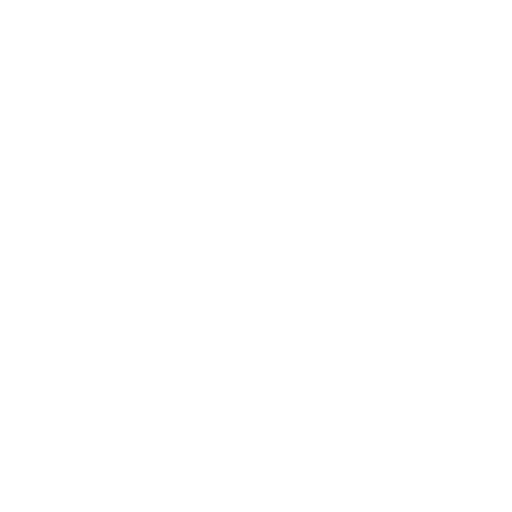

What is a Corrosion Inhibitor?
Corrosion destroys various metals such as iron, steel, and copper. Various techniques and substances are used to inhibit or prevent the process of corrosion. One of the processes or techniques is Corrosion inhibitors to prevent or reduce the rate of corrosion.
Chromate, molybdate, and nitrate are the most commonly used corrosion inhibitors. Corrosion inhibitor spray is also used to inhibit the rusting process.
WD-40 is one corrosion inhibitor spray. There are various manufacturers of corrosion inhibitors.
What is Corrosion?
Corrosion is the process of destruction of a material as a result of its interaction with its surroundings.
Examples of Corrosion
Formation of rust on the iron surface which is also an electrochemical process
The blue-green coating on the surface of copper metal
Tarnishing of silver
What are Corrosion Inhibitors?
Corrosion inhibitors are chemical substances that when added to the environment reduce the rate of corrosion and are hence used to protect the substance from corrosion.
Chemicals that are used to prevent and slow down the process of corrosion are generally liquid or gases.
Corrosion Inhibitors for Water - when corrosion inhibitors are mixed with water, their effect may depend on the quality or properties of water such as viscosity, temperature, etc.
Types of Corrosion Inhibitors
Corrosion inhibitors are generally of three types depending on the type of method used by them.
Anodic Inhibitor - In this type of corrosion inhibitor. It helps in the formation of a protective oxide layer on a metal surface. This reaction causes a considerable anodic move transforming the metallic exterior into a passivation area. This passivation helps in decreasing the corrosion of the metal. Examples of anodic corrosion inhibitors - Chromates, nitrates, and molybdates can be used as anodic inhibitors.
Cathodic Inhibitor - This type of inhibitor is used for decreasing the cathodic reaction. They also work to hasten the cathodic metal region to confine the dispersion to the metal surface of the eroded metal. Examples of cathodic corrosion inhibitors -
Sulfite and bisulfite can be used as cathodic inhibitors Which react with the oxygen to make sulfates.
Redox reaction catalysts by nickel are also another example of a cathodic reaction.
Mixed Inhibitors - Mixed corrosion inhibitors also form a thin protective layer on the surface of the metal. They worked to lessen the process of anodic as well as cathodic reactions. This is done through the formation of a precipitate on the surface of a metal.
Silicates and phosphates can be used as mixed inhibitors. These chemicals react with water to stop the process of corrosion and are also used as water softeners to stop the rusting of water.
Examples of mixed corrosion inhibitors - are silicates and phosphates.
Mechanisms of Corrosion Inhibitors
Cathodic Toxic Substances: These are utilized by smothering the procedures of cathodic decrease to adjust the reaction at the anode. The vulnerability of the metal to hydrogen-initiated breaking can be inclined to cathodic inhibition because the metal can retain hydrogen during cathodic charging or aqueous corrosion. In low-pH solutions, some decreased hydrogen diffuses as atomic hydrogen into the metal as opposed to the gas formation. This occurs during electroplating or pickling of the metal.
