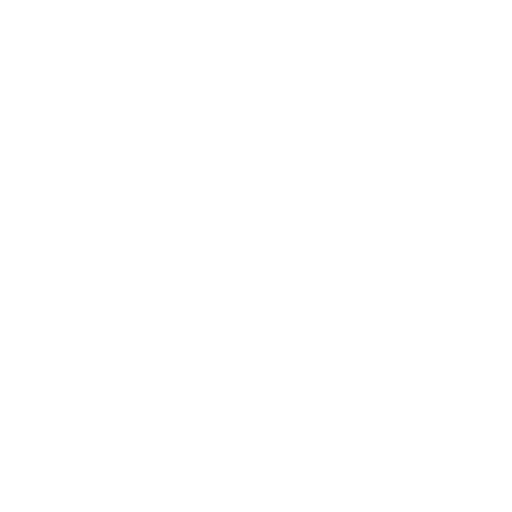

Screw Gauge to Measure Thickness of a Sheet
A screw gauge is a tool for precisely measuring the diameter of a thin wire or the thickness of a metal sheet. You can usually measure length precisely up to 0.1 mm with Vernier Calipers. A screw gauge can be used to make more precise length measurements of up to 0.01 mm or 0.005 mm.
As a result, a Screw Gauge is a more precise instrument than Vernier Calipers. A screw has threads on it. Any two successive threads are separated by the same amount of space. By twisting the screw anticlockwise or clockwise in its nut, it can be moved backwards or forward.
We all know that Vernier calipers are one of the precision instruments that can actually measure with an accuracy of up to 0.1 mm. At the same time, higher accuracy can be attained using Screw Gauge. A Screw Gauge can take measurements up to 0.01 mm to even 0.005 mm. The sole idea behind this experiment is to find how to measure the thickness of a sheet of paper using a screw gauge.
Aim of the Practical
The aim of the experiment is to measure the thickness of a given sheet using a screw gauge.
What is the Apparatus Requirement in the Experiment?
Screw gauge
Sheet
Magnifying Lens
Apparatus Description
A screw gauge is made up of a U-shaped frame with a screwed spindle connected to a thimble. A scale graduated in mm is carved parallel to the thimble's axis. Pitch scale is the term for this. A sleeve is affixed to the screw's head.
A ratchet on the screw head prevents the screw from being overtightened. A circular scale known as the head scale is found on the thimble and is divided into 50 or 100 equal sections. The sleeve moves around the pitch scale when the screw is turned.
The anvil is a stud with a plane end surface that is positioned precisely opposite the screw tip on the 'U' frame. When the screw's tip makes contact with the anvil, the head scale's zero normally corresponds with the pitch scale's zero.
Theory
Screw gauge is one of the precision instruments that can be used to accurately measure the thickness of a paper, or even the diameter of a thin wire. The structure of a screw gauge consists of a U-shaped frame along with a screw spindle that is attached to the thimble. In a screw gauge, mm scales are engraved, running parallel to that of the thimble.
(Image will be uploaded soon)
The head section of the screw gauge consists of a ratchet that restricts the over-tightening of the screw. Within the thimble section, it consists of a circular scale that is divided into 50 or 100 equal parts. It is also termed as a head screw, which moves over the pitch scale while operating.
The anvil, which is the stud with a plane end surface, forms the U shaped frame. It can be found on the opposite side to the tip of the screw. You will find the zero of the head scale coinciding with that of the pitch scale. This occurs when the tip of the screw comes in contact with that of an anvil.
Pitch of the Screw Gauge
The pitch of the screw gauge can be defined as the distance traveled by the spindle per rotation. The pitch of the screw gauge can be determined by the distances traveled by the screw, divided by the total number of rotations.
The formula for pitch is given by:
Pitch of the Screw = \[\frac{\text{(Distance travelled by the screw)}}{\text{(Number of Full rotation taken)}}\]…………. (1)
Principle
The screw's linear distance traveled is proportional to the spin applied to it. The smallest distance that the instrument can reliably measure is the linear distance moved by the screw when rotated by one division of the circular scale. It's known as the instrument's least count.
Least Count of the Screw Gauge
When the tip of the screw gauge is turned by one division of the head scale, the least count (LC) is taken.
The formula for calculating least count is given by:
Least Count =\[\frac{\text{(Pitch)}}{\text{(Total number of divisions in the circular scale)}}\] …………. (2)
Zero Error and Zero Correction
By looking at the screw gauge image, one needs to consider the zero error in the calculation. The zero error can be calculated by completely rotating the screw until it touches the anvil. Make sure that the edge of the cap is located at the zero marking. The screw gauge needs to be kept vertical so that its zero is facing downward.
By attaining the same position, you can come across three circumstances:
The zero marks from the circular scale align with that of the reference scale. Here, no scope of zero error or zero correction can be found.
