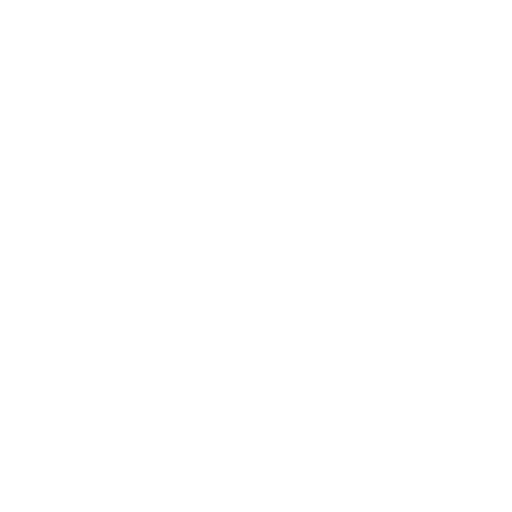

What is Cost Control and Reduction?
Cost control and cost reduction are the two very efficient tools used to reduce the cost of production and maximise profit. In simple words, Cost control is a technique used to provide the management with all the necessary information regarding the actual costs and also align them properly with the budgeted costs. On the other hand, the term cost reduction is used to save the unit cost of the product, without causing any compromise to its quality. The companies use a wide variety of techniques of cost control and cost reduction in order to carry out the process effectively.
(Image will be Uploaded Soon)
Cost Control
The definition of cost control states that it is a process which focuses on trying to control the total cost through competitive analysis. Such practices help in aligning the original cost in agreement with the established costs.
Through this process, firms can ensure their production costs do not soar higher than the predetermined expenses. The cost control process involves several stages, which begins with the budget preparation related to production. Next, the actual performance is evaluated, followed by the calculation variances between the original cost and the budgeted cost. The next task is to investigate the reasons for the same, and the final stage involves implementing necessary actions to mend the discrepancies.
Standard costing and budgetary control are two techniques used in the cost control process. The process is a continuous one and helps to analyse the causes for the variances. It involves:
Determining the standards
Comparing the standards and looking at the results
Analysing the variances
Establishing the action needed to be taken by the firm
Cost Reduction
The definition of cost reduction states it to be a process which aims to reduce the unit cost of a product or service manufactured by the firm without harming its quality. A number of modern and improved techniques can be used for this purpose which serves as an insight to the alternative methods to lower the production costs of every unit.
Cost reduction has a significant role in reducing the per unit costs of products and are thus essential for firms to maximise their profits. This process helps in pointing out and reducing the unnecessary expenses during the production process, storage, selling or distribution of the products. The cost reduction process emphasises the following:
Savings in every unit cost of production
The product quality should not be compromised
Non-volatile nature of the savings
The primary tools involved in cost reduction involve quality operation and research, better designs in products, reducing variety and evaluating jobs amongst others.
(Image will be Uploaded Soon)
Difference Between Cost Control and Cost Reduction
The importance of cost control and cost reduction are massive in businesses, but they have a few differences. The key difference between cost control and reduction include:
Cost control is a process which focuses on reducing the total cost of production. However, cost reduction aims at reducing the per unit cost of a product.
Cost control is a quick process by nature, while cost reduction is a more permanent process.
The cost control process ends when the required target is met. On the other hand, the cost reduction process is a continuous process which does not end after a certain time. It is primarily focused on eliminating unnecessary costs.
Cost control does not provide any promises regarding maintaining the quality of the products, but cost reduction does not affect the quality of the product even slightly.
The cost control process is more of a function to prevent the cost before their occurrence while the cost reduction process is more of a function used to resurrect the expenses.
Thus cost control and reduction are an essential part of any organisation willing to boost their profits.
Did You Know?
The meaning of cost of control is to identify and reduce the expenses in business to maximise profit. It is a useful factor in maintaining and growing the earnings of the company. The budgeting process helps massively in this regard as the actual results of the company are compared with the budget. If the actual costs are more than what planned, then the company needs to take action.
Solved Examples
1. Cost Measure is What Kind of Control?
Corrective
Preventive
Both
None of the above
Ans: (b) Preventive
2. Which Type of Control Process Does Not Affect the Quality of the Products?
Cost control
Cost reduction
Cost-cutting
None of the above
Ans: (b) Cost reduction
Importance of Cost Control and Cost Reduction in Commerce
Cost control mainly focuses on bringing down the total cost of production whereas cost reduction focuses on decreasing the per unit cost of a particular product. Cost Control is thus temporary but Cost Reduction is permanent in nature. In Commerce, students will learn how cost control gets completed once all the business targets are achieved. It is an important chapter that will pave the way for other related chapters later on. Getting the very fundamentals right at this stage will then assist the students in understanding all the challenging concepts later on. It is one of the most important chapters of Commerce and must be prepared for in a proper manner.
How to Prepare for a Commerce Test on Cost Control and Cost Reduction
Students can go through Cost Control and Cost Reduction – Explanation, Difference and Solved Examples on Vedantu
This page has all the information that they need to be aware of
Read everything on the page and then make notes on certain topics using your own words
Go through the solved examples properly
Assess what you’ve learnt by writing each of the concepts down in your own words
Revise from this page before all tests
FAQs on Cost Control and Reduction Strategies
1. How do students revise Cost Control before their commerce exams?
Students can revise Cost Control from Cost Control and Cost Reduction – Explanation, Difference and Solved Examples on Vedantu. They can read up this page and get to know why it's important. Cost Control is a tactic that’s employed by companies to control the total cost through competitive analysis. The material provided here is pertinent and in keeping with the Commerce syllabus and so the students can be rest assured that they are on the right track when it comes to this topic.
2. Is Cost Control the same as Cost Reduction in Commerce?
Both are similar but not the same things. Cost Control is used to align the actual costs with the budgeted costs whereas Cost Reduction is used to preserve the unit cost of a product without compromising on its quality.
The distinction between both becomes clearer as students refer to Cost Control and Cost Reduction – Explanation, Difference and Solved Examples on Vedantu’s e-learning platform. Both have been explained rationally and in a lucid language. Going through the page will assist the students in learning the differences between both.
3. Is it important for students to go through the topic of Cost Control and Cost Reduction in Commerce?
Yes, it's vital for students to go through Cost Control and Cost Reduction as these concepts of Commerce are very important. These are the basics that one needs to know so as to know the other concepts. Without a grasp over these, they will not be able to understand anything else that’s in their Commerce syllabus. They can also read from Cost Control and Cost Reduction – Explanation, Difference and Solved Examples on Vedantu as this page has explained both the concepts in a very interesting manner. The students can go through the matter and will then not feel like skipping anything.
4. Where can students learn about Cost Reduction online?
Students can learn about the same online if they refer to Vedantu. Vedantu is India’s trustworthy online tutoring portal that provides free of cost study material to millions of potential students all over the world. The material can be downloaded and accessed later on as well when students do not have access to the internet. All they need to do is log in with their credentials. Vedantu has Cost Control and Cost Reduction – Explanation, Difference and Solved Examples on its platform so that students of Commerce get to know in depth about Cost Reduction.
5. What are the areas related to the process of Cost Reduction?
To define cost reduction, one refers to reducing the unit cost of a product or service without harming its quality. The areas of cost reduction process include:
The most important area of the cost reduction process is the design of the products that are being produced. The easiest way of reducing costs is by making the product simpler and making it more standard. When such a design of the production gets the nod of approval, the production process undergoes certain arrangements. Thus reduce costs meaning that firms have limited choices available to them.
The organisation of the factory layouts where the products are being made and the methods are undertaken.
Marketing is another area where the costs of selling, distribution, distribution channels or transportation can be reduced.
6. What is Cost-cutting?
The cost-cutting definition refers to the processes implemented by various firms to cut their expenses and boost their profit margins. Such steps are taken by companies when they face an economic downturn or during periods of the financial crisis.
It is important for the company to have a cost-cutting strategy in place to carry out the process effectively. Most classify the costs into good, bad and best costs and the aim is to maximise the best costs and eliminate bad costs. This is a process which is more concerned with optimising the costs rather than cutting them off altogether.
However, they have their fair share of risks as overcutting costs could lead to an increase in demand at a position, thus incurring more costs.
7. How will students know about the type of questions that come from Cost Reduction in their Commerce exams?
Students can read from Cost Control and Cost Reduction – Explanation, Difference and Solved Examples and then get an idea about the kinds of questions that will be asked in theri Commerce exams. They can read this page thoroughly and then understand how each is different and how each is implemented in the businesses that run. If they are well-versed with the content that’s on the page, they will be able to answer every question that comes and secure higher marks in their examinations.
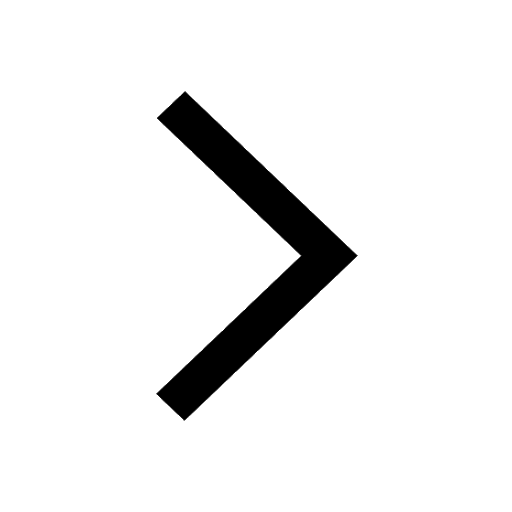
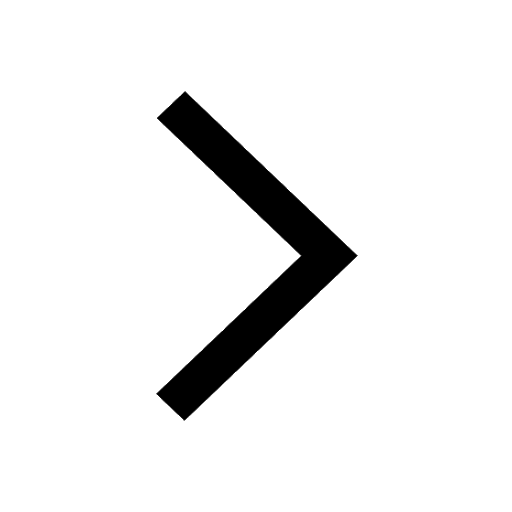
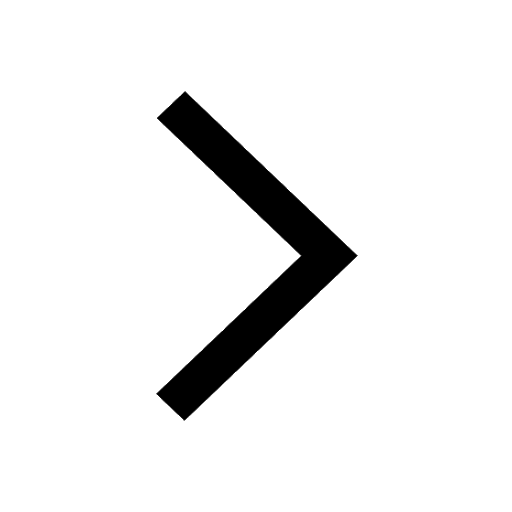
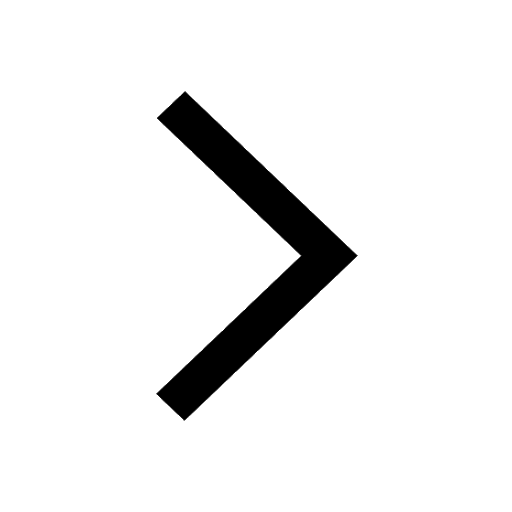
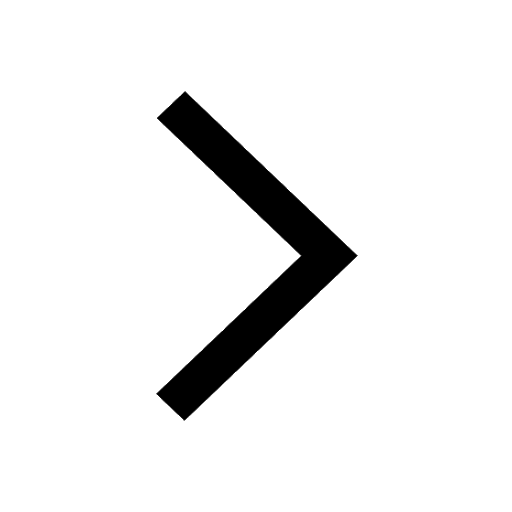
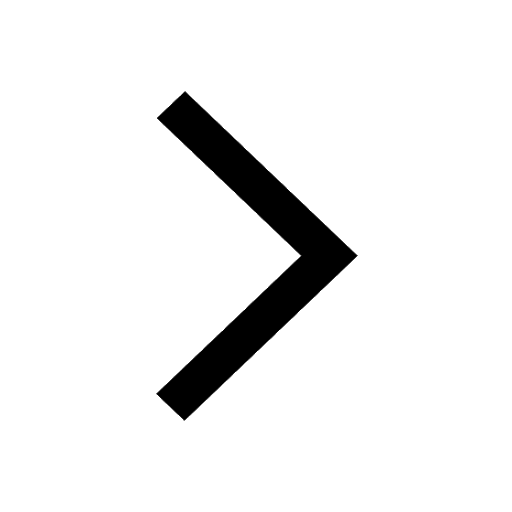