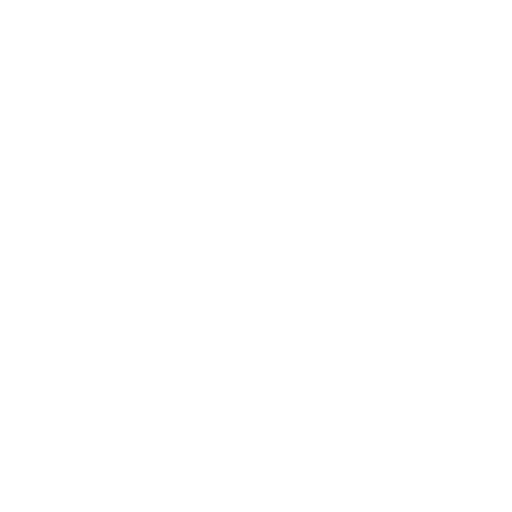

What is Distillation?
Distillation, also known as classical distillation, is a process of separating the two or more components or substances by converting the liquid into vapour and then substantially condensing back the vapours into a liquid state. Dry distillation is a heating process where the solids are heated to form the vapours which are then condensed to liquid or solid form. Chemical changes are involved in the dry distillation like that of the cracking or destructive distillation. In the distillation process either the targeted liquid is completely separated to a pure state or is partially separated that increases the concentration of that particular component in the mixture. In either of the cases, the distillation is based on the difference in the relative volatility of the components that are present in the mixture.
The boiling point of that component will decrease as the process of distillation progresses. Slowly and eventually the temperature inside the apparatus will start to change. Until the boiling point of the next lowest boiling element is obtained the temperature will keep on increasing. After the temperature stabilises again, another pure fragment of the distillate can be collected. This fragment of distillate will be originally the element that boils at the second-lowest temperature. This process must be repeated until the first mixture has been separated.
Process of Distillation
Check the adjustment of the thermometer that will be utilised. This can be practised by putting the thermometer in an ice bucket of distillate water. As the thermometer reaches the level of thermal equilibrium, place it in a cup of boiling distilled water and again allow it to achieve the level of thermal equilibrium. If the temperature differs from the estimated value by 2 degrees then use a new thermometer and check its calibration.
Fill the distillation flask. Only two-thirds of the flask should be filled because there should be proper space left above the surface of the liquid so that when the boiling starts the liquid does not move into the condenser. The boiling pieces should be installed in the distillation flask for 2 reasons: they will prevent superheating of the fluid being distilled and they will help in causing a more controlled boil, this eliminates the probability of the liquid falling out of the distillation flask into the condenser.
Start heating the distillation flask until the water starts boiling (Picture 4). Vapours will start to move upwards through the neck of the distillation cup. As the vapours go through the condenser, they will gather and drip into the collection receiver (Picture 5). A proper rate of distillation is around 20 drops per minute. The process of distillation should be slow so that the vapour condenses to liquid in the condenser. Numerous natural compounds are flammable and if vapours go through the condenser without condensing, they may cause a fire as they meet the heat source.
The temperature on the thermometer changes slowly when the distillate falls from the condenser. At the point when the temperature stabilises, use another receiver to gather every one of the drops that form over two to three degrees range of temperature. As the temperature rises once more, change to a third receiver collector to gather the distillate that is formed now. This procedure should be performed time and again; utilising a new collector every time the temperature stabilises or starts changing, until most of the distillate has been gathered in discrete fractions.
Remove the heater from the distillation before the whole liquid evaporates. On the off chance that most of the fluid is distillate away, there is a risk that peroxides, which can ignite or explode, might be present in the residue left behind. Additionally, when most of the fluid has evaporated, the temperature of the glass of the filtration jar will rise very quickly, perhaps igniting whatever vapours may be left in the distillation flask.
Never distil to dryness. The residue left in the distillation jar may contain peroxides, which could ignite or detonate after all the fluid has distillate away.
Ensure that all joints are airtight. If any vapour escapes at the joints, it might come into direct contact with the heater and ignite.
Never heat a closed container, the increasing pressure might cause the glass to explode If the distillation flask has a narrow neck, then the thermometer should be placed in such a way so that the vapour cannot exit the flask. Ensure that if using a narrow neck jar, the thermometer is not resting in the lower portion of the neck.
Simple distillation is successful only while separating a volatile fluid and a non-volatile fluid or while separating 2 fluids whose boiling point differs more than 50 degrees. If the fluid used in the distillation process has a boiling point closer than 50 degrees to one another, the distillate gathered will be richer in the volatile compound but not to the degree required for complete separation of the individual compounds.