Oxygen Scavengers: These are synthetic chemicals that react with dissolved oxygen for a reduction in corrosion. The best examples are Sulfite and bi-sulfite ions that lead to the formation of sulfates while reacting with oxygen. Before any bringing down of oxygen dissolved in mud is finished by a scavenger, the air is expelled from the mud through mechanical foaming and degassing.
Cathodic Precipitates: These incorporate zinc, calcium and magnesium. They are accelerated on the metal surface to shape into a defensive layer. Since the task of an inhibitor is to diminish the anodic procedure rate, the possible corrosion change after an inhibitor has been included demonstrates a hindrance in the procedure. Positive displacement of the corrosion potential demonstrates an obstacle of the anodic method. The negative displacement of the potential shows the impediment of the cathodic process.
Inhibitors
An inhibitor is a chemical compound or mixture of chemicals that, when given at extremely low concentrations to a corrosive environment, effectively prevents or lowers corrosion while causing no substantial interaction with the environment's components. Inhibitors are useful in closed environmental systems with excellent circulation because they ensure an appropriate and regulated concentration of inhibitors. These conditions can be reached in a variety of applications, including cooling water recirculation systems, oil refining, oil production and acid pickling of steel components. Antifreeze for vehicle radiators is one of the most well-known applications for inhibitors. Inhibitors can be organic or inorganic chemicals, and they are often dissolved in aqueous solutions. They reduce corrosion by acting as a barrier, by forming an adsorbed layer or by delaying the anodic, cathodic, or both corrosion processes.
Factors to Consider While Selecting an Inhibitor
Cost of the inhibitor.
The toxicity of the inhibitor can cause ill effects on human beings and other living spices.
The availability of the inhibitor determines its selection.
Inhibitors should be environment friendly.
Corrosion Classification
Corrosion has been divided into the following methods:
Low-temperature corrosion and high-temperature corrosion (or)
Electrochemical corrosion and chemical corrosion (or)
Wet and Dry corrosion.
Wet corrosion happens when a metal comes into touch with an electrolytic conducting liquid or when two different metals or alloys are submerged or partially immersed in the electrolytic conducting solutions. This is always connected with low temperatures. Dry corrosion occurs mostly as a result of the direct chemical action of air gasses and vapours in the environment. This is usually linked with a high temperature.
Effective Method of Using Corrosion Inhibitor
One of the most effective ways to fight corrosion is to utilize corrosion inhibitors. Three elements must be addressed for them to be used effectively:
Identification of corrosion problems
Anodic inhibition (polarization of the anode to be increased)
Cathodic inhibition (polarisation of the cathode to be increased)
Resistance inhibition (increase in circuit's electrical resistance simultaneously with creating a thin or thick layer on the metal's surface)
Diffusion restriction (preventing the diffusion of depolarizers)
Conclusion
Corrosion inhibitors are chemicals used to inhibit or slow down the process of corrosion.
There are three main types of corrosion inhibitors- anodic, cathodic, and mixed. Corrosion inhibitors are used to decrease the process of rusting. Corrosion inhibitor chemicals are synthesized by various methods. These are also available in spray form.
FAQs on Corrosion Inhibitor
1. What are the adverse economic and social effects of Corrosion?
Corrosion has a far greater impact on the safe, dependable, and efficient functioning of equipment and buildings than just losing a mass of metal. Even though the amount of metal damaged is minimal, failures of various machines and the need for costly replacements are possible. The following are some of the most serious negative consequences of corrosion:
Nuclear power plants are shut down owing to failures, such as a nuclear reactor failing during the decontamination process.
Replacement of rusted equipment costs a lot of money.
Painting is an example of high-cost preventative maintenance.
Product loss as a result of a rusted container.
Loss of Efficiency.
A fire hazard, an explosion, or the release of a poisonous product are all examples of safety requirements.
Corrosion is likely to be the cause of health issues, such as lead pollution in drinking water.
