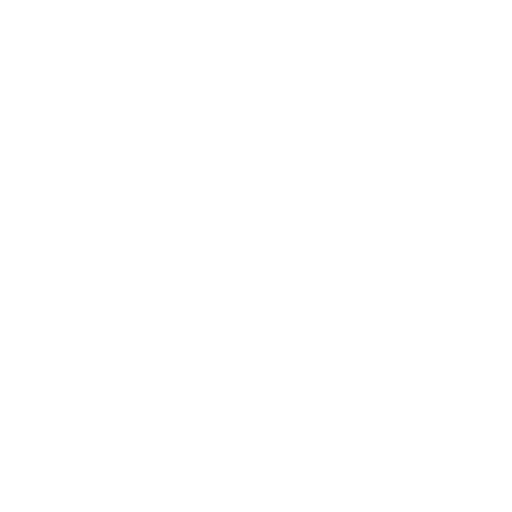

Metallurgy Definition
A huge variety of metals are available in the earth’s crust. The naturally occurring metallic compounds mixed with sand, soil, and rocks having a definite chemical composition are called minerals. A metallic compound having a relatively high concentration of metal and can be used to extract particular elements in convenient and economical manner called ore.
Metallurgy definition can be given as the branch of chemistry that deals with the extraction of metal in their pure form from their ore.
(Image will be uploaded soon)
Metallurgy Process
Metallurgy process involves the refining of metals and the production of alloys of metals. The impurities present in the ore, which has to be separated in order to obtain desired metal from its ore during the process of extraction, are called gangue. A substance added in the furnace to remove the gangue present in the ore is called flux. The key steps involved in the metallurgy of metals are:
Crushing and grinding of the ore
Concentration of the ore
Extraction of the crude metal
Purification of the metal
Principles of Metallurgy
The processes involved in metallurgy are as follows:
Crushing and Grinding:
The primary process involved in the metallurgy of metals is pulverization, which involves the crushing of ores into fine powder in a crusher.
The Concentration of Ores:
The ores extracted from the earth's crust contains a large number of unwanted impurities called gangue mixed with them, such as quartz, silicates, sand, feldspar, mica, etc. The removal of these unwanted impurities from the ore is called dressing. The dressing of ore is also called concentration of the ore because it gradually increases the percentage of metal. In metallurgy, the concentration of ore is achieved using the following methods.
Physical Methods:
Hand-picking is a traditional method of concentrating ore by merely picking it by hand. In this method, the gangue or adhering rocky materials are separated from the ore with the help of a hammer.
Hydraulic Method:
Hydraulic method or gravity separation or Levigation: This method is a gravity separation method of metallurgy, which is based on the differences in the gravity of the ore and gangue particles present in the ore. This method is frequently used when the ore particles are more massive than the rocky gangue particles. It is used to concentrate heavy oxide ores of lead, tin, iron, etc.
In this method, the powder ore is agitated with jets of water in a hydraulic classifier (or Wilfley table) that makes the more massive ore particle settle down at the bottom and washes away the lighter impurities. The oxides and carbonate ores are concentrated by using this method. This method is also called levigation and is used for gold, chromium, iron, etc.
Magnetic separation:
This method of metallurgy is used when either the ore or the impurities are magnetic in nature. For example, magnetic ores like pyrolusite (MnO₂) and chromite (FeO.Cr₂O₃) have a difference in the magnetic properties of the ore and gangue particles. In this method, the ground ore is carried on a conveyor belt rotating around two wheels, which passes over a magnetic roller. The magnetic wheel attracts the magnetic particles and separates them from the non-magnetic particles of the mixture.
Froth floatation:
The crushed ore is mixed with a mixture of water, pine oil, detergent in a tank to separate sulphide ores. A current of compressed air passes through the pipe of a rotating agitator that produces froth. The presence of differences between the gangue particles and wetting properties of the ore helps to separate them. The pine oil wets and coats the sulphide ore particles which makes them rise up along with the lighter froth. The heavy water wets the gangue particles which sinks to the bottom of the tank. The froth containing the sulphide ore gets transferred to a different container where they are washed and dried.
Chemical Method
Leaching:
Leaching is a chemical method used for treating ores, which are soluble in a suitable solvent. In leaching, the powdered ore undergoes treatment with specific reagents, which dissolves the ore but not the unwanted impurities. The undissolved impurities are removed by filtration.
For example, Bauxite (Al₂O₃) is an ore of aluminum, which contains unwanted impurities ferric oxide, titanium oxide, and silica. The finely powdered ore of bauxite undergoes treatment with an aqueous solution of sodium hydroxide at about 1500 – 1700C. NaOH dissolves the alumina (Al₂O₃) present in the ore to form soluble meta aluminate, while the other oxides (Fe₂O₃, TiO₂, and SiO₂) remain insoluble and are removed by filtration.
Al₂O₃.2H₂O (s) + 2NaOH(aq) + 3H₂O (l) → 2NaAl(OH)₄(aq)
Sodium aluminate(Hydrated)
2NaAl(OH)₄(aq) + CO₂ (g) → Al₂O₃.xHO(s) + 2 NaHCO₃
The sodium silicate, which remains in the solution, is precipitated out as hydrated alumina and separated by the filtration method. It is then dried by heating to 1470 K, which gives pure alumina.
Al₂O₃.xH₂O (s) → Al₂O₃ (s) + xH₂O
This process is called Baeyer's process.
Roasting: The process of heating a concentrated ore strongly in the presence of excess oxygen at a temperature below the melting point of the metal is called roasting. This process is commonly used for sulfide ores.
2ZnS + 3O₂ → 2ZnO + 2SO₂
During Roasting:
Sulphides are partially converted to oxides
Volatile impurities are removed
The free elemental forms of sulphur, arsenic, and antimony are removed as SO₂, As₂O₃, and Sb₂O₃, respectively.
Calcination: The process of heating a concentrated ore in the absence of air to melt the ores is called calcination. This process is done for carbonate ores.
ZnCO₃ → ZnO + CO₂
CaCO₃ → CaO + CO₂
Al₂O₃.2H₂O → Al₂O₃ + 2H₂O
During calcination:
Moisture is removed
Mass becomes porous
Volatile impurities are removed
Carbonate ores decompose to oxides
Water from hydrated oxide ore is removed
Roasting and calcination are carried out in different types of furnaces; the most commonly used is the reverberatory furnace. In the roasting process, the air holes are always kept open while in the calcination process, the air holes are entirely or partially closed.
FAQs on Metallurgy
1.What is metallurgy?
Metallurgy is a section of materials science and engineering that looks into the physical and chemical properties of intermetallic compounds, metallic elements and alloy mixes. Metallurgy refers to both the science and the technology of metals, i.e., how science is applied to the manufacturing of metals and the engineering of metal components utilised in consumer and industrial products. Metallurgy is different compared to minecrafting as a craft. Metalworking is dependent on metallurgy in the same way that medicine is dependent on medical science for technological growth.
Chemical metallurgy and physical metallurgy are two large divisions within the discipline of metallurgy. Chemical metallurgy deals with oxidation and metal reduction, and also metal chemical properties. Metal extraction, mineral processing, electrochemistry, thermodynamics, and chemical deterioration are all subjects of discussion in chemical metallurgy. Physical metallurgy, on the other hand, is concerned with metals' mechanical properties, physical qualities, and physical performance. Crystallography, material characterization, mechanical metallurgy, phase transitions, and failure mechanisms are all researched in physical metallurgy. Kindly click here to learn more.
2.Write an note on metal and its alloys
Aluminium, chromium, copper, iron, magnesium, nickel, titanium, zinc, and silicon are all common engineering metals. With the exception of silicon, these metals are most commonly used in alloys.
The iron-carbon alloy system, which includes steels and cast irons, has received a lot of attention. Plain carbon steels (those with practically only carbon as an alloying element) are utilised in low-cost, high-strength applications where weight and corrosion aren't a big consideration. The iron-carbon system also includes cast irons, such as ductile iron. Non-magnetic applications such as directional drilling use iron-manganese-chromium alloys (Hadfield-type steels).
Where corrosion resistance is critical, stainless steel, particularly Austenitic stainless steels, galvanised steel, nickel alloys, titanium alloys, and occasionally copper alloys are utilised.
When a lightweight, sturdy item is required, such as in automotive and aerospace applications, aluminium and magnesium alloys are typically utilised. Copper-nickel alloys (such as Monel) are employed in non-magnetic applications and in highly corrosive conditions.
High-temperature applications such as gas turbines, turbochargers, pressure vessels, and heat exchangers use nickel-based superalloys like Inconel. Single crystal alloys are used to reduce creep at extremely high temperatures. Metal-oxide-silicon transistors (MOS) and integrated circuits require high purity single crystal silicon in modern electronics.
3.How is metallurgy used for production?
Metallurgy deals with the fabrication of metallic components for utilisation in engineering or consumer products in production engineering. This includes alloy manufacturing, shape, heat treatment, and product surface treatment.
Using the Rockwell, Vickers, and Brinell hardness scales to determine the metal's hardness is a standard practice that aids in better understanding the metal's elasticity and plasticity for various applications and manufacturing processes.
The metallurgist's job is to strike a balance between material attributes like cost, weight, strength, toughness, hardness, corrosion resistance, fatigue resistance, and temperature extreme performance. The operational environment must be carefully considered in order to attain this purpose.
Most ferrous metals and some non-ferrous alloys corrode quickly in a saltwater environment. Metals exposed to cold or cryogenic settings may shift from ductile to brittle, losing their hardness and becoming more brittle and crack-prone. Metal fatigue can occur when metals are subjected to cyclic loading on a regular basis. Metals that are subjected to constant tension at high temperatures can creep.
4.What is extractive metallurgy?
The method of extracting valuable metals from an ore and refining the retrieved raw metals into a purer form is known as extractive metallurgy. The ore must be reduced physically, chemically, or electrolytically to convert a metal oxide or sulphide to a purer metal. Feed, concentrate (metal oxide/sulphide), and tailings are the three basic streams that extractive metallurgists are interested in (waste).
After mining, big chunks of ore feed are crushed or ground into minute particles, with each particle containing either mostly valuable or mostly waste material. The needed metal can be extracted from waste products by concentrating the valuable particles in a condition that allows for separation.
If the ore body and physical environment are suited to leaching, mining may not be necessary. Minerals in an ore body are dissolved by leaching, resulting in an enriched solution. To extract valuable metals, the solution is collected and treated. Ore bodies often have multiple precious metals.
Tailings from a previous process can be fed into a new process to extract a secondary product from the ore. Furthermore, a concentration may contain multiple precious metals. The valuable metals would next be separated into individual elements from the concentration.
5.What is the history of metallurgy?
Gold, which can be obtained free or "native," thought to be the oldest metal used by humans. Small amounts of natural gold have been discovered in caverns in Spain going back to the late Paleolithic period, roughly 40,000 BC. Silver, copper, tin, and meteoric iron are also found in native form, allowing early cultures to do some metalworking. Certain metals, such as tin, lead, and, at a higher temperature, copper, can be extracted from their ores by simply smelting the rocks in a fire or blast furnace. The first evidence of extractive metallurgy was discovered at archaeological sites in Majdanpek, Jarmovac in Priboj, and Plonik in modern-day Serbia, dating from the 5th and 6th millennia BC. The first evidence of copper smelting has been discovered at the Belovode site near Plocnik. The Vedantu app and website should be visited if you want your hands on free study materials.
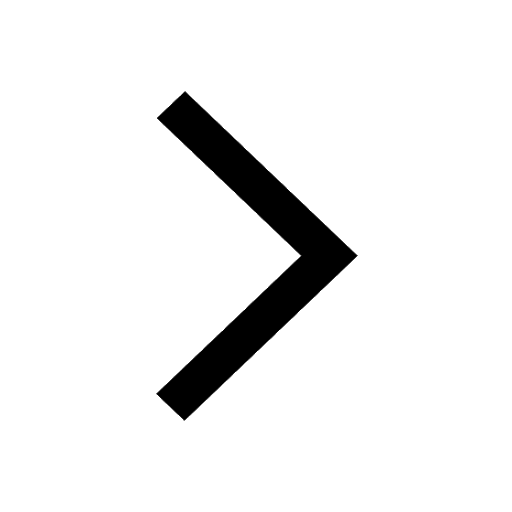
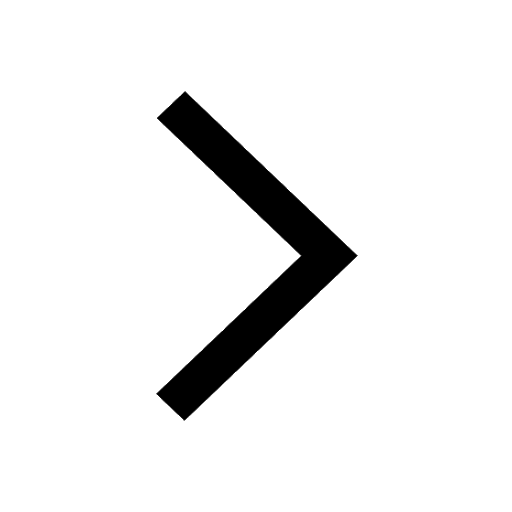
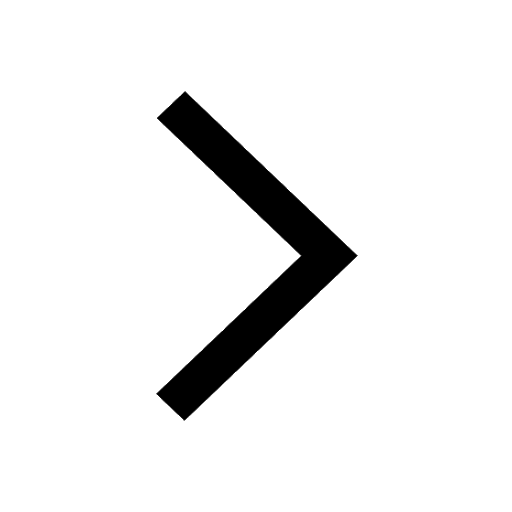
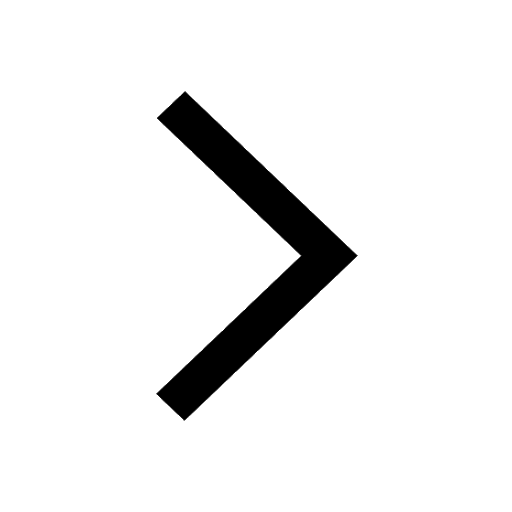
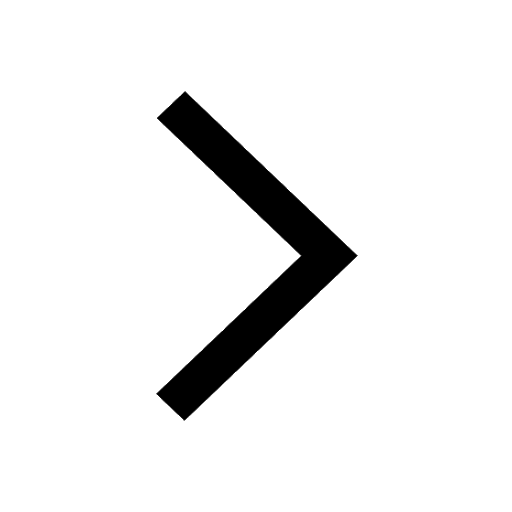