The fundamental thought behind fractional distillation is the same as simple distillation: the procedure is repeated again and again. If simple distillation was applied to the mixture of fluid having similar volatilities, the processed distillate would be concentrated in a more volatile compound than the first mixture, but it would still contain a specific amount of high boiling compound. If again simple distillation was performed the distillate would get more concentrated and have a lower boiling point, but still, some of the distillate would be left out with a higher boiling point. If the simple distillation is repeated again then a pure distillate can be formed.
This may take a long time. In fractional distillation, the vapours formed from boiling rise into the fractionating cylinder where they condense on the cylinder’s packing. This condensation is more concentrated in the lower boiling compound than the mixture in the distillation jar. The liquid condensed will re-vaporize when the vapour rises through the cylinder. In every fractional distillation, the vapour is more and more concentrated in a more volatile substance. The continuous re-condensing of the vapour gets affected by the material it is packed with and the length of the fractional cylinder.
The fractionating column is used to supply a temperature gradient over which the distillation can occur. In an ideal situation, the temperature in the distillation flask would be equal to the boiling point of the mixture of liquids and the temperature at the top of the fractionating column would be equal to the boiling point of the lower boiling compound; all of the lower boiling compound would be distilled away before any of the higher boiling compound. In reality, fractions of the distillate must be collected because as the distillation proceeds, the concentration of the higher boiling compound in the distillate being collected steadily increases. Fractions of the distillate, which are collected over a small temperature range, will be essentially purified; several fractions should be collected as the temperature changes and these portions of the distillate should be distilled again to amplify the purification that has already occurred.
The procedure of simple distillation is very similar to those used in fractional distillation, the equipment that is used in the process are also similar. There is only one difference between the equipment used is that with fractional distillation, a wrapped fractional cylinder is attached to the top of the distillation jar and under the condenser. This gives the surface area on which rising vapour condenses and re-vaporises.
The fractionating cylinder is used to transfer a temperature gradient over which the distillation can take place. In a perfect situation, the temperature at the top of the fractionating cylinder would be the same as the boiling point of the lower boiling compound and the temperature in the distillation jar is the same as the boiling point of the mixture of the fluids. Fractions of the distillate must be gathered so that when the distillation proceeds, the concentration of the higher boiling mixture in the distillate being gathered slowly increases. The fractions of distillate that are gathered over a small temperature range will be effectively purified; some fractions shall be gathered as the temperature changes and these portions of the distillate shall be distilled once more to increase the purification that has already taken place.
Types of Distillation
There are certain types of the distillation process that are discussed below:
Simple Distillation: Simple distillation involves the boiling of the liquid mixture to the vapour state by heating it to its boiling point and then immediately converting the vapours into the liquid state by condensation of the vapours. This method is only applicable for the mixtures whose boiling point has a large difference where the minimum difference that can be noted is 250C. The purity of the purified liquid that is termed distillate is governed by Raoult's law.
Fractional Distillation: The mixture of liquids that have a similar boiling point undergo fractional distillation for the separation process. Several evaporation-condensation steps are involved in fractional distillation that usually takes place in the fractional column. This process is also known as rectification. The apparatus that is required to perform the fractional distillation are given below:
Distillation flask or round bottom flask
Distillation column
A fire or a hot bath both are sources of heat.
Receiving flask that is used to receive the condensed vapours
A thermometer is used to measure the temperature of the distillation flask.
Condenser
Standard glassware
When the liquid is heated in the round bottom flask, the vapours of the liquid mixture rises into the fractionating column. A thermometer is fixed on the mouth of the fractional column in order to read the temperature rise. The vapours then enter into the condensation chamber also known as a condenser and then are cooled and condensed on the wall of the condenser. Now the hot vapours that are emerging from the distillation flux heat the condensed vapours creating new vapours.
A large number of evaporation and condensation cycles takes place and the purity of the distillate improves with every cycle. An illustration of such a fractional distillation setup is given below.
(Image will be uploaded soon)
Steam Distillation: The heat-sensitive components in a mixture are often separated with the help of the steam distillation process. This is done by passing the steam through the mixture which is then slightly heated to vaporise some of the components. Because of the high heat transfer rate established by the process, there is no need for high temperatures. To afford the required distillation, the resulting vapour is condensed. To obtain essential oils and herbal distillates from several aromatic flowers/herbs the process of steam distillation is used.
