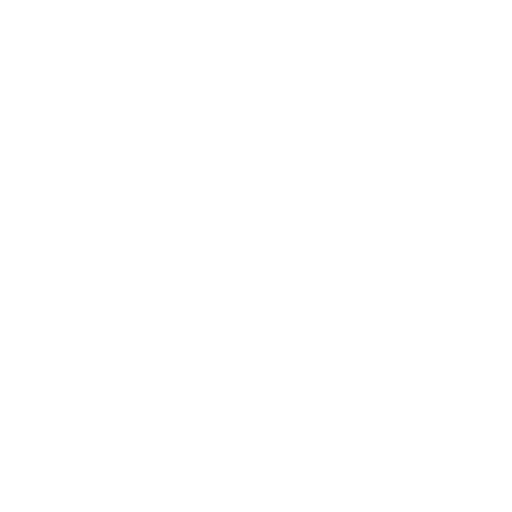

What are Stress and Strain?
Some of the items you might have noticed can be easily stretched, for example, like a rubber band. But can you stretch an iron rod? It is impossible, right? On this page, we will learn about the properties of solids in greater detail also, how quantities like stress will help us to understand the strength of solids.
Stress and Strain are the two terms in Physics that describe the forces causing the deformation of objects. Deformation is known as the change of the shape of an object by applications of force. The object experiences it due to external forces; for example, the forces might be like squeezing, squashing, twisting, shearing, ripping, or pulling the objects apart.
Types of Strain
A person's body can be stressed in one of two ways, depending on how much stress is applied:
Tensile Strain: Tensile strain is defined as a change in the length (or area) of a body caused by tensile tension.
Compressive Strain: The change in length (or area) of a body caused by compressive strain is known as compressive strain.
Use of Stress-Strain Graph
The stress-strain diagram is a graphical representation of the material's strength and elasticity. The stress-strain diagram can also be used to study the behaviour of the materials, which simplifies the application of these materials.
(Image will be uploaded soon)
Relationship Between Stress and Strain
Stress and strain have a straight proportional relationship up to an elastic limit. The relationship between stress and strain is explained by Hooke's law. Hooke's law states that the strain in a solid is proportional to the applied stress, which must be within the solid's elastic limit.
Yield Point in Stress-Strain Graph
The yield point of a material is the point at which it begins to distort plastically. Permanent plastic deformation happens after the yield point is passed.
How to Create a Stress-Strain Curve?
The stress-strain curve is created by progressively adding load to a test coupon and monitoring the deformation, which allows the stress and strain to be calculated.
Hooke’s Law
When English scientist Robert Hooke was studying springs and elasticity in the 19th century, he observed that numerous materials had a similar feature when the stress-strain connection was analysed. Hooke's Law defined a linear zone in which the force required to stretch material was proportionate to the extension of the material.
Define Stress and Strain
The force applied per unit area in mechanics is known as stress. The following formula represents it
Σ =F/A
where,
σ is stress applied
F is force applied
A is the area of force applied
Stress is measured by unit N/m2
The ratio of internal force F, produced when a substance is deformed, to the area A where force is applied is known as stress. At equilibrium, the internal force is equal to the magnitude of the externally applied force.
The newton per square meter (Nm2) is the SI unit for stress. Dyne-cm2 is the CGS unit in which stress is measured. ML-1T-2 is the dimensional formula for stress.
What is Strain?
Strain is the ratio of the amount of deformation experienced by the body in the direction of force applied to the initial sizes of the body. The relation of deformation in terms of the length of the solid is given below
ϵ=δlL
where,
ϵ is strain due to stress applied
δl is changed in length
L is the original length of the material.
Strain is the ratio for change of shape or size to the original shape or size. It is expressed in number as it doesn't have any dimensions. Since strain defines the relative change in shape and it is a dimensionless quantity. A body can experience two types of strain depending upon the stress application.
Stress-Strain Curve Explanation
The material's stress-strain curve represents the relationship between stress and strain for materials. The strain values are plotted on the curve corresponding to the stress incurred by different loads on the object.
Explaining Stress-Strain Graph
The stress-strain diagram has different points or regions as follows:
Proportional limit
Elastic limit
Yield point
Ultimate stress point
Fracture or breaking point
(Image will be uploaded soon)
(i) Proportional Limit
The region in the stress-strain curve that observes Hooke's Law is known as the proportional limit. According to this limit, the ratio of stress and strain provides us with the proportionality constant known as young's modulus. In the graph point, OA is known as the proportional limit.
(ii) Elastic Limit
Elastic limit is the maximum stress that a substance can endure before permanently being deformed. When the load acting on the object is completely removed and the material returns to its original position, that point is known as the object's elastic limit.
(iii) Yield Point
The point at which the material starts showing to deform plastically is known as the yield point of the material. Once the yield point of an object is crossed, plastic deformation occurs. There are two types of yield points (i) upper yield point (ii) lower yield point.
(iv) Ultimate Stress Point
The point at which a material endures maximum stress before failure is known as the Ultimate Stress point. After this point, the material will break.
(v) Fracture or Breaking Point
In the stress-strain curve, the point at which the failure of the material takes place is known as the breaking point of the material.
FAQs on Stress and Strain
1. What are the Types of Stress and Strain?
The different types of stress and strain are as follows:
Normal Stress: The restoring force per unit area perpendicular to the body surface is known as the normal stress. It is differentiated into two types: tensile and compressive stress.
Tangential Stress: It is called tangential stress when the elastic restoring force acts parallel to the surface area.
Types of Strain
Longitudinal Strain: The strain produced on the body due to the deforming force, which leads to change in only the length of the object is known as longitudinal or the tensile strain.
Volumetric Strain: This is the strain produced on the body due to the deforming force, which leads to only the change in volume of the object.
Shear Strain: Due to the tangential stress, an angle tilt is caused in the body; this is known as shear strain.
2. What is the relationship between Stress and Strain?
Hooke's law expresses the relationship between stress and strain; it states that the strain in an object is proportionate to the stress applied within the range of the elastic limit of that object.
Hooke's Law
The 19th century English scientist Robert Hooke noticed while experimenting with springs and elasticity of the materials, they exhibited a similar property when the stress-strain relationship was studied. According to Hooke's law, the linear region where the force required to stretch the material was proportionate to the extension of the material.
Mathematically, Hooke's law is commonly expressed as:
F = – k.x
Where,
F is the force
x is the extension length
Negative sign indicates that the force is acting in the opposite direction to the motion of a body.
k is the constant of proportionality known as spring constant in N/m
Point A shown in the graph is the proportional limit, which exhibits the proportional relationship between stress and strain in many of the materials.
Point B is known as the elastic limit, which is beyond the proportional limit, where an object returns to its original form when the applied stress is reversed, or the external force is removed. The proportional limit and elastic limit for many of the materials is the same or equal.
Point C in the graph is known as the yield point, where the strain increases faster than stress, and the material experiences some amount of permanent deformation.
The stress causes a specified amount of permanent strain at the offset yield strength (point B).
D denotes the value of the ultimate tensile strength of the material that has been reached. It denotes the maximum stress that can be applied to the material before its failure occurs.
3. How do bones get fractured?
Bones do not shatter as a result of tension or compression. Rather, they usually break owing to bending or sideways stress, resulting in bone shearing or snapping. The way bones behave in tension and compression is significant because it influences how much weight they can support. Weight-bearing structures, such as columns in buildings and trees, are classified as bones. Weight-bearing structures have unique characteristics, such as steel-reinforcing rods in building columns and fibrous trees and bones. Distinct bones serve varying structural purposes and are subject to different forces in different regions of the body. Thus, the top of the femur's bone is arranged in thin sheets separated by marrow, although the bones in other locations can be cylindrical and filled with marrow or solid.
4. Explain the different regions in the stress-strain graph?
The different regions in the stress-strain graph are:
(i) Proportional Restriction
Hooke's Law is obeyed in this section of the stress-strain curve. The stress-strain ratio offers us a proportionality constant called Young's modulus in this limit. The proportional limit is shown by the point OA in the graph.
(ii) Elastic Boundary
When the load acting on the material is removed, the material returns to its previous position up to this point in the graph. The material does not return to its original position beyond this point, and a plastic deformation appears.
(iii) Yield Point
The yield point of a material is defined as the point at which it begins to distort plastically. Permanent plastic deformation happens after the yield point is passed. The yield points are In the upper yield point and (ii) lower yield point.
(iv) The Highest Stress Level
It is a reference point for the maximum stress that a material can withstand before failing. Failure occurs after this stage.
(v) Breaking Point or Fracture
It is the point on the stress-strain curve where the material fails.
5. Give a biological example of Hooke’s law?
Tendons are another biological example of Hooke's law. When a force is applied, the tendon must stretch easily initially, but then provide a considerably stronger restorative force for a greater strain. Some tendons have a high collagen content, resulting in little strain or length change; others, such as support tendons, can alter the length by up to 10%. As the slope of the line varies in different places, this stress-strain curve is nonlinear. The fibres in the tendon begin to align in the direction of the stress in the toe area of the stretch, which is known as uncrimping. The fibrils will be stretched in the linear zone, and individual fibres will begin to break in the failure region. For free study materials, go to the Vedantu app and website.
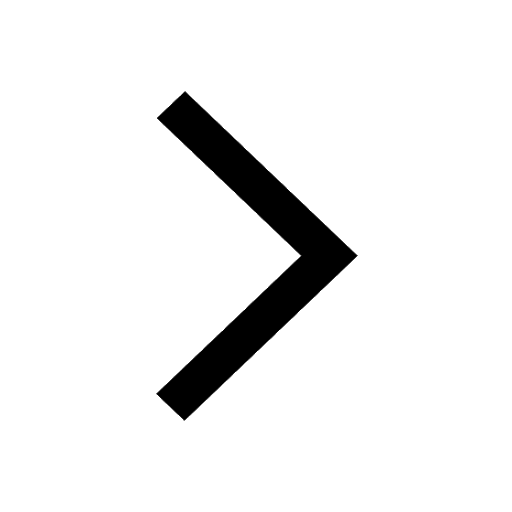
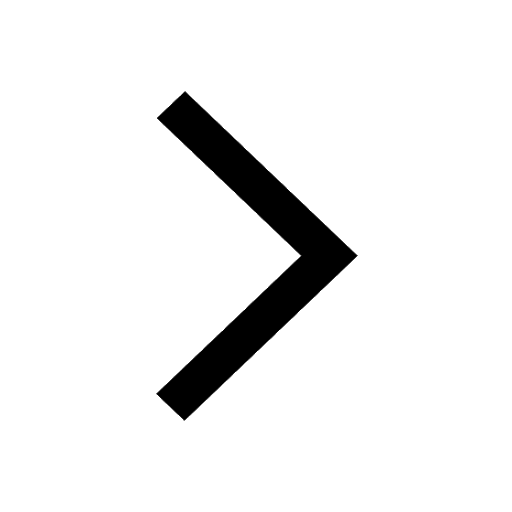
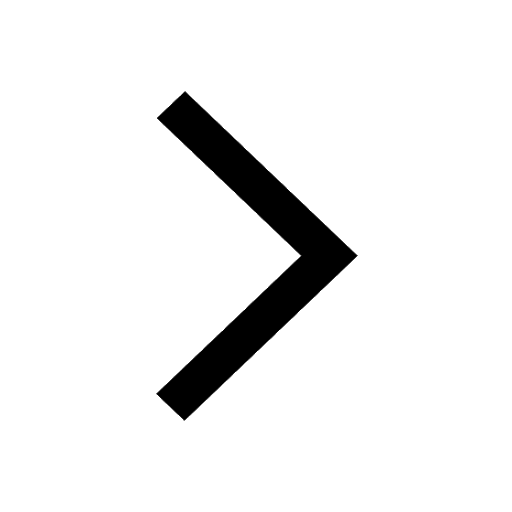
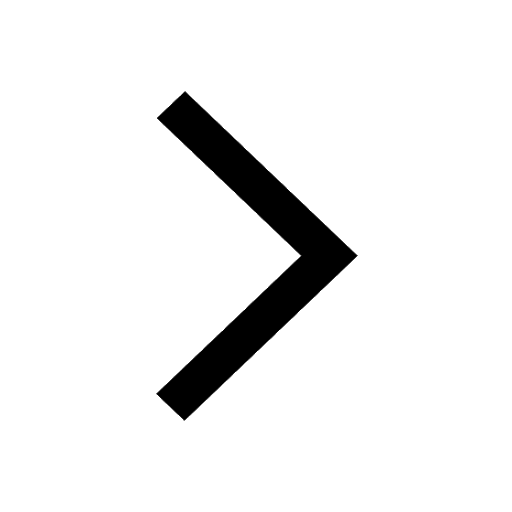
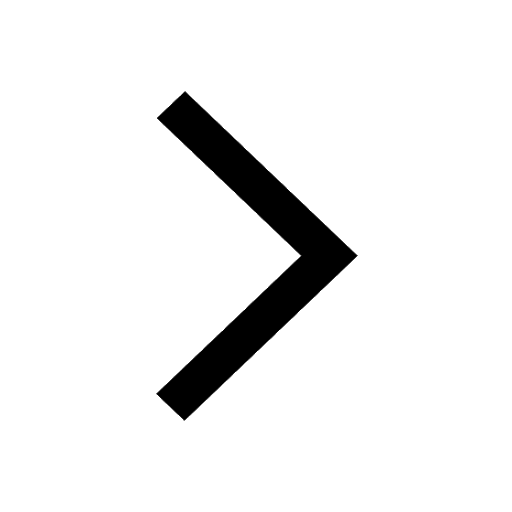
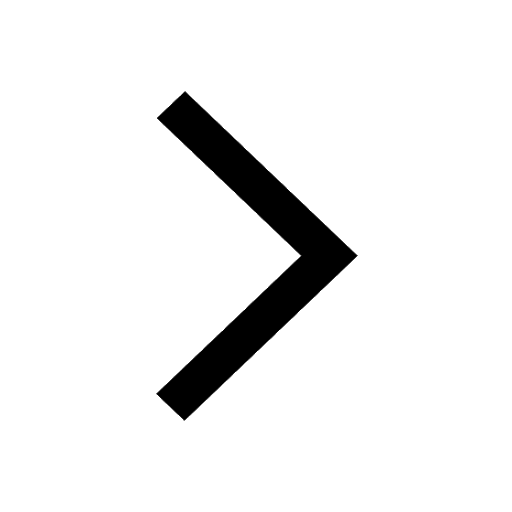