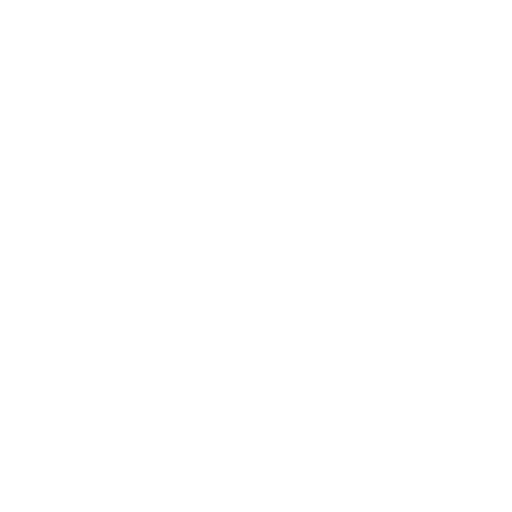

What is Polyurethane Foam?
A polymer which is a composition of organic units and joined by carbamate links is called polyurethane foam. Most of the polyurethanes do not melt on heating and hence are thermosetting polymers, but thermoplastic polyurethanes also exist.
These polymers are commonly and traditionally created by a reaction of di- or tri-isocyanate with one polyol. Some other materials are also added for support to modify the polymer properties or processing of the polymer.
As polyurethane foams consist of two kinds of monomers, that polymerise one by one, they are classified as alternating copolymers. Both polyols and isocyanates utilised to make polyurethanes on an average hold two or more than two functional groups each molecule.
The following image shows the synthesis of polyurethane and polyurethane structure:
Image will be uploaded soon
Raw Materials to Make Polyurethane
Isocyanates
The widely used isocyanates to make polyurethane are aromatic diisocyanates, methylene diphenyl diisocyanate (MDI) and toluene diisocyanate (TDI).
MDI and TDI are cheaper compared to other isocyanates and much more reactive. Industry-level MDI and TDI are simply isomer mixtures, and the former contains polymeric materials. These compounds can be modified by reacting them partially with polyols or with other materials to lessen the volatility (and thus toxicity), reduce their freezing points to handle them easily and improve the characteristics of the resultant polymers.
Polyols
Polyols can be polyester polyols or polyether polyols. The former one is formed by reacting epoxides with compounds having active hydrogen, and the latter is formed by polycondensation of multifunctional polyhydroxy compounds and carboxylic acids. These compounds can be further categorised depending on their end-use. The polyols which have high weight (molecular weight ranging from 2000 to 10000) are utilised to create flexible polyurethane foam and the ones with low weight are used to make rigid products.
Furthermore, due to interest in “green” products, there is a demand for polyols made from vegetable oils. Various kinds of oils are used in preparing polyols like cottonseed, castor, soybean and neem seed. These vegetable oils are made to work in different ways and modified to polyethers, polyetherimide, alkyds, etc. Few renewable sources for making polyols are fatty acids or dimer fatty acids.
Crosslinkers and chain extenders
Chain extenders (f=2) and crosslinkers (f>=3) are amine-terminated and hydroxyl compounds that play a major role in polymer morphology of elastomers, polyurethane fibres, adhesives and specific microcellular and skin foams. The naturally occurring property of these substances is obtained from phase separation of soft and hard copolymer segments in such a way that urethane hard portion domain provides cross-links between amorphous polyester or polyether soft portion domain.
Catalysts
The catalysts of polyurethane can be divided into two wide categories – acid amine and basic amine. Tertiary amine catalysts work by improving the diol component’s nucleophilicity. Oxides, alkyl tin carboxylates and mercaptides oxides work as mild Lewis acids to accelerate polyurethane formation.
Traditional base amine catalysts are triethylenediamine, dimethyl cyclohexylamine, dimethylethanolamine, etc., and dibutyltin dilaurate is a classic Lewis acidic catalyst.
Surfactants
These compounds are utilised for the characteristic modification of non-foam and foam polyurethane polymers. In polyurethane foam, the surfactants regulate the size of the cell, emulsify liquid elements, stabilise the structure of the cell to prevent subsurface voids and to collapse.
After learning the raw materials, let us proceed with polyurethane properties.
Properties of Polyurethane
Polyurethane properties can be classified into physical and chemical ones, and they are as follows:
Physical properties of polyurethane foam
Resilience
Between the polyether and polyester foams, the latter ones have high tensile strength, hardness and elongation at break. Hence, they hold considerable abrasion resistance. The low resiliency of polyether foams is also useful for packaging purposes.
Solvent resistance
These foams are highly resistant to solvents, and the polyester foams are specifically more resistant to dry cleaning solvents.
Discolouration and yellowing
When exposed to UV light, polyurethane foams can become discoloured. The degree of yellowing is dependent on radiation intensity. But, the yellowing of the polymer has no noteworthy effect on the physical properties of polyurethane foam.
Furthermore, non-yellowing foams can also be manufactured by using aliphatic isocyanates, but are more costly than the normal ones.
Chemical Properties of Polyurethane Foam
Upon oxidation, polyurethane foam forms hydrazoic acid, carbon dioxide and water. Take a look at the chemical reaction below:
6C27H36N2O10 + 185O2 🡪 162CO2 + 106H2O + 4HN3
Production of Polyurethanes
These polymers are fabricated by blending two or more than two liquid streams. The stream of polyol includes surfactants, catalysts, blowing agents, and others. The whole mixture is called ‘resin blend’ or ‘resin’. Additives of resin blend may consist of crosslinkers, chain extenders, surfactants, blowing agents, flame retardants, fillers and pigments. Polyurethanes can be formed in various hardness and densities by making variations in isocyanates, additives or polyols.
Applications of Polyurethane Foam
There are multiple polyurethane uses within which three-quarters of the entire global consumption are in the form of polyurethane foam.
Both flexible and rigid kinds of foams are available in markets. The foams are placed at the back of other materials like the flexible ones are placed behind the upholstery fabrics in domestic and commercial furniture.
Flexible foams are created by blending diisocyanates, polyols, auxiliary blowing agents, catalysts and other additives and then allowing the foam to grow freely. Besides furniture, they are used to make carpet cushions, automotive seat cushions, mattress padding, etc.
On the other hand, the rigid foams are placed between plastic sheets, metals, freezers and refrigerators.
Use of polyurethanes is increasing in the garments sector as well. For example, it is used in lining the brasserie cups. Another use of polyurethane foam is for making various bathroom and kitchen sponges.
Some other applications of polyurethane foam are as follows:
Highly resilient flexible foam seating.
Rigid foam for insulation panels.
Microcellular foam gaskets and seals.
Durable elastomeric tires and wheels.
Automotive suspension rubber bushings.
Carpet underlay.
Note: Flexible polyurethane foam is a recyclable item
Safety Measures and Health
Polyurethane polymers which are fully reacted are chemically inert. The Occupational Safety and Health Administration (OSHA) or American Conference of Governmental Industrial Hygienists (ACGIH) has not established any exposure limits of the polymer; OSHA has also not regulated for carcinogenicity as well.
Polyurethanes are combustible solids and can ignite when exposed to open flame. When decomposing in a fire, it can emit considerable amounts of hydrogen cyanide, carbon monoxide, nitrogen oxides, isocyanates and other toxic products. As the material is flammable, it must be treated with flame retardants (specifically for furniture), because all of them are harmful.
Did You Know?
In California, a Technical Bulletin 117 2013 was issued that permitted maximum polyurethane foam to succeed flammability tests without using flame retardants.
However, the Green Science Policy Institute said that it does not ban their use even though the new standard can be met without flame retardants. Consumers can look for TB117-2013 tag on furniture, and verify with sellers to ensure the products do not contain flame retardants if they wish to reduce household exposure to the same.
Isocyanates and liquid resin blends can contain regulated or hazardous components. The former is known to cause skin and respiratory allergic reactions. Moreover, glycols, phosphate and amines available in spray polyurethane foam are also risky.
Biodegradation and Hydrolysis
There is a possibility of polyurethanes to crumble because of hydrolysis. An example of such problem is when shoes are left in a closet, and it reacts with air moisture.
Pestalotiopsis is an Ecuadorian fungus whose two species can biodegrade polyurethane in aerobic and anaerobic environments, found at the base of landfills. There are also reports of degradation of polyurethane objects in museums. Polyester polyurethanes are more prone to biodegrade by fungus than the polyether type polyurethanes.
Do It Yourself
Choose the correct option concerning the following sentences -
i) Polyurethane is chemically inert.
ii) Polyurethane polymers do not support combustion.
a) true and false b) both are true c) both are false d) false and true
Polyurethane foam is an essential polymer which has multiple uses in daily life. But you must also keep in mind that it is a chemical substance that supports combustion and can emit toxic gases. If you wish to know more related to other topics of Chemistry, download the Vedantu app today and get access to study materials and online tutorials.
FAQs on Polyurethane Foam
1. What is the chemical formula of polyurethane foam?
Polyurethane foam chemical formula is C27H36N2O10.
2. What is the use of polyurethane sealant?
These sealants dry quickly and moisture-curing, which are utilised in several industries like construction, automotive and building industry. They are primarily used to seal joints in floors and walls and works effectively on concrete. Moreover, it can also bond and seal fibreglass panels.
3. Which one is better among polyurethane and silicon?
It cannot be determined which one among silicon and polyurethane works better. Silicon works best as a sealant on tiles, metals and glass. In contrast, polyurethane is suitable for natural objects like wood. But silicon fails to work on wood.
4. What are the drawbacks of polyurethane?
There are quite a few disadvantages of polyurethane such as short life, health-related issues, environmental problems, and although not noticeable, they have an odour and releases fume.
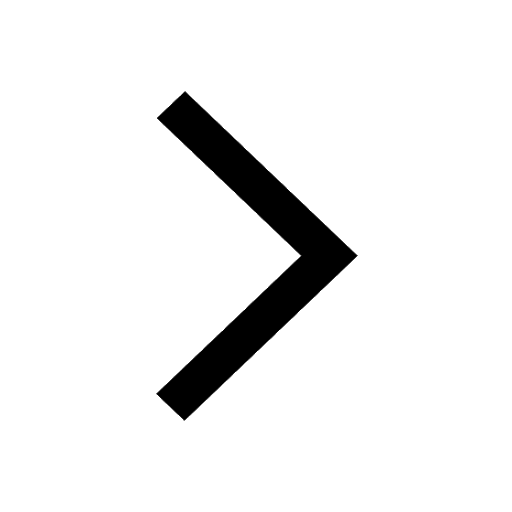
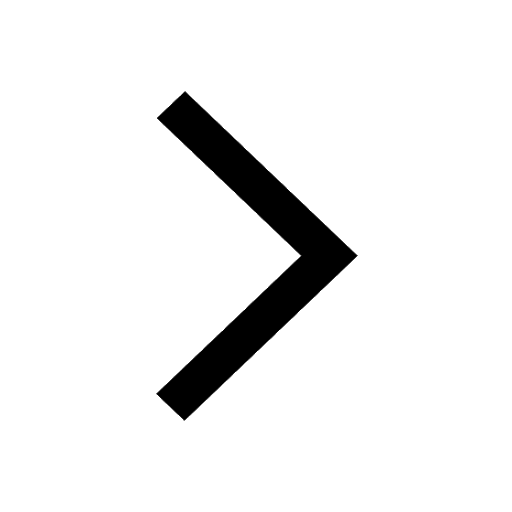
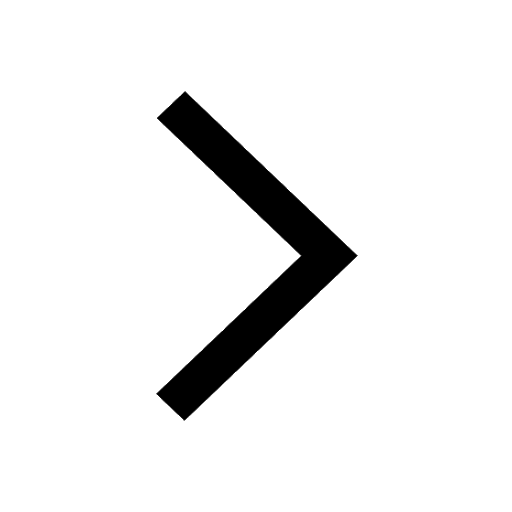
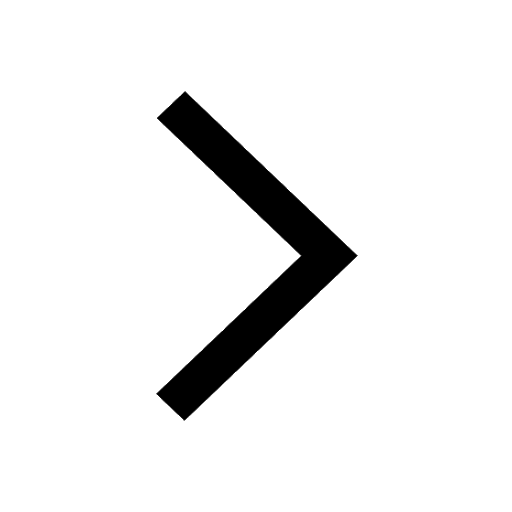
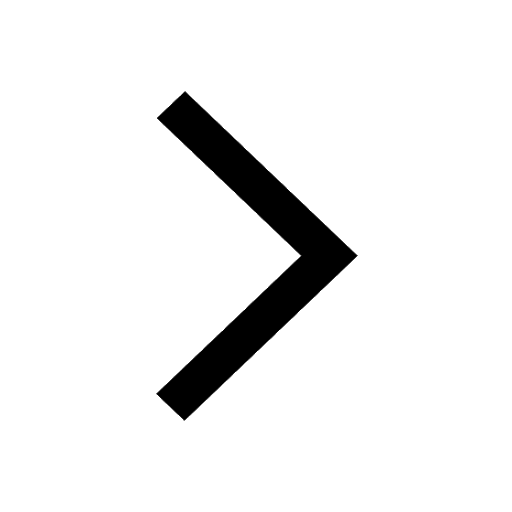
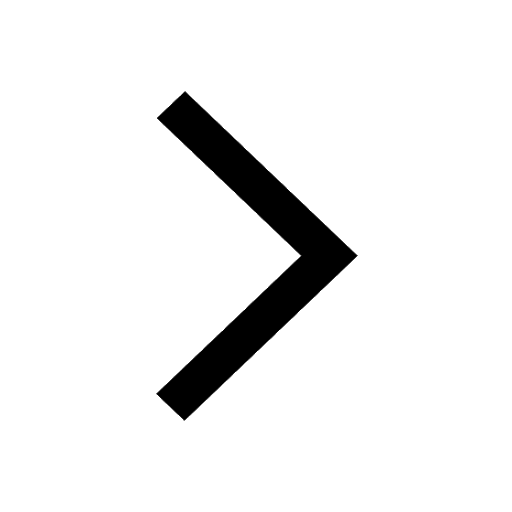