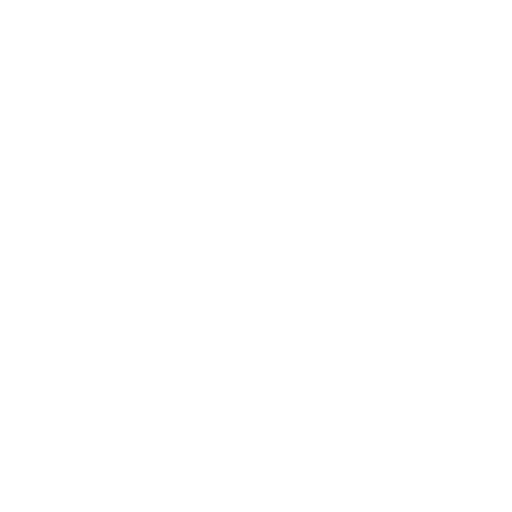

A Brief Introduction to the Concept of Spring
Springs are frequently used in our commonly-used electronic gadgets and the batteries that power them. Long before there were electronic toys, springs were crucial to the toy manufacturing industry. Here, we will learn about springs, their various classifications, free length, mean diameter, and index.
Spring is a material that can be bent by force and can recover to its original form once the force is released. Although there are many types of springs, the most common type is probably the metal coil spring. From ballpoint pens to racing car engines, springs are a necessary component of almost all sophisticated mechanical equipment.
Classification of Springs
1. Based on the Load Applied:
Torsion Spring: The spring's applied twisting force or torque causes this. A mousetrap and a clothespin, for instance.
Compression Spring: This operates due to the force generated by a compressed load. These are utilized in spring mattresses, retractable pens, and shock absorbers.
Extension Spring: It is typically utilized in garage door mechanisms and functions under tensile pressure.
2. Based on the Displacement due to Force Applied:
Constant Force Spring: A steady force is used to expand the spring. Clock spring is another name for it. It is employed in clocks and monitor screen adjustments.
Variable Rate Spring: The spring rate is not constant along the entire axial length. There are three different varieties, depending on the spring rate.
Linear Rate Spring, whose spring rate is constant.
Progressive Rate Spring, including adjustable spring rate
Dual Rate Spring comprised of soft spring rate and form rate
Linear Spring: These are linear constant force helical springs.
3. Based on How They’re Made:
Coil Spring: These springs are produced from metal wires that have been formed using a CNC coiling machine, and they are thin and light. To acquire spring characteristics and develop shape, the springs that emerge from this machine must be heated.
Flat Spring: Metal components are stamped into a sheet to create these. To shape, these are also heated. These come in a variety of shapes and sizes and also include coiled flat springs. They are utilized in clock springs, volute springs, retainer clips, and spring washers.
Molded Spring: These springs are constructed from corrosive or plastic materials. These creep and are typically utilized in irregular cycles. Its use is observed in manufacturing food, marine applications, and medicine.
Machined Spring: These are employed in heavy-duty applications that demand both high strength and precision. It is utilized in mills and lathe machines.
The Free Length of a Spring
A spring's real length when no force is being applied to it is known as its "free length" (it is not being deflected). There are several techniques to measure a spring's free length, and each one is dependent on the kind of spring you are using. For compression springs, you simply multiply the overall number of coils by the length of the spring wire per coil.
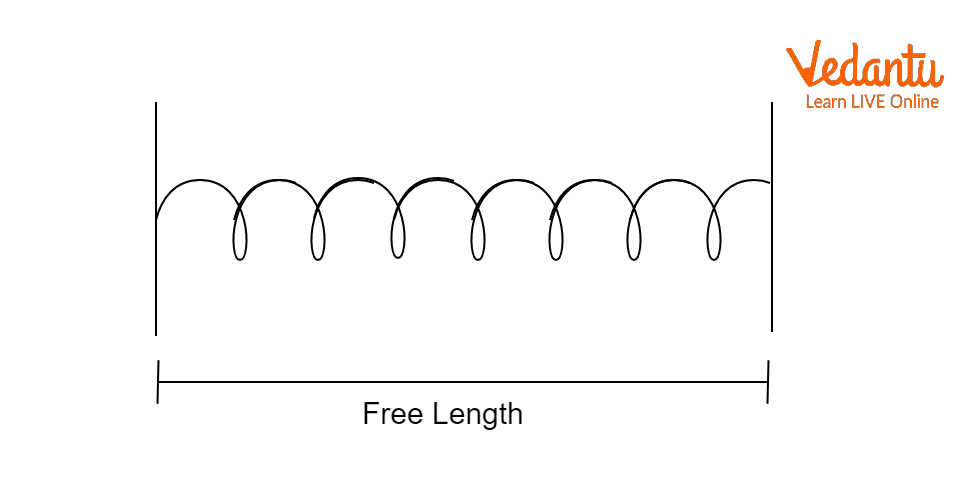
Free Length of Spring
For extension springs, you follow the same procedure, but you also increase the number of active coils by two. A torsion spring's free length is calculated by adding the leg lengths and multiplying the length of the spring wire per coil by the total number of coils.
Formula for Free length:
$\text{Free length }=\text{Solid length}+\text{ Total axis gap}+\delta $
Where,
$\text{Total axial Gap between Coils of Springs}=\text{ (Total number of coils}-1\text{)}\times \text{Axial Gap between Adjacent Coils Bearing Max Load}$
$\text{Solid length of spring}={{N}_{t}}d$
Where ${{N}_{t}}=$ Total number of coils
d = diameter of coil
Pitch of a Spring
Like the threads (lead) on a bolt or screw, the pitch of a spring is the distance between the centers of one coil and the adjacent coil. A compression spring's pitch is particularly crucial because it directly affects how the suspension behaves. For instance, a compression spring with a higher pitch for the same length is more powerful than one with a lower pitch.
By measuring the distance between the spring's coils and then multiplying that value by the wire thickness, it is occasionally possible to approximate the pitch of the spring. However, when springs are in use, they are dynamic and subject to various stresses. As spring pitch can be difficult and frustrating to measure on the surface of spring, it might be best to use a formula or computer program to help you pinpoint it.
Pitch of a Spring Formula:
$\text{Pitch of coil}=\dfrac{\text{Free length}}{\left( {{N}_{t}}-1 \right)}$
Where ${{N}_{t}}=$ Total number of coils
Mean Diameter of Spring
The I.D. (inner diameter), O.D. (outer diameter), and "mean" diameter are the three diameters of a spring. An average is referred to by the word "mean". The average diameter of the I.D. and O.D. is known as the mean diameter. Since most spring calculations employ this dimension, the mean diameter is significant. Since it is a computed diameter, it cannot be determined by using a set of calipers; rather, it must be discovered mathematically. Standard calipers can be used to measure the O.D. and I.D. because they are quantifiable diameters.
Formula for Mean Diameter:
$\text{Mean Diameter}=\text{Outer Diameter}-\text{ Wire Diameter}$
$\text{Mean Diameter}=\text{Inner Diameter+ Wire Diameter}$
$\text{Mean Diameter}=\left( \text{Spring Index} \right)\times \left( \text{Wire Diameter} \right)$
Spring Index
How securely or loosely a spring is wound is indicated by its ‘index’. As it hints at some likely design issues, this knowledge is particularly helpful to spring engineers. By dividing the mean diameter by the wire diameter, the "index" may be calculated. In spring design, a lowercase ’d’ stands in for the wire diameter, and an uppercase ’D’ represents the mean diameter. The index is in capital letters. The index should typically be more than 3 and lower than 20.
Spring Index Formula
$I=\dfrac{D}{d}$
Smaller index springs are more likely to require additional processing stages to assure adequate life, which increases tooling wear. The diameter and length tolerances for large index springs frequently need to be increased.
Spring Numericals
1. The spring index is 6, the wire diameter is 7mm, and the number of active coils is 8. The actual deflection of the spring is 30.34mm. (It is assumed that the spring has square and ground ends) Determine the mean diameter, total number of coils, free length, and pitch of a coil.
Sol: Given: Spring Index C = 6
Wire Diameter d = 7mm
Number of active coils N = 8
Actual Deflection $\delta$ = 30.34mm
Now, the mean diameter can be calculated using the following formula:
\[D\text{ }=\text{ }C\times d\]
\[=6\times 7\]
\[=42mm\]
Here, it is given that the spring has square and ground ends. So the number of inactive coils is equal to 2.
The total number of coils is given by
\[{{N}_{t}}=N+Inactive\text{ }Coils=8+2=10\]
Here, Total axial gap \[=\text{ }\left( Total\text{ }number\text{ }of\text{ }coils\text{ }-1 \right)\left( Gap\text{ }between\text{ }consecutive\text{ }coils \right)\]
\[~=\left( 10-1 \right)\left( 1 \right)\]
\[~=\text{ }9\]
Now, Free length is given by
Free length = \[{{N}_{t}}d\text{ }+\text{ }Total\text{ }axial\text{ }gap\text{ }+\text{ }Actual\text{ }deflection\]
\[=\left( 10 \right)\left( 7 \right)+9+30.34\]
\[=109.34mm\approx 110mm\]
Now, the pitch of a coil is given by the following formula
$\text{Pitch of coil}=\dfrac{\text{Free length}}{\left( {{N}_{t}}-1 \right)}=\dfrac{109.34}{\left( 10-1 \right)}=12.15\,mm$
Hence, the values of mean diameter, the total number of coils, free length, and pitch of a coil are 42mm, 9, 110mm, and 12.15 mm.
Conclusion
Springs are pliable mechanical devices that regain their original shape after deformation, i.e., after being stretched or compressed. They are an essential part of many different mechanical devices. The force needed or applied to compress or extend a spring on any attached object is known as the spring force. The length of a compression spring when it is not under any load or force is known as the free length of the spring. The correlation between mean diameter and wire diameter is known as the spring index. Similar to the threads (lead) on a bolt or screw, the pitch of a spring is the distance between the centers of one coil and the subsequent coil. The average diameter of the internal diameter and the outside diameter is known as the "mean" diameter.
FAQs on Numericals On A Spring - JEE Important Topic
1. State Hooke’s law.
A metal spring is an elastic item, and the force needed to extend it, up to a point, is precisely proportional to the spring's extension. This is known as Hooke's law and is commonly written:
$F=-kx$
Where $F$ is the force, $x$ is the length of extension/compression and $k$ is a constant of proportionality known as the spring constant , which is usually given in $N/m$.
The negative sign is typically supplied even though the force's direction hasn't been determined explicitly in this case. This shows that the spring's restoring force is directed in the opposite direction from the force that created the displacement. When you pull down on a spring, it will extend downward, producing an upward force because of the spring.
2. What occurs when the spring index is high?
The correlation between the diameter of the wire and the mean diameter of the spring is known as the spring index, which gives us information about the stress induced on a spring, and strength of spring and manufacturability of the spring. The coil diameter can vary greatly when the spring index is high (C > 15). A spring like that is prone to buckling. A spring index between 4 and 12 is regarded as ideal from a production perspective. Consequently, the spring index typically ranges from 4 to 12 in practical applications.
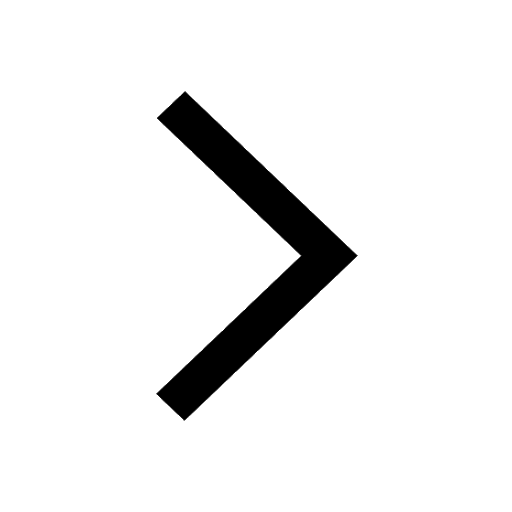
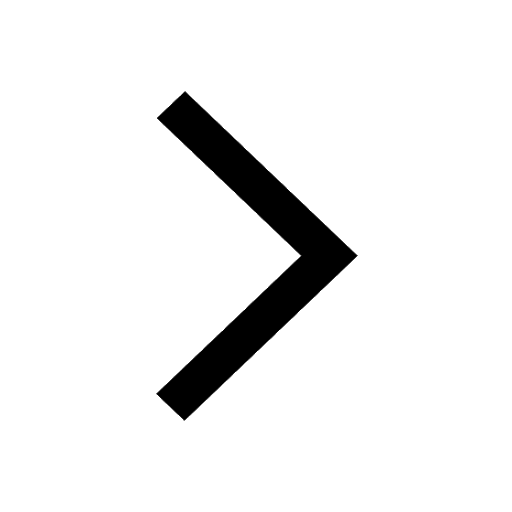
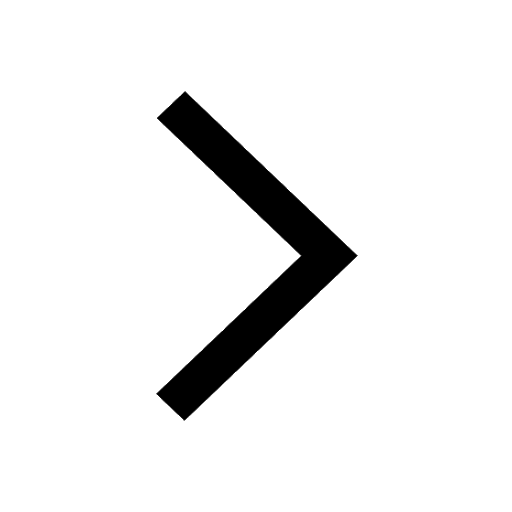
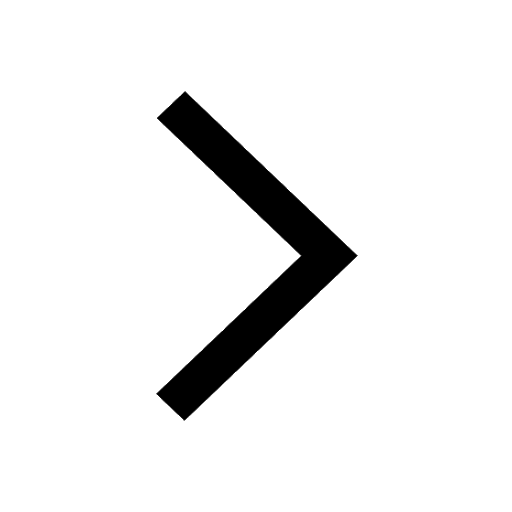
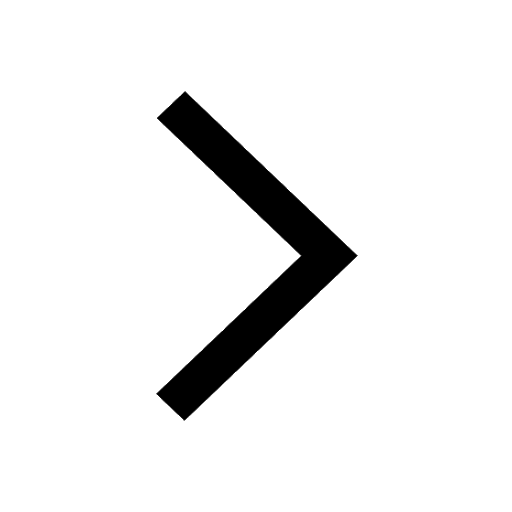
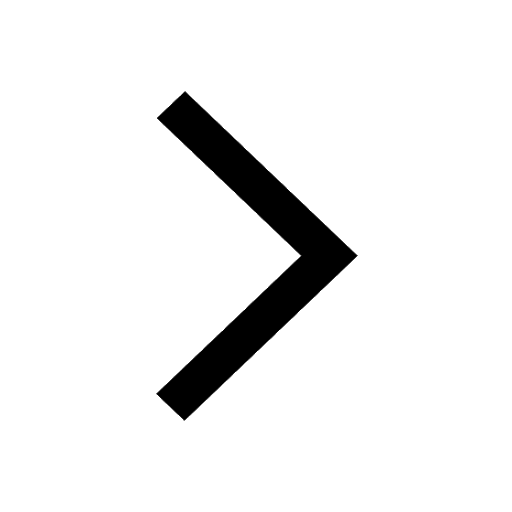
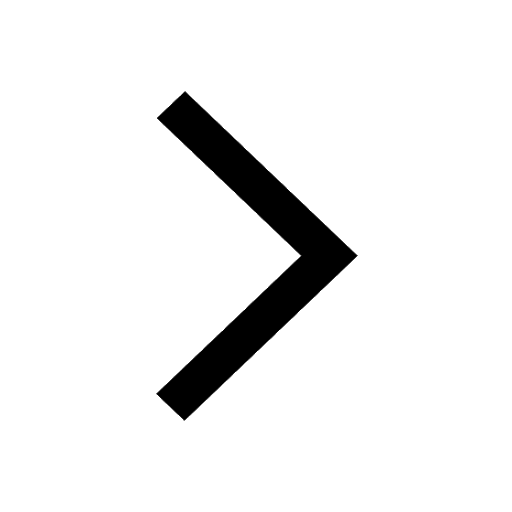
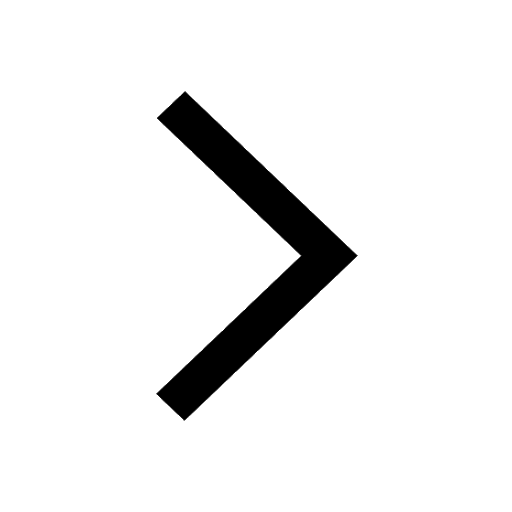
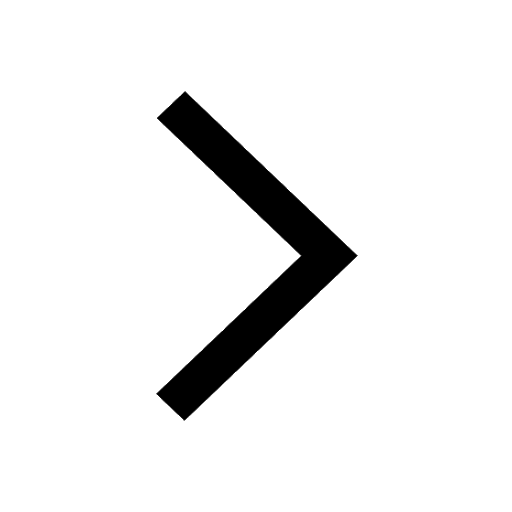
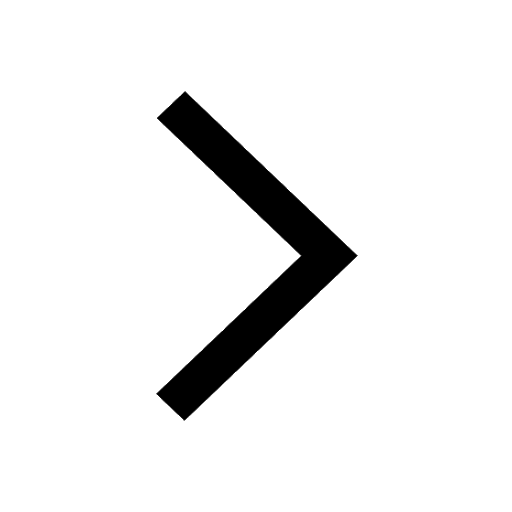
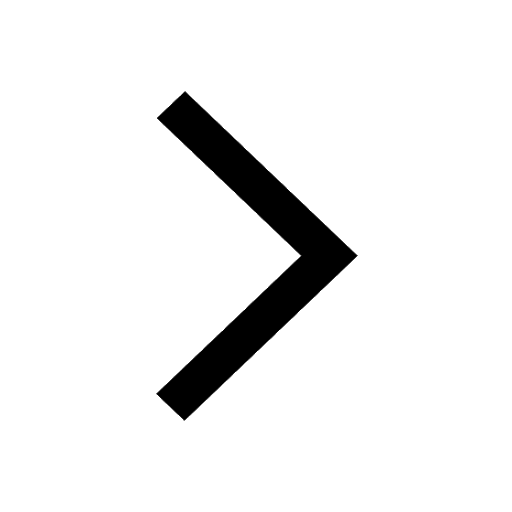
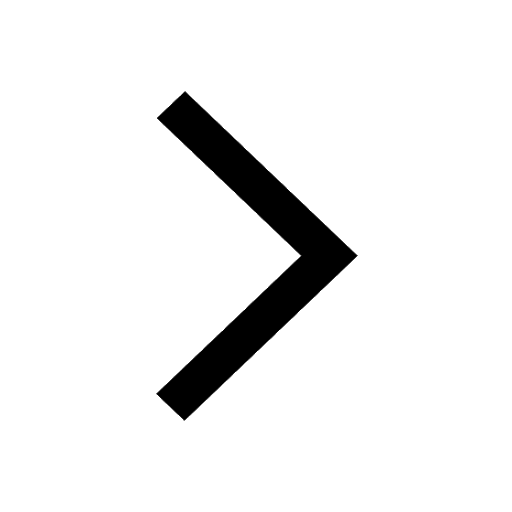