2. What are the methods to control Corrosion?
Corrosion is a harmful and silent process. It causes issues for both large and small businesses. Since corrosion is unavoidable, it can be reduced rather than prevented by using particular anti-corrosion techniques. There are a variety of effective approaches for protecting metal from corrosion. They might be based on a broad range of factors:
Modification of metal
Modification of design
Modification of the corrosive environment
Modification of metal environment potential
Use of inhibitors
Modification of surface
These methods are often used independently or together. Instead of employing numerous strategies to avoid or prevent deterioration or degradation of metal surfaces, corrosion inhibitors are one of the most well-known methods of corrosion prevention. Because of the low cost and ease of administration, the usage of inhibitors is on the rise.
3. Can I get Chemistry Study material for the chapter “Corrosion Inhibitor.”
Students may be confident that at Vedantu, they will be able to properly comprehend the chapter with the assistance of subject matter experts and the content supplied by them. The answer offered is simple to grasp and clearly described, and students may rely on it for test preparation. These solutions are available for free on Vedantu's website and may also be downloaded via Vedantu's app. Vedantu's professors framed the solutions from an examination standpoint. These solutions are written entirely with accompanying illustrations and examples so that students can remember them for a long time. Students can also access Vedantu's online learning services via a smartphone app, which can be downloaded for free. Because books and computers cannot be brought everywhere, Vedantu's mobile app was developed to offer students with the assistance and comfort they require when studying. The mobile software may be downloaded at any moment, allowing students to study or review whenever they have free time.