The zero marks from the circular scale actually remain above that of the reference scale. Here, the zero error is considered positive, while the zero correction is negative.
The zero marks from the circular scale are actually below the reference line. Here, the zero error is considered negative, while the zero correction is positive.
Procedure
In order to properly conduct the experiment, make sure to go through the following procedure carefully:
Determine the screw gauge's pitch (1) and least count (2) using the above equations.
To determine the zero error, make contact between the anvil and the screw. Perform it three times and keep track of the results. If no zero errors occur, the value 'zero error nil' is recorded.
Using the ratchet head, move the screw away from the anvil, insert the lead shot, and then return the screw to its original position. Stop then and there if the ratchet slips without moving the screw.
Count the number of pitch scale divisions visible and uncovered by the cap's edge. The pitch scale reading (PSR) is denoted by the letter N.
Count the number (n) of circular scale divisions that cross the reference line.
To measure the diameter perpendicularly, repeat steps 4 and 5 after rotating the lead shot by 900 degrees. Fill in the blanks with your observations in the tabular column.
Calculate the total reading by using the equation gives as:
t = PSR + corrected HSR = N+(n x L.C) and apply zero correction in each case.
Find the mean of the various values.
Make sure to insert the sheets in between the studs of the screw gauge. Take the calculation of thickness from five different positions.
Make sure to calculate the average thickness, while determining the correct thickness by zero error.
Experiment Observation Table
Calculation
Least count _____ mm
Zero Error _____ mm
Mean thickness of the paper _____ mm
Mean corrected thickness of the paper
Thickness observed through screw gauge – Zero error _____ mm
Final Result
As a result, the thickness of the given sheet of paper comes out is _____ mm
Sources of Error
The thickness of the sheet may not be consistent.
Although backlash-related errors can be reduced, they cannot be entirely eliminated.
FAQs on To Measure the Thickness of a Given Sheet Using Screw Gauge
1. What is the screw gauge's principle?
The screw gauge operates on the idea of travel. On the huge scale of the screw gauge, there is a direct movement when the screw is rotated. The minimal length is calculated using this scale. The pitch of the screw gauge is the distance traveled by the rotating cable for each rotation.
2. What does it mean by backlash error?
In order to make room from the play of the screw, there is a little space from the nut. With gradual usage over time, this space starts to increase. So, when you turn the screw in one direction, the stud tends to move the same. As for the opposite direction, the stud is expected to move in the same manner, but it suddenly stops for a while. This particular error is commonly termed as a backlash error. In other words, backlash error can be defined as the one that is introduced on moving the nut in another direction.
3. What are the physical attributes that contribute to error in screw gauge?
By looking at the screw gauge diagram, one can find there are three physical attributes that can cause errors in screw gauge. The first and foremost one is temperature. Since, screw gauge is made out of metal, upon the increase in temperature, its diameter tends to increase proportionately. The second source of error is manufacturing defects. In fact, no two screw gauges can attain the same precision due to the error. Lastly, human error is worth considering, too, as it can also create hindrance with the outcome of the experiment.
4. What does the screw gauge's range imply?
The range of the screw gauge refers to the maximum length of the main scale. The metric micrometer screw gauge is designed for sections in the 25mm range. They'll come in sizes ranging from 0 to 25mm, 25 to 50mm, 50 to 75mm, and so on. Tube or three-point micrometers, on the other hand, have lower ranges. Imperial micrometers are available in a variety of sizes, including 0 to 1in, 1 to 2in, 2 to 3in, and so on.
5. Does the diameter of the screw vary as the temperature rises?
Yes, the temperature has an impact on the screw diameter. As the temperature rises, the diameter of the screw increases, and as the temperature decreases, the diameter of the screw decreases.
6. What resources on Vedantu can students use to learn more about screw gauges, such as functioning principles, formulas, and so on?
Students may learn more about the screw gauge topic of physics on Vedantu, which is explained by subject experts. The best part is that students can enroll in free online tutorial classes to get answers to their problems.