Vacuum Distillation: Vaccum distillation is eligible for separating the liquids that have very high boiling points from the liquid mixtures. Thus it becomes impossible to raise the temperature to reach the high boiling point of the liquids. Hence the pressure is lower instead. The lowering of the vapour pressure helps the liquid with a high boiling point to boil at a much lower temperature. When the vapour pressure of the component becomes equal to the pressure of the surroundings, then the liquid converts into its vapours. Then the vapours are condensed and collected in the distillate. high-purity samples of compounds that decompose at high temperatures are used to obtain the through vacuum distillation.
Air-Sensitive Vacuum Distillation: Some of the compounds or the substances that are sensitive to air or react with the air readily, their distillation is carried out in a vacuum but the vacuum must be replaced with the inert gas once the distillation process is completed. Such a process is known as air-sensitive vacuum distillation.
Short Path Distillation: The small quantity of the components that are unstable at a high temperature is being purified with the help of the short path distillation. This is basically done at a lowered pressure due to which the distillate that is formed travels a very small distance before it gets collected. The reduced distance between the collected distillate and the path travelled by it in this method also reduces the wastage of the distillate that gets accumulated in the wall of the apparatus.
Zone Distillation: The process of partial melting of a substance and the condensation of the resulting vapours to obtain a pure distillate is known as zone distillation. With the help of a zone heater, this process is carried out in a long container.
Uses of Distillation
A large number of the items we utilise each day are the results of distillation, from the fuel that controls our vehicles to the water we drink. Distillation is a physical procedure that utilises heat to filter or separate a mixture containing at least one fluid. As a mixture is heated, the fluid with the most minimal boiling point will boil and transform into vapour, deserting any solid material or different fluids. The vapour is caught and cooled until it gathers, bringing about a purified adaptation of the fluid.
Scientific Use
One natural use of distillation is in the lab. While the results of this kind of distillation may not discover their route specifically into our homes, the procedure is utilised consistently in the compound and pharmaceutical research, quality affirmation testing for some customer items and law requirement crime scene investigation.
Water Purification
Water from regular sources contains a mixture of minerals and different particles. These mixtures include a lot of particles which can be removed by distillation. Distillate water is normally utilised in circumstances where the proximity of minerals may decrease the viability of certain equipment, for example, in steam irons. A few people drink distilled water since they like the taste or need to keep away from the minerals found in contaminated water. Parents will frequently utilise distilled water while cooking some food for their babies. Desalination plants additionally use distillation to transform seawater into drinking water.
Alcoholic Beverages
Distillation is utilised to create a selection of mixed refreshments, for example, bourbon, rum and liquor. Whenever products of the soil materials age, a weakened variant of ethyl liquor is created. A selection of different segments, for example, water, esters and different kinds of liquor, are additionally gathered between the distillation procedure, which represents the one of a kind of every alcoholic soul.
Petroleum Products
Various items can be created from raw petroleum. Since every one of these items has a one of a kind boiling point, a procedure known as partial distillation is utilised to refine oil into isolated materials. These incorporate gases, diesel fuel, greasing up oil, fuel oil, paraffin wax and petrochemicals.
Perfume
One of the earliest employments of distillation was to make aroma, which started around 3500 B.C. The fragrance from different plants and herbs is contained in what are known as fundamental oils, which can be extracted through distillation. Be that as it may, numerous fragrant plants will in general deteriorate at high temperatures so partition by typical distillation isn't possible. In those cases, steam is passed through the plant material to draw out the basic oils without consuming the mixture. The steam is then caught and consolidated similarly as in typical distillation.
FAQs on Distillation
1. What are the three steps that are involved in distillation?
The three steps that are involved in the distillation process that is common for all the distillation processes are fermentation, distillation and finishing.
2. What is a distillation plant?
A distillation plant is a large-scale distillation solution that can be used for commercial or manufacturing purposes. Rather than single drop counter distillation, large scale distillation plants are much more capable of producing pure distillates.
