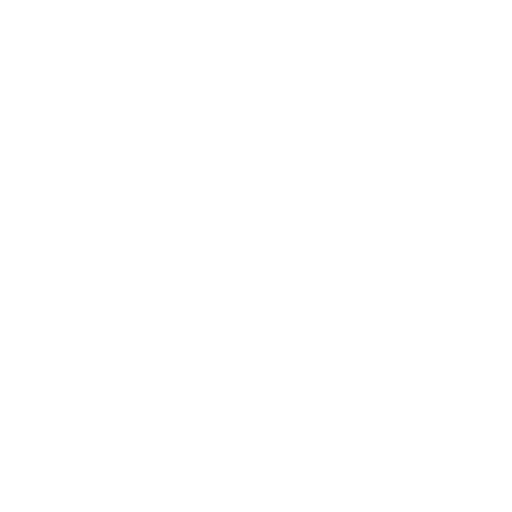

Prevention of Rusting of Iron - Methods and Examples
Several metallic materials in course of the time develop chemical changes on their surface, if left unused, or stagnant. These changes are known as corrosion. Corrosion is a process that leads metals to a gradual degradation. It will happen on iron and its alloys such as steel. Rusting of iron is one of them. Iron objects react with the oxygen present in the air and develop rust in a humid environment. The other examples of corrosion are tarnish on silver and the blue-green patina on copper.
Rust is basically an iron oxide. Mostly, red oxide is formed by the redox reaction between oxygen and iron in the presence of air moisture and water. It was researched that surface rust is friable and flaky and does not provide any protection to the iron. ‘Green rust’ is developed when iron reacts with chloride in the presence of water and oxygen which is mostly found in the underwater iron pillars.
What is the Chemistry Behind the Rusting of Iron?
The formation of rust takes place in the presence of water and oxygen on iron or some of its alloys. The reaction needs a considerable long time to develop. The formation of bonds between iron atoms and oxygen atoms makes iron oxides. The rusting of iron includes an upsurge in the oxidation state of iron with a loss of electrons. The rust chemical formula can be written as Fe2O3.3H2O (hydrated iron (III) oxide).
Rusting of iron reaction: 4Fe + 3O2 → 2Fe2O3
Fe2O3 reacts with water and forms Fe2O3.3H2O.
Rust is developed from two different iron oxides that are different due to their oxidation state in the iron atom. These oxides are
Iron (II) oxide or ferrous oxide - The oxidation state of iron in this compound is +2 and its chemical formula is FeO.
Iron (III) oxide or ferric oxide - in which the iron atom shows an oxidation state of +3. The chemical formula of this compound is Fe2O3.
We all know that oxygen is an excellent oxidizing agent while iron is a reducing agent. So, the iron atoms willingly provide their electrons to oxygen when exposed to it. The rusting of iron involves the process:
Fe → Fe2+ + 2e-
The oxidation state of iron changes due to the oxygen atom in the presence of water.
The ferrous ions get oxidized to ferric ions in presence of moisture and air, also generating hydroxyl ions and yielding ferric hydroxide.
4Fe2+ + O2+ 2H2O →4Fe3+ + 4OH-
Fe3+ +3OH- → Fe (OH)3
Fe (OH)3 converts into Fe2O3.3H2O.
Factors that Affect Rusting of Iron
All the chemical reactions of rusting are dependent on the presence of water and oxygen. The rusting of iron can be controlled by restricting the amount of oxygen and water surrounding the metal.
Why is Rusting an Undesirable Phenomenon?
Rusting is known as a great destroyer of things. It can destroy cars and other vehicles, sink ships, fell bridges, spark the fire, and destroy everything that is made up of iron or its alloys.
The entire piece of metal may disintegrate and be turned to rust when left unattended for extended periods. This can cause many problems as iron is used to construct buildings, bridges, automobiles, etc. Rust makes the metal weaker as oxidized metal is weaker than the original metal itself. It also makes the metal brittle and puts it at risk of breaking.
Iron is also used to make water pipes and storage tanks. If this iron rusts, the pipes can get damaged. They can also increase the amount of iron oxide in the water being transported. Rust also acts as a breeding ground for bacteria. If a person is injured by rusted iron, he/she could be at risk for tetanus.
How can Rusting be Prevented?
Paint Coating
Rusting can be prevented by many methods. One method is to keep iron from corrosion by painting it. The layers of paint resist oxygen and water to form rust on the surface of iron as paint prevents iron from contacting them directly. The iron is protected from corrosion as long as the paint is there. Oil-based paints are hassle-free and the most highly recommended. Alternatively, any organic paint with a 15-25µm thickness may be used to prevent rust.
Alternatively, rusting can be prevented by thermoplastic or a thermoset polymer powder coating on the iron surface. Powder coating is considered superior to paint as it gives a thicker protective layer. Spraying a dry, organic powder onto the iron surface and heating the iron to the melting point of the powder. Once melted, the powder creates an even layer over the iron surface. Common materials used for powder coating include vinyl, polyester, nylon, acrylic, urethane, and epoxy-based organic materials.
Iron Alloys
Other strategies include iron alloying with other metals. For example, stainless steel is mostly made up of iron with a little amount of chromium.
Galvanization
In a different strategy, iron is galvanized or zinc-plated. Zinc has a lower reduction potential which enables it to oxidize more easily than iron. Zinc is a more active metal. This process is known as galvanization. The metal (iron) is covered with another metal such as zinc to form a protective layer. Galvanization can be done in two ways:
Hot-dip Galvanization: that involves dipping the iron into a very hot bath of melted zinc
Electro-Galvanization: Involves using zinc metal as an anode, iron as the cathode, and passing electricity through a zinc solution to apply an even coating of zinc on the iron surface.
Electro-galvanization is the preferred method of galvanization today as it produces an even coating, unlike the hot-dip method.
Cathodic Protection
An important method to protect iron from rusting is to make it a galvanic cell cathode. This process is known as cathodic protection. It can be used for metals, not only for iron. In this process, iron is connected with a more active metal such as magnesium or zinc. The more active metals have a lower reduction potential. Then, the other metal (iron) behaves as a cathode and does not get oxidized. This process is highly useful to the storage of iron tanks underwater when anodes are monitored properly and replaced timely. This process is also used to protect metal parts of water heaters.
FAQs on Methods of Prevention of Rusting of Iron
1.What is Rust? What is the equation for the formation of rust?
Rust is a reddish-brown discoloration that builds upon the surface of Iron. Rust is basically a form of iron oxide (Fe2O3). When the surface of Iron is exposed to the air for a long enough period of time, then the iron gets oxidised forming iron oxide, Fe2O3. This substance that is formed after the oxidation of the iron is what is called rust. Given enough time under the right conditions, any object made of iron will eventually develop rust.
This formation of rust on the surface of iron can be expressed in the chemical equation given below -
4 Fe (the surface of iron) + 3O2 +2x H2O → 2 Fe2O3 . x H2O
2.Write down the conditions necessary for the rusting of the Iron?
Certain conditions must be met beforehand, in order to start the process of rusting of iron. These certain necessary conditions for the rusting of iron are-
Moisture - The presence of moisture or water in the atmosphere near the surface of iron, or directly on the surface of iron is what facilitates the process of rusting. Rains are often one of the major reasons for water.
PH value: If the pH of the surrounding around the metal or iron is reduced, then the process of rusting becomes even faster. Rains but more specifically acid rains have lower pH values too, so it is a greater threat to the iron appliances.
Impurity: The presence of various salts in the water, will result in a faster rate of rusting. And also the impurities present in iron itself also tends to make the iron more prone to rusting.
3.Write down the experiment to prove that air and moisture are essential for rusting.
Procedure for a simple experiment to prove that air and moisture are essential for the process of rusting.
Take three iron nails and put them in the three different test tubes labelled as A, B, and C.
Fill the first test tube A with running tap water.
Add distilled water in the second test tube B, with 1 ml of oil on top of it, and tightly seal it.
For the last test tube C, add some amount of anhydrous calcium chloride and tightly close it.
Allow them to remain as such for a few days.
Observation and conclusion: The iron nail gets rusted in test tube A, but not in test tubes B and C. In test-tube A, nails are exposed to both air and water, while in test tube B, the nails are exposed to water but not air and in test tube C, nails are prevented from having contact with water, but let the dry air as it is. By all this experiment, we can say that the Iron only gets rusted when both air and water are present in the surrounding.
4.How to Prevent the process of rusting?
There are many issues caused by the rusting of iron and hence many processes are developed to stop the process of rusting of iron. Some of these methods are procedures are listed below:-
Adding a coat of paint on the surface of the iron can prevent the rusting enormously.
Applying grease and oil are very helpful too.
The process of galvanisation is a very famous way to prevent rusting on the outer walls.
Electroplating on the surface of the iron items.
By making use of alloys rather than pure iron metal like stainless steel which has lower chances of getting rusted.
5.What are the damages caused by Rusting of Iron objects?
The process of rusting eats away the upper surface of the iron metal, exposing the surface to the risk of rusting. All this wear and tear of the iron makes it flaky and weak, rendering the iron object worthless.
Rusting is a big issue due to the wide range of use of iron. Iron is used to create buildings, vehicles, railings, grills, ships, and even satellites. Rusting of iron in objects can cause serious problems, and in some cases can be deadly. Hence, scientists have developed many ways to protect iron from rust.
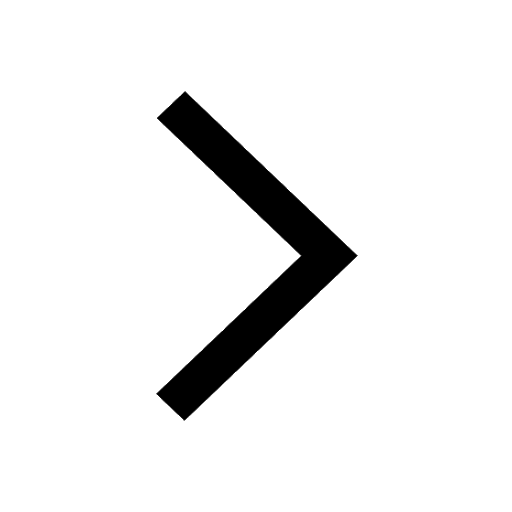
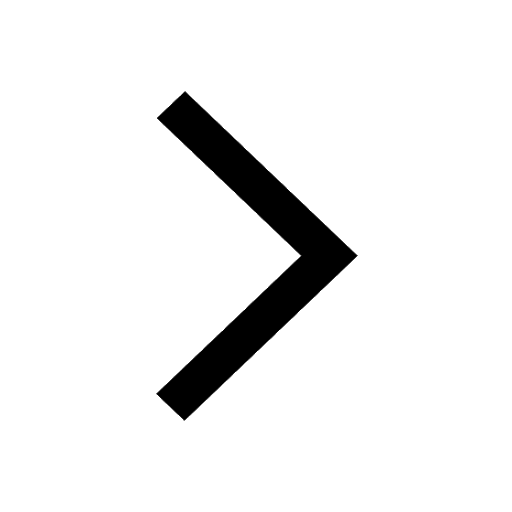
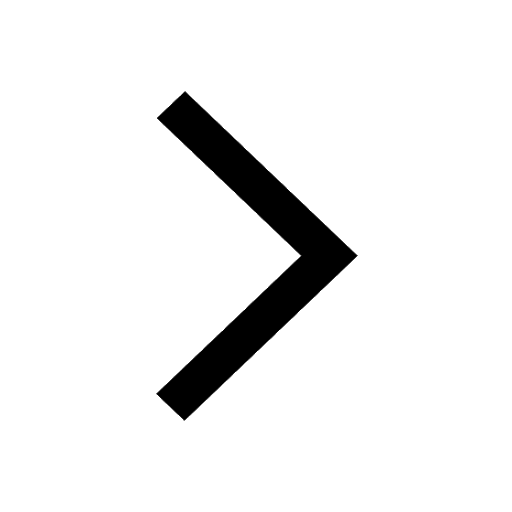
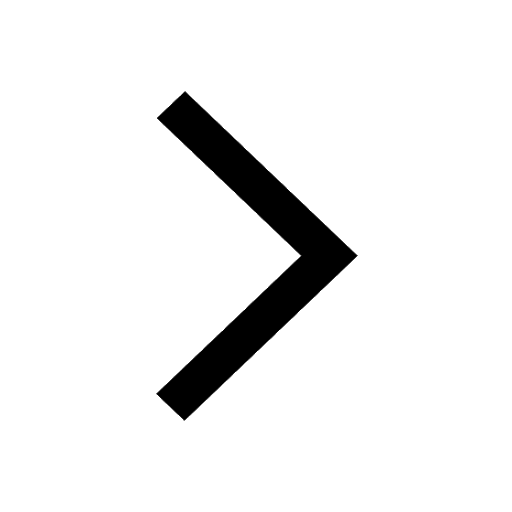
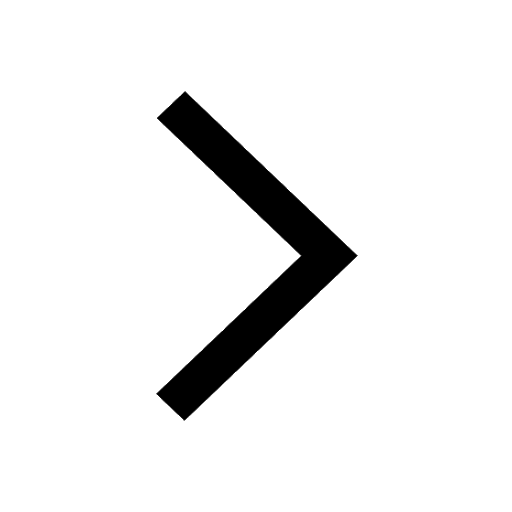
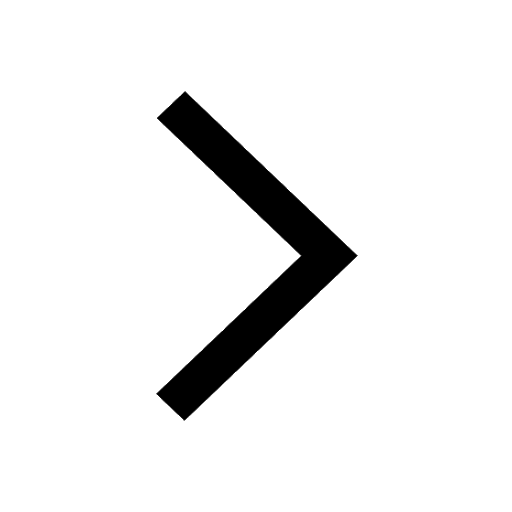