4. What do you Mean by the Term Anti-corrosive Agents?
Anti-corrosion intends to shield the metal's surface from eroding at high-risk environmental conditions. Zet-Chemie has various agents to ensure your metal against erosion. These corrosion agents help to protect a wide range of metals against rust and corrosion.
In the most widely used word, the term anti-corrosive agents imply electrochemical oxidation of metal in response to an oxidant, for example, oxygen. Rusting, the arrangement of iron oxides is a notable case of electrochemical corrosion. This kind of damage commonly creates oxide(s) or salt(s) of the original metal.
There are various strategies for the prevention of corrosion, particularly in marine applications. Anti-corrosion measures are of specific significance in situations where high moistness, fog, and salt are factors.
5. How to Protect the Corrosion?
The following ways can prevent corrosion:
1. By Interfacing Metal to a Progressively Electropositive Metal: As long as the more electropositive metal is there, the given metal doesn't get eroded. For instance, iron can be shielded from corrosion by interfacing it with a block/plate of zinc or magnesium. This technique for the protection of corrosion is called protection or cathodic.
2. By Coating Insoluble Phosphate or Chromate: Metal surfaces are treated with phosphoric acid to formulate an insoluble phosphate. The corrosion of metals can also be prevented by the formation of a thin chromate layer.
3. Using Anti-Rust Solutions: Solutions of alkaline phosphatase and alkaline chromates are commonly utilized as anti-rust solutions.
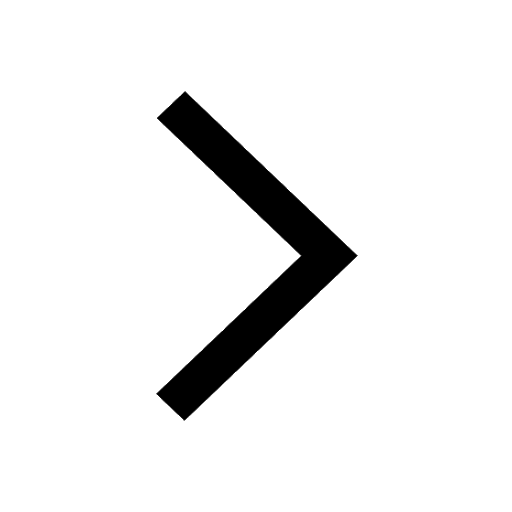
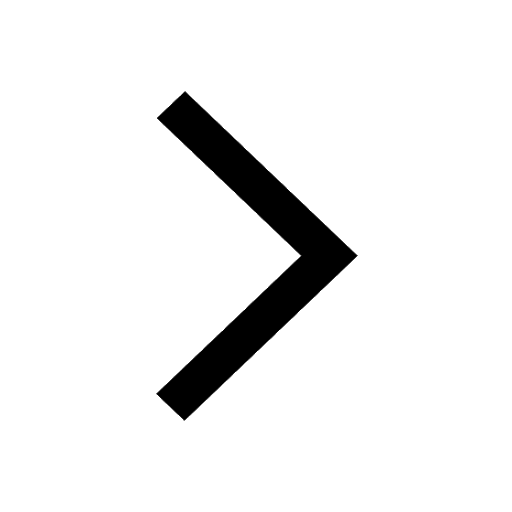
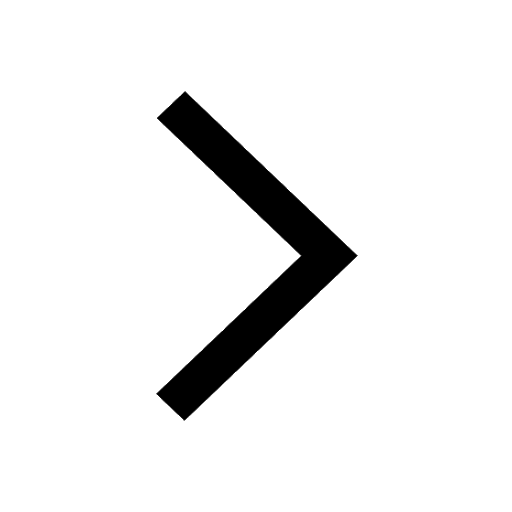
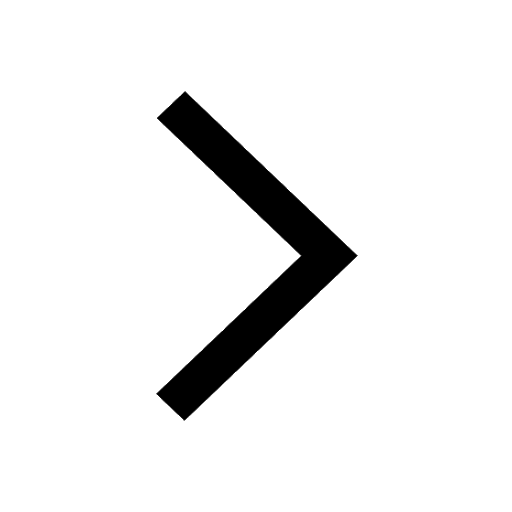
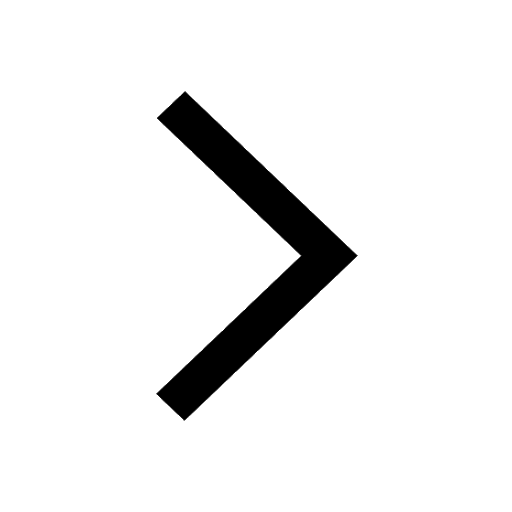
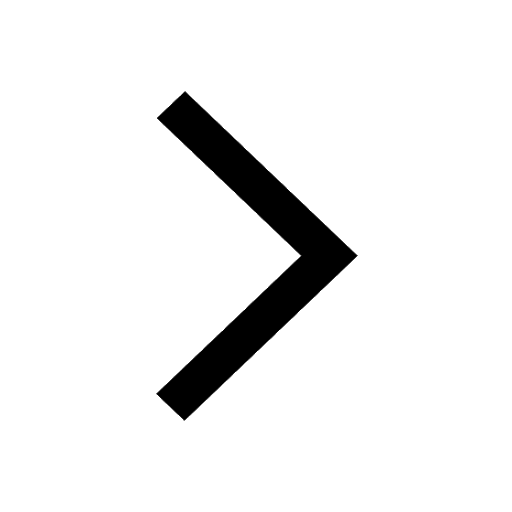