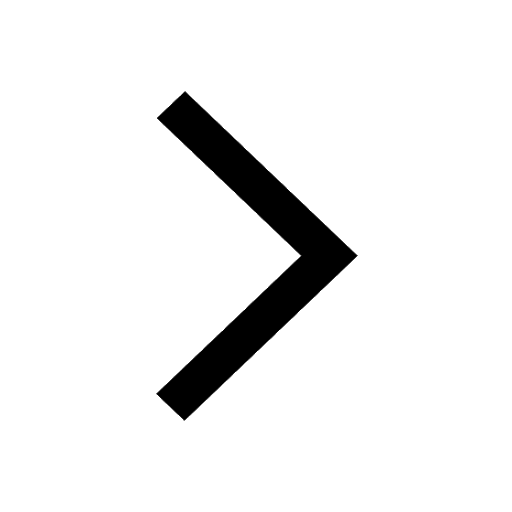
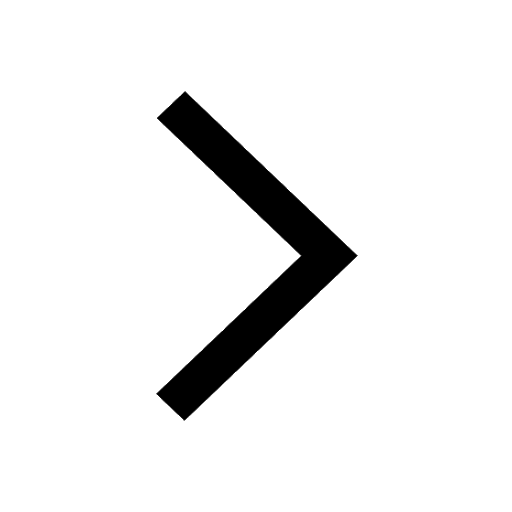
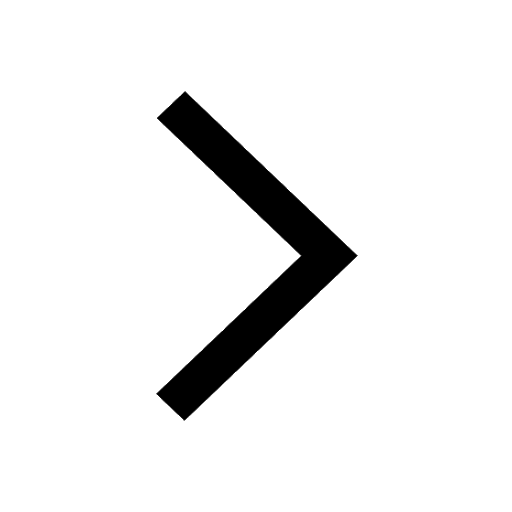
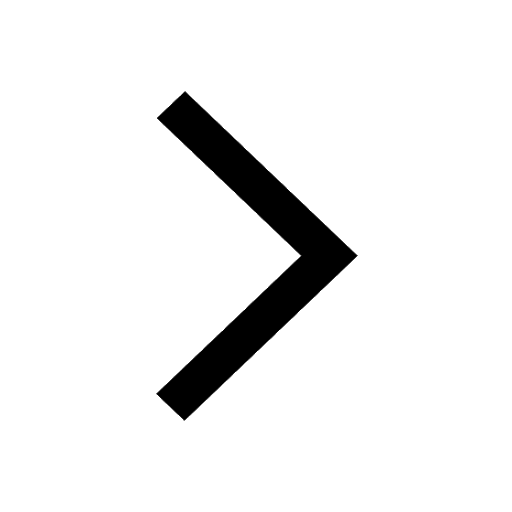
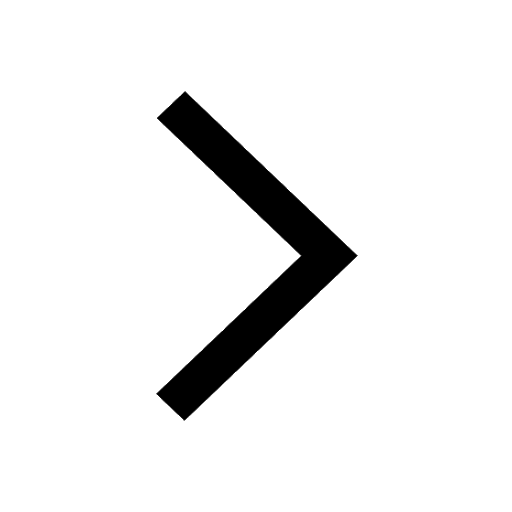
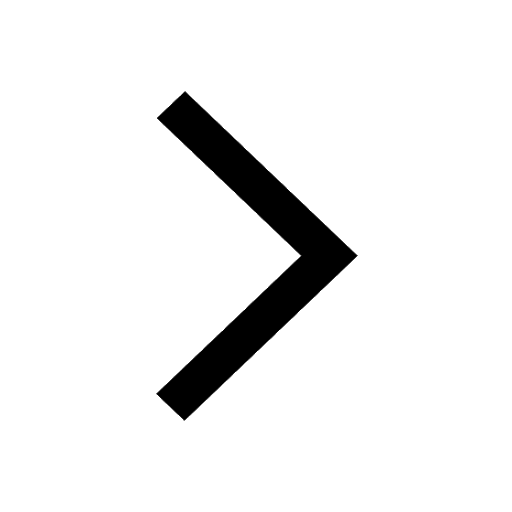