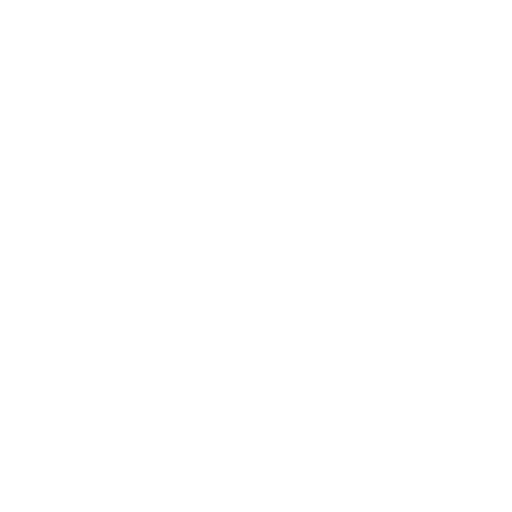

Screw Gauge Measurement Using the Micrometer
A differential screw is a key component in an analog screw gauge for measuring small magnitudes. There are a number of threads on these screws, and each thread, when turned individually, causes them to move axially. As a result, it covers a minute distance axially with every 360° turn of the screw. In other words, a screw's pitch or lead. By rotating the thimble and the screw, we can measure the size of the object to be measured, even if the object is very small. Having a minute dimension means that rotations are more easily readable as they are bigger. On an LCD screen, the measurement of an object is displayed using a digital screw gauge.
Screw Gauge Measurement Using the Micrometer
Screw Gauge is a mechanical tool that facilitates measuring the diameter or radius or thickness of a thin wire or thickness of a thin metal sheet with utmost accuracy. Figure1 shows the schematic of the Screw Gauge. This tool consists mainly of a U shaped frame and a spindle (or screw) attached to the thimble. There are two scales known as Pitch Scale which is the main scale and is engraved on the barrel with vertical lines. Another one is the Circular Scale which is engraved horizontally on the thimble. Pitch scale measures the distance in millimetre (mm) travelled by the spindle per revolution. One revolution by the circular scale is equal to half of the millimetre of displacement of the screw is called a micrometre screw gauge. Micrometre gauges are more accurate and precise as compared to the Vernier Caliper scale.
Schematic of the Screw Gauge Showing Different Parts of it.
Before starting measurement, it is indispensable to make sure that the ‘Stud-end’ and the ‘Spindle (or Screw) end’ area is cleaned; otherwise, the obtained measurements will provide the wrong thickness.
The plane surface near Stud is stationary and is also known as ‘Anvil’ which is immovable and attached with the U-shaped frame. When the anvil and spindle (or screw) is in contact, the zero of the Pitch Scale (or main scale zero) must coincide with zero of the circular scale. This is considered as the reference of the measurement.
As the anvil is fixed, therefore, it is appropriate to place the object, whose thickness is to be measured, firmly near the anvil. At the same time, the cylindrical thimble at the other end of the gauge needs to be rotated clockwise. This act will make the spindle (or screw) part move forward in a linear direction towards the anvil. Keep rotating the thimble such that the spindle (or screw) reaches the object, which was placed near the anvil.
In this final condition, an object, whose dimension is to be found, must be held tightly and stable between the anvil and spindle. Ratchet is used which clicks three times once the precise movement of the spindle is done. This position can be locked using the lock knob positioned near the spindle.
Once the previous step is obtained, both the pitch scale and the circular scale should be readout. Pitch scale reading is the value of the Pitch scale when it touches the sleeve of the circular scale. The circular scale reading is the reading which matches the line on the pitch scale. A magnifying glass can be used to read the measurements. Let’s say the pitch reading is ‘X’ and the circular reading is ‘Y’.
The final calculation will be as follows:
Total reading = X(mm) + (Y x LC of the gauge)mm
Here, LC is the least count of the gauge.
Screw Gauge Measurement Through the Inch Micrometer
The basic design of the Screw gauge in an Inch micrometre is similar to the one discussed in the previous section. The only difference is the dimension of the scale with which the circular and pitch scale deals.
The number of divisions on the pitch scale is calculated in terms of the part of an inch. Figure 2 shows the Pitch scale of an inch micrometer. The number 5 (or the graduation 5) on the barrel denotes half of the inch or 0.500 inches. There are 4 divisions between graduation 0 and graduation 1 on the pitch scale. So, the first graduation seen on the barrel like a number 1 is a 10th of an inch or 0.100 inches or 100th of a 1000 inch. Similarly, the graduation 2 is 0.200 inches or 200th of 1000 inches or 20th of 200 inches. Hence the smallest division on the pitch scale would be 0.025 inches or 25th of 1000 inches.
Pitch scale of the Inch Micrometer
Next is to learn how to read the circular (or thimble) scale of an inch micrometre. The circular scale is shown in Figure 3, consisting of 25 divisions altogether.
Circular or Thimble scale of an Inch Micrometer
The smallest division on the circular of the thimble scale is the 1000th part of an inch; hence it is equal to 0.001 inches. Similarly, the 5th reading is equal to 0.005 inches.
Next, we discuss an example of how to read the total reading from an inch micrometer. Consider figure 4, the main scale or pitch scale will be 0.375 inches as there are 13 divisions and one division equals 0.025 inches as calculated before. While on the circular scale it is 0.001 inches. Hence the total reading is 0.375+0.001 which is 0.376 inches.
Inch Micrometre with Pitch and Thimble Scale
Screw Gauge Formula
Pitch scale measures the distance in millimetre (mm) travelled by the spindle per revolution. The pitch of the screw gauge is calculated as given below:
To measure the dimension of a thin wire or thin sheet using a screw gauge, one needs to know the least count. The least count of the screw gauge can be calculated using the formula given below:
Once the least count of the gauge is calculated, the final reading is calculated as below
Total Reading = Pitch Scale Reading + Circular Scale Reading x LC of the gauge.
LC in the above equation is the least count of the gauge. There might be the possibility that the zero of the pitch scale does not coincide with the zero of the circular scale. In that case, either the scale can be above or below the pitch scale (also known as the main scale). Figure 5 discusses all the possible causes.
Figure 5: Case 1, shows the nil zero as the pitch scale zero matches the circular scale zero. Case 2 is the positive zero as circular scale zero is below the pitch scale zero. Case 3 is negative zero error as the circular scale zero lies above the pitch scale zero.
If the zero of the circular scale is below the pitch scale zero, it is known as positive zero error. The number of divisions on the circular below the pitch scale is to be multiplied with the least count of the gauge. This value is to be subtracted from the total reading for the correct measurements. Hence the formula becomes as follows:
Total Reading = Pitch Scale Reading + Circular Scale Reading x LC of the gauge - positive zero error reading x LC of the gauge
If the zero of the circular scale is above the pitch scale zero, it is known as negative zero error. The number of divisions on the circular above the pitch scale is to be multiplied with the least count of the gauge. This value is to be added to the total reading for the correct measurements. Hence the formula becomes as follows:
Total Reading = Pitch Scale Reading + Circular Scale Reading x LC of the gauge + negative zero error reading x LC of the gauge
An example is discussed on how to read the screw gauge measurement using a micrometre. Figure 6 is the final reading to be calculated.
Screw Gauge Using Micrometer
The micrometre shown in Figure 4 has a pitch of 0.5 mm. It means that for one complete rotation of the thimble scale, 0.5 mm distance is travelled by the spindle. There are 50 divisions on a circular scale. The least count will be 0.01 mm calculated as below.
Least count=PitchNumber of divisions=0.5*50=0.01mm
The pitch scale reading in Figure 4 is 3 mm. For the circular scale reading, the 46th division matches with the reference line on the pitch scale. Hence total reading will be
Total Reading = Pitch Scale Reading + Circular Scale Reading x LC of the gauge
= 3mm + 46 × 0.01 mm = 3.46 mm.
A Positive Zero Error is:
The zero error is said to be positive if, when the dial and spindle of a micrometre screw gauge are brought together, the circular scale's zero mark is below the central scale line.
The division on the circular scale that corresponds with the main scale line can be used to determine positive zero error. Optical errors are calculated by multiplying the number of divisions on the main scale line by the lowest count of the micrometre screw gauge. It is necessary to deduct this error from the overall reading to get the correct result.
When the zero mark of the circular scale is above the scale line on the anvil and spindle of a micrometre screw gauge, then it is said that the zero error is negative.
In the circular scale (C.S.R. ), negative zero errors can be found by looking at the division on the main scale line. The negative error, therefore, equals the product between the number of divisions of a circular scale based upon the main scale line and the smallest count of the micrometre screw gauge. This error must be added to the overall reading to obtain the correct result.
Back-lash Error:
Because of the wear and tear of threads, sometimes the tip of the screw does not rotate fully backward during the reverse rotation of the head. Such a phenomenon is known as back-lash. When an object is held between anvil and spindle, don't rotate the head in the reverse direction. This will avoid backlash.
The Use of Screw Gauge:
Apply gentle pressure between the anvil and spindle of the screw gauge while holding the object that needs to be measured.
Take a note of the initial reading of the circular scale just before zero. It is called the main scale reading (M.S.R.).
The number of circular scale divisions (n) that coincide with the main scale line should be noted down. Reading circular scale, (C.S.R.) - n X least count.
To get readings, combine the MSR and the CSR.
To get the correct reading, subtract the zero error from the above reading.
Types of Errors in Screw Gauge
Basically, there can be three types of errors that come in screw gauge : zero error, positive error, and negative error.
If the zero marks in the main scale and in the thimble scale don’t coincide when the anvil and the spindle touch each other, it is zero error. Zero error is always subtracted from the total reading.
In positive zero error when the anvil and the spindle touch each other, the thimble scale zero-mark advances beyond the main scale zero mark.
In negative zero error when the anvil and the spindle touch each other the thimble scale zero mark is left behind the main scale zero mark.
For example : consider a wire of diameter nearly 0.1 cm, if measured from a screw gauge having negative zero error and Z. C=+0. 0005 mm, can be found out to be zero.
Solved Examples
Consider a screw gauge whose least count of 0.01 mm. On rotation we found that main scale reading is 2 mm and circular scale reading is 40. Determine its total reading.
Sol: Given:
Least count of the screw gauge= LC= 0.01 mm
Main scale reading=MSR= 2 mm
Circular scale reading= 40
We are asked to determine the total reading value. We know that, total reading of a screw gauge is given by:
Total reading = Main scale reading + (Circular scale reading × Least count of the gauge)
In a screw gauge there are 50 divisions on the thimble scale and screw advances 1 mm in a one complete rotation of the screw cap. In another screw gauge there are 100 divisions on the thimble scale and screw advances 1 mm in a one complete rotation of the screw cap. Which of the two scregauge is providing accurate measurement?
Sol: Let us first calculate the LC of both the screw gauge by the formula:
The LC of first screw gauge be
The LC of second screw gauge be
We know that, The screw gauge which has the smallest least count is capable of measuring a very smaller length than that of the least count screw gauge. So the second one is more accurate than the first one.
Thus,
Summary
In a micrometre screw gauge, there are 2 gauge readings taken, the first is the main scale reading followed by the circular scale reading. The instrument has 2 adjustment keys, one is for moving the spindle towards the anvil. The other key is a lock when the gauge is achieved. They additionally involve some extent of error. These errors come because of improper usage or wear and tear. Whereas analysing the error and correcting it, we can have near perfect results.
FAQs on Screw Gauge
1.Does the micrometre screw gauge have an accurate reading?
Using a micrometre screw gauge is recommended if a more accurate measurement is required. It can measure objects up to a few millimetres across and is typically accurate to 0.01 mm.
2.What is the purpose of a micrometre screw gauge?
Measurements can be taken using the micrometre screw gauge even more accurately than with the Vernier callipers. An auxiliary scale (measuring tenths of a millimetre) on a rotary thimble is also used on the micrometre screw gauge.
3.Why is the micrometre screw gauge equipped with a ratchet?
In a nutshell, the ratchet provides a kind of limiting device by applying a force by sliding at a predetermined torque. This prevents the spindle from moving further. In addition to scales being locked in place, some screw gauges also contain locking devices that prevent any kind of error during the reading process.
4.What types of screw gauges are there?
Universal micrometre sets - They include a variety of interchangeable anvils, such as disks, blades, points, and knife edges. Universal micrometres can be used as external microphones, depth microphones, step microphones, etc.
Blade micrometres - It has two narrow blade-like tips designed to measure narrow objects, such as O-ring grooves.
Pitch-diameter micrometres - Using these, you can measure screw thread pitch diameter with thread-shaped tips.
Limit micrometres - A measurement object should pass through the first gap and halt at the second gap, which consists of two anvils and two spindles.
Bore micrometres - Designed to measure the inside diameter of an object. They have three anvils.
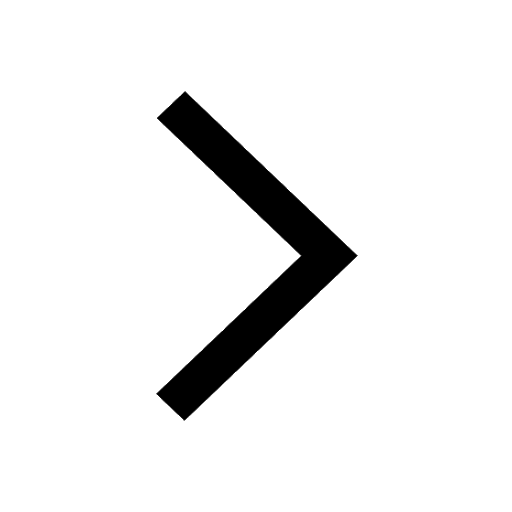
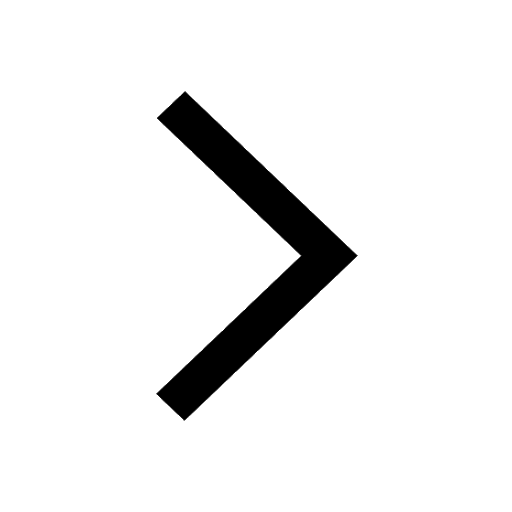
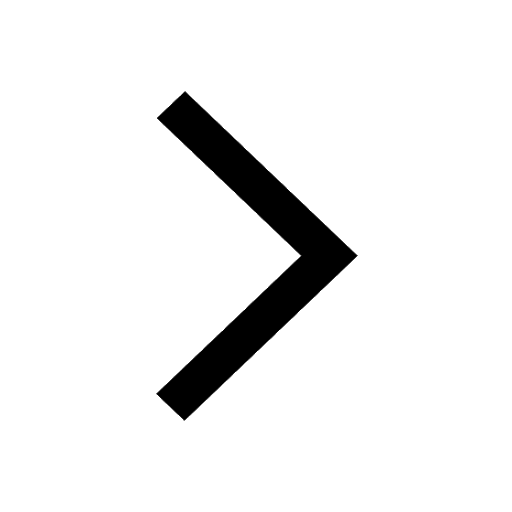
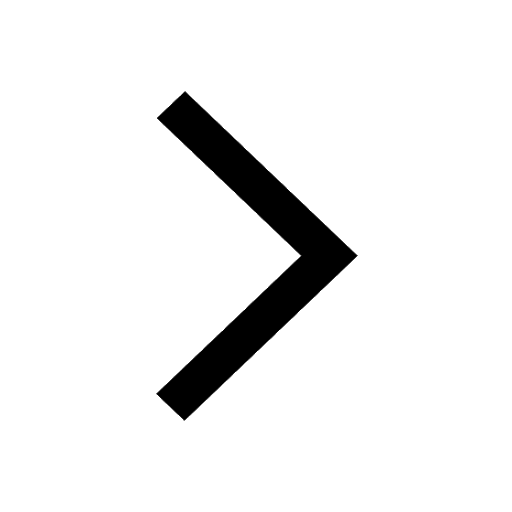
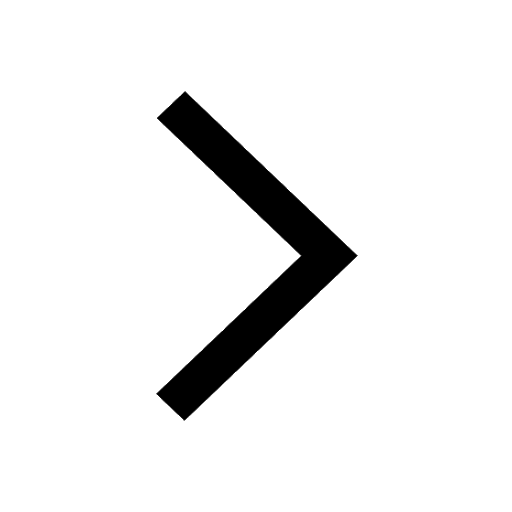
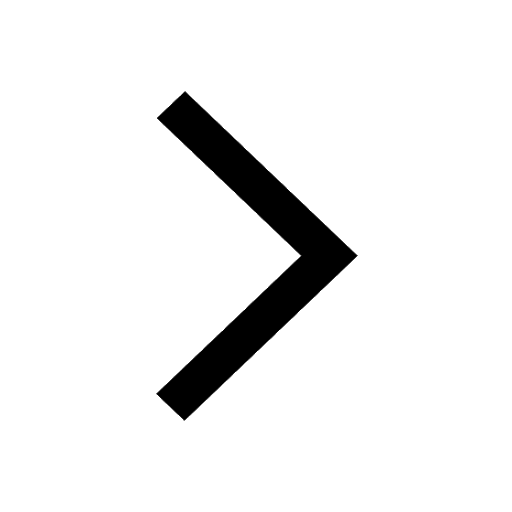