An Introduction: What is Iron Loss?
FAQs on Difference Between Iron Loss and Copper Loss
1. What is iron loss and copper loss?
The quantity of weight lost over a specific time period is known as Iron Loss. Flux density changes in the transformer core are the reason for the iron loss. Mechanical energy is first converted from electrical energy. Magnetic energy travels through the magnetic core. Energy is lost during the core's demagnetization and magnetization. Copper Loss is the amount of volume lost over a specific time frame. The transformer winding is the source of the copper loss. A transformer's primary and secondary windings have a specific resistance. The wire diameter and number of turns affect the winding resistance. The current flowing in the primary and secondary windings is what causes the heat loss in the winding. The heat loss in the coil is known as copper loss.
2. What are the factors affecting eddy current losses in the transformer?
Eddy current losses are a consequence of Farady's law, which states that "Any change in the environment of a coil of wire will cause a voltage to be induced in the coil, regardless of how the magnetic change is produced." Consequently, a voltage, or EMF, is created in the coils when a motor core rotates in a magnetic field. Eddy currents, which are circulating currents that are caused by this produced EMF, flow as a result. Eddy current loss is the name for the power loss brought on by these currents. Factors affecting eddy current losses are attributed to maximum flux density in the core, supply frequency, thickness of the lamination, volume of the core material and resistivity of the core.
3. What are the ways of reducing hysteresis loss inside the transformer?
Some ways through which hysteresis loss can be mitigated inside a transformer include selection of the specific core material which has less magnetic flux density and operating the transformer at a rated voltage and frequency. Also using alloys like mumetal or silicon steel for core material can greatly reduce hysteresis loss.
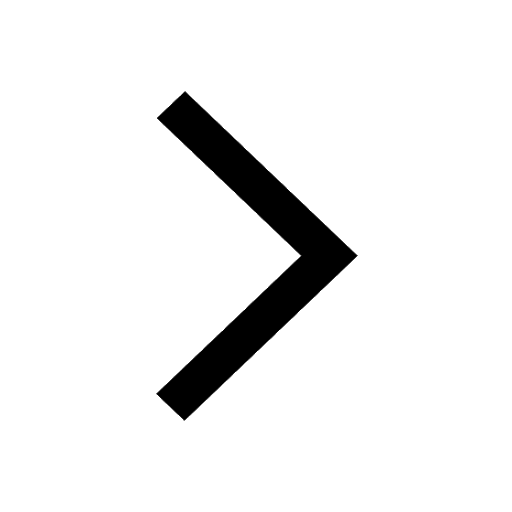
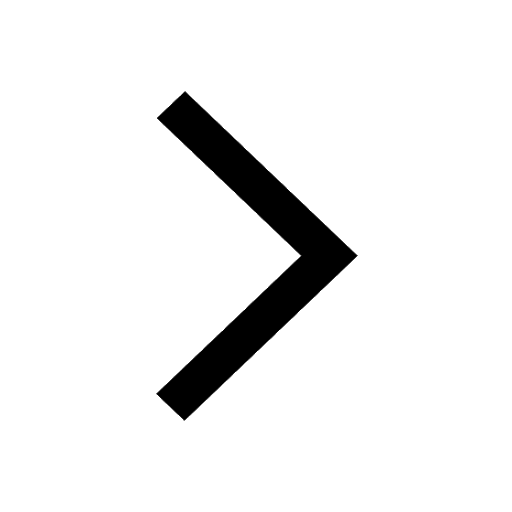
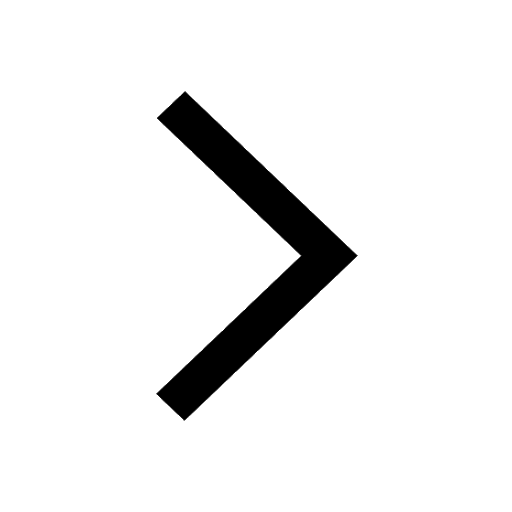
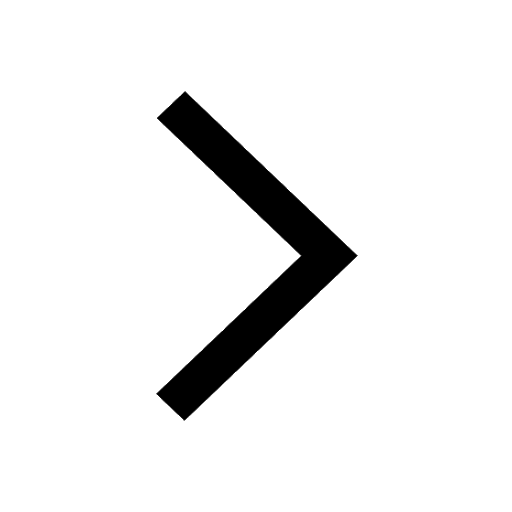
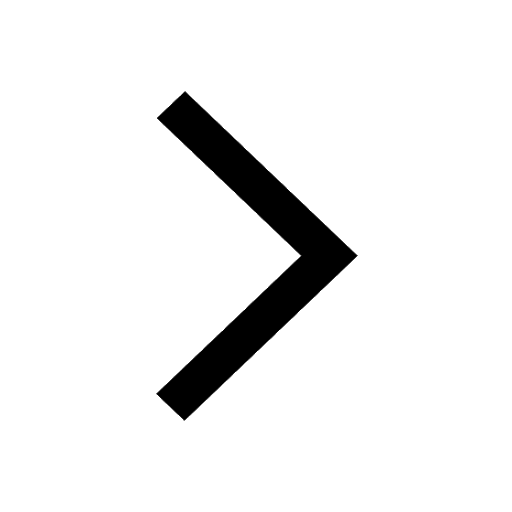
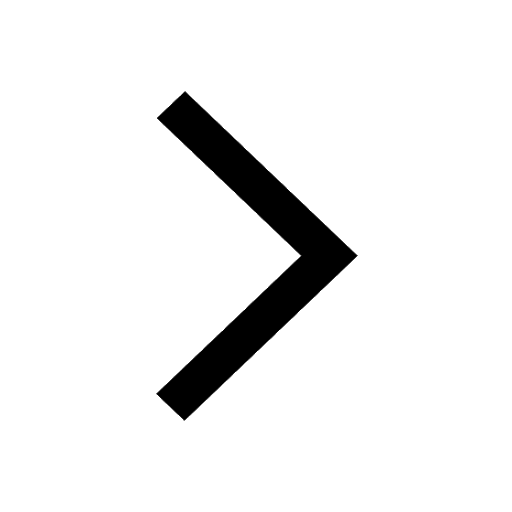
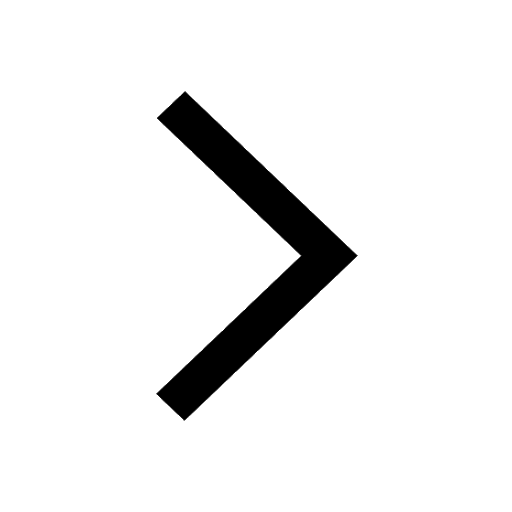
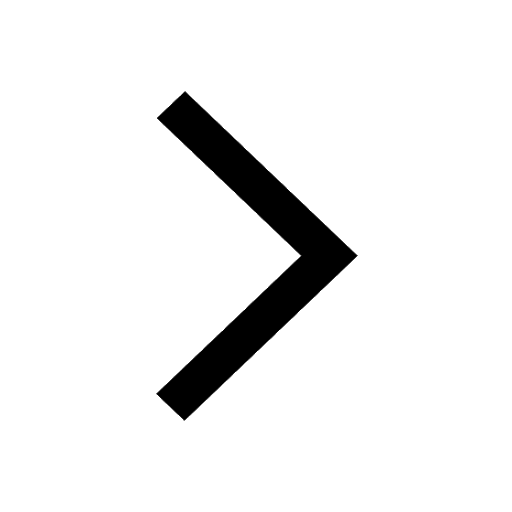
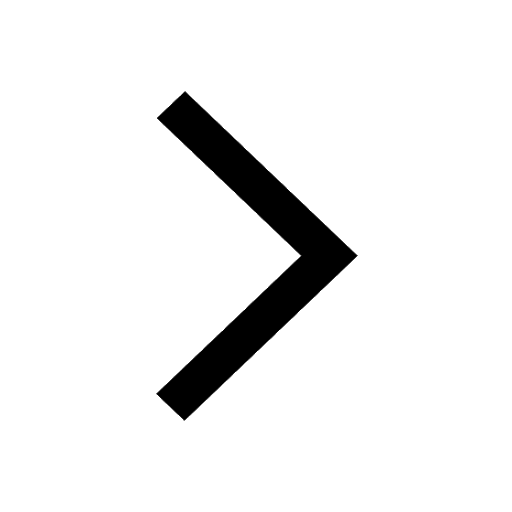
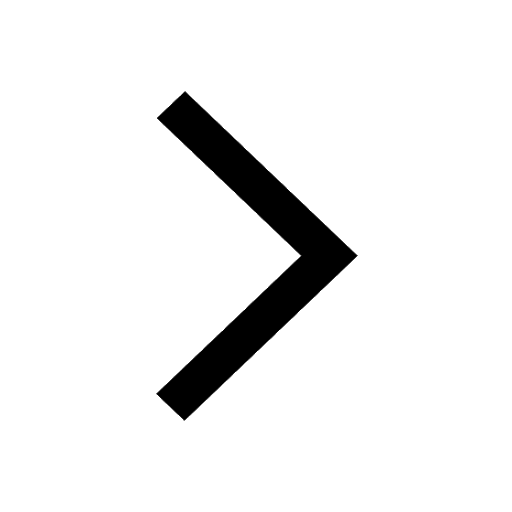
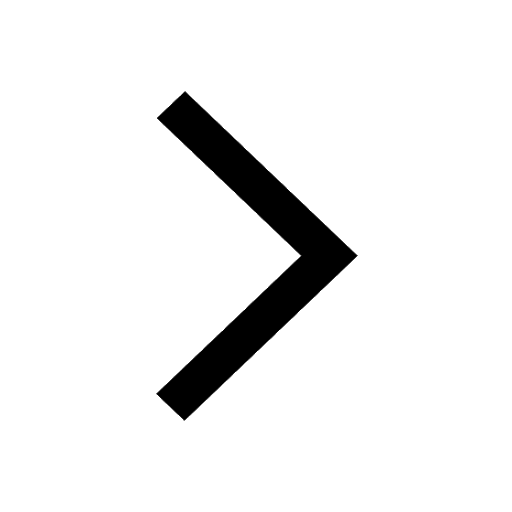
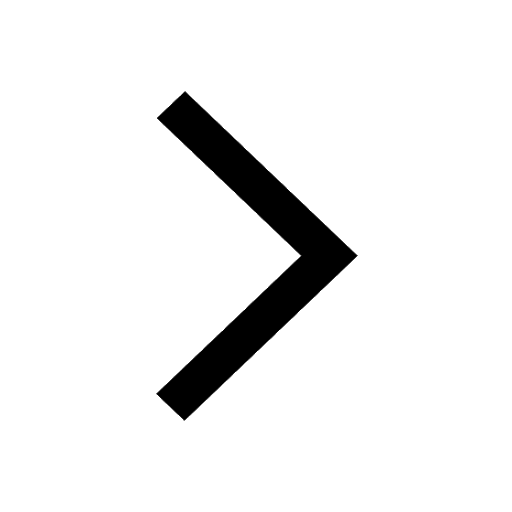
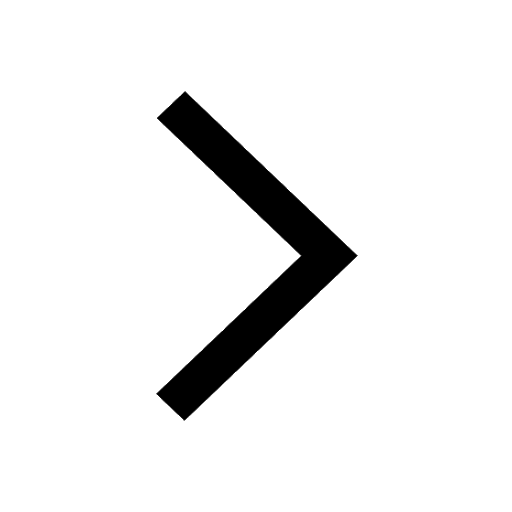
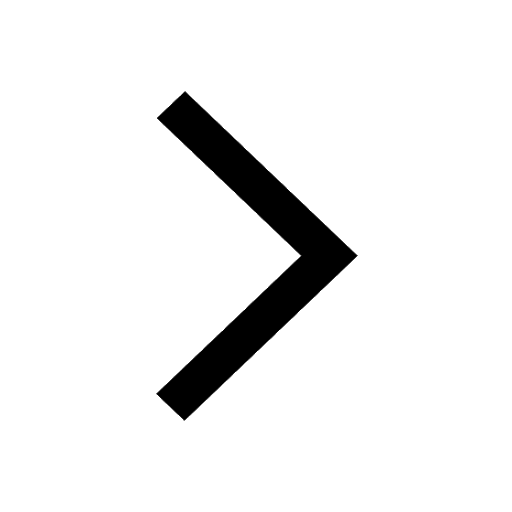
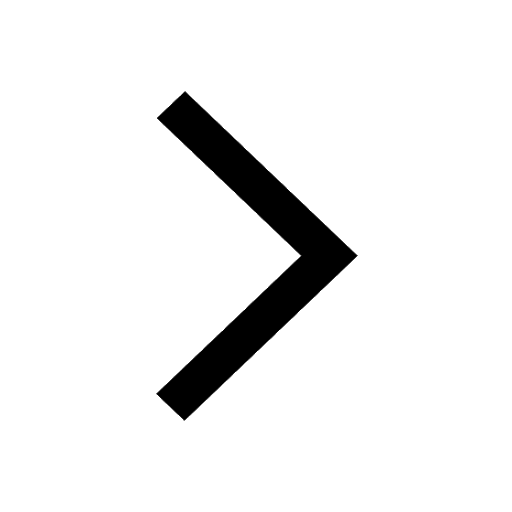
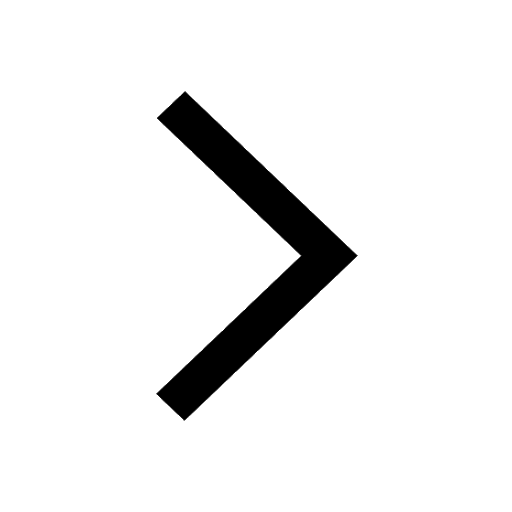
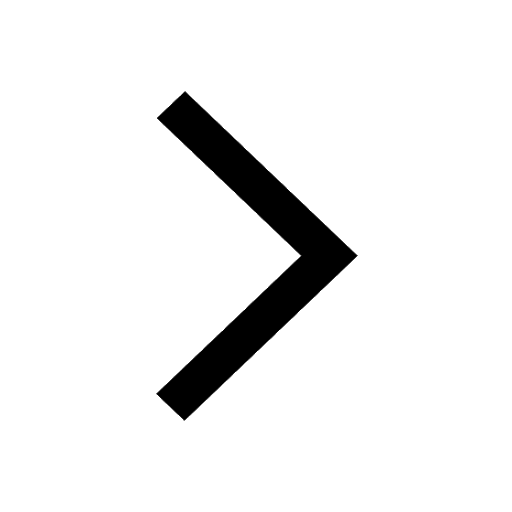
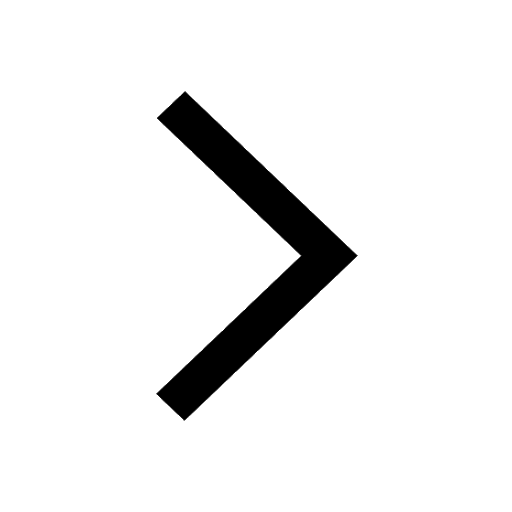
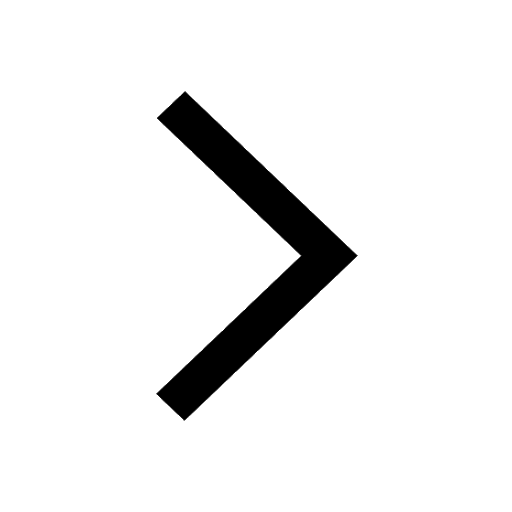
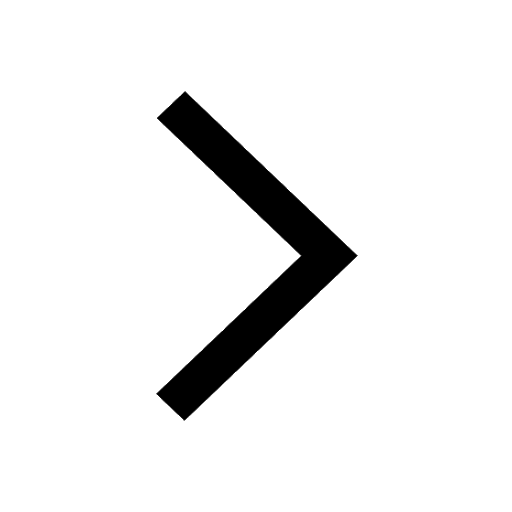
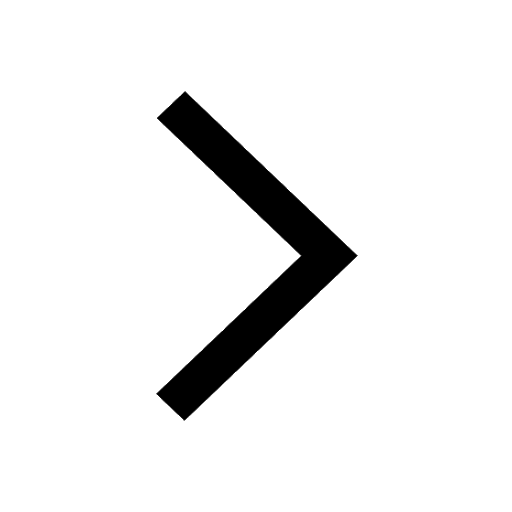