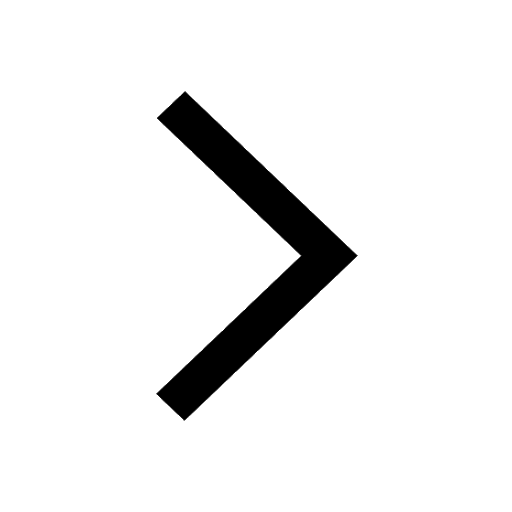
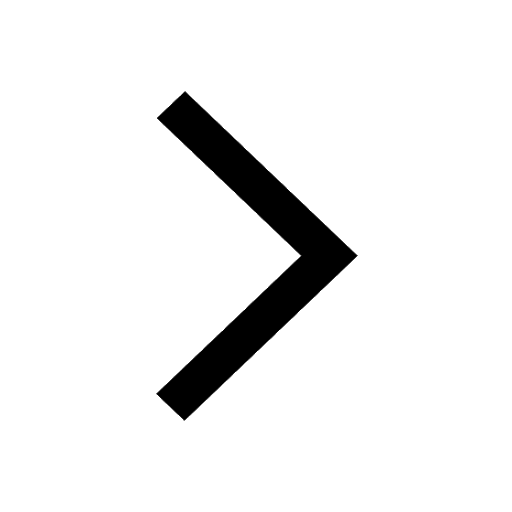
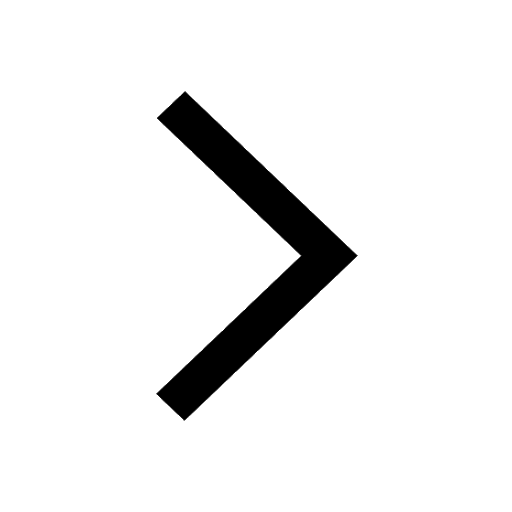
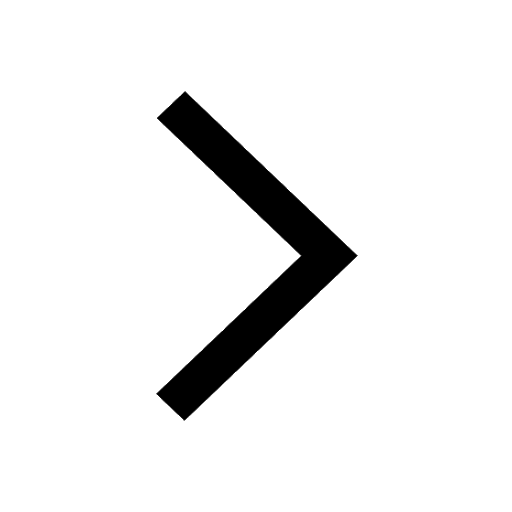
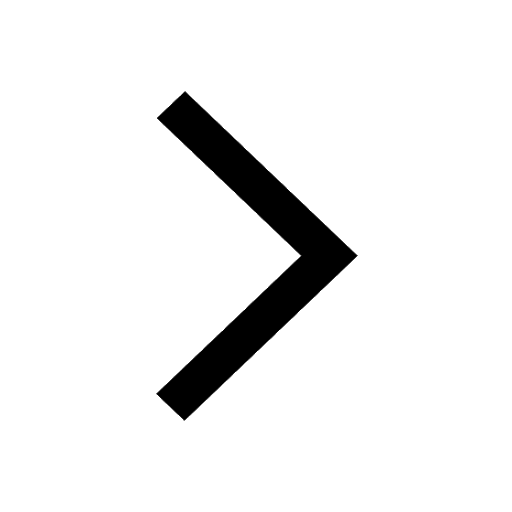
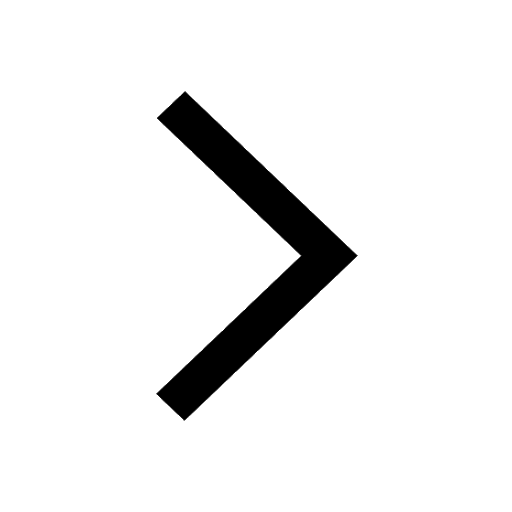