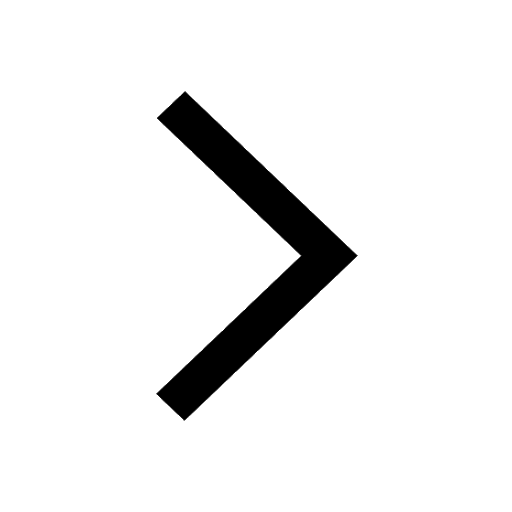
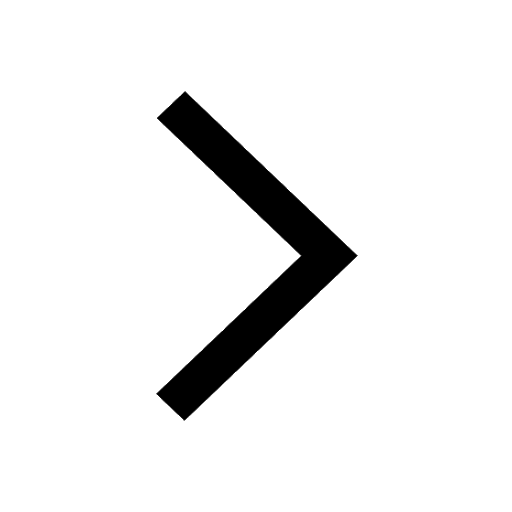
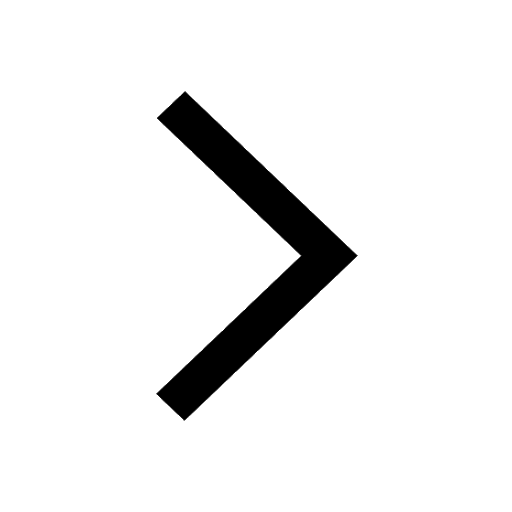
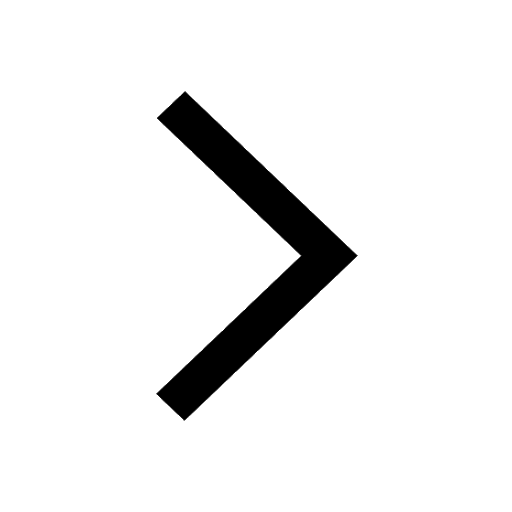
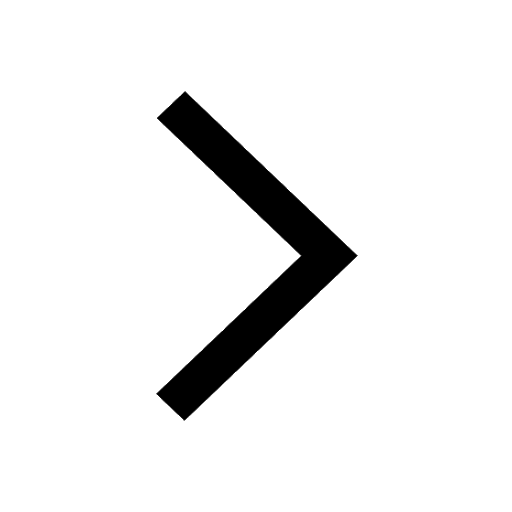
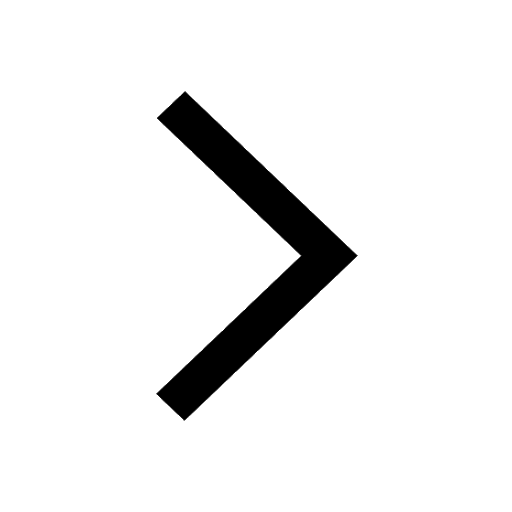
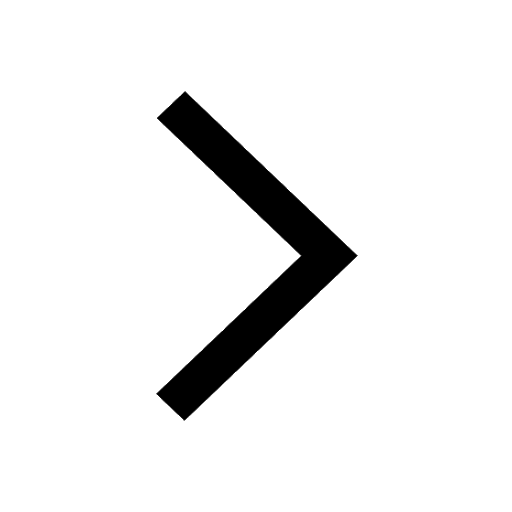
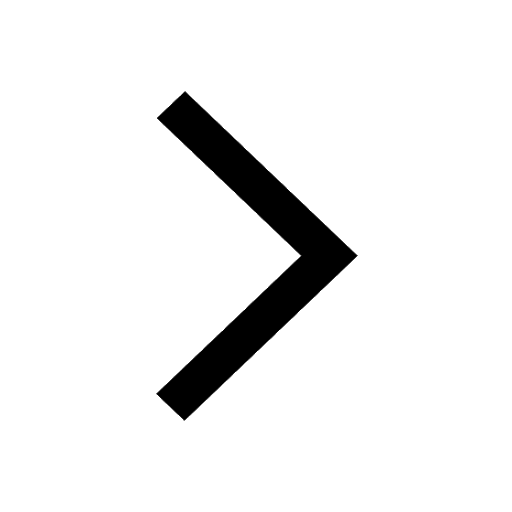
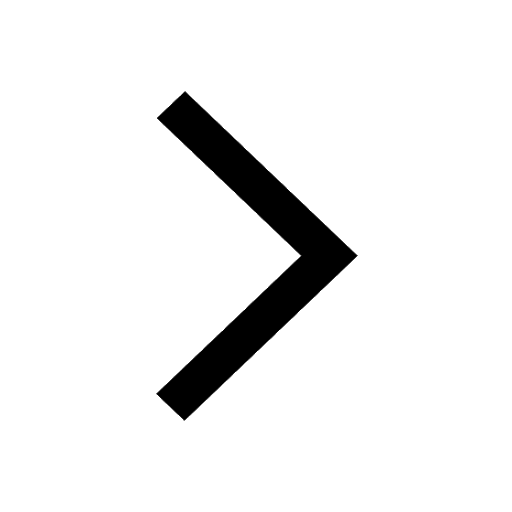
FAQs on Reverberatory Furnace: A Detailed Summary
1. Is roasting done in reverberatory furnaces?
Yes. In a reverberatory furnace, the calcination and roasting operation is completed. For example copper sulphide.
2. What type of roof is utilised to make a reverberatory furnace?
Refractory brick is now utilised for roofs instead of the common brick that was once used, allowing for greater temperatures and quicker refinement.
3. List some advantages and disadvantages of a reverberatory furnace?
Reverberatory furnaces have a number of notable advantages, including inexpensive working, large volume treatment, and maintenance expenses. High metal oxidation speeds, low efficiency, and typically requiring a big space are the downsides on the contrary hand.
Q5. What are Furnaces?
Answer: A furnace is described as a device that becomes really hot enough to reach 1200⁰C or even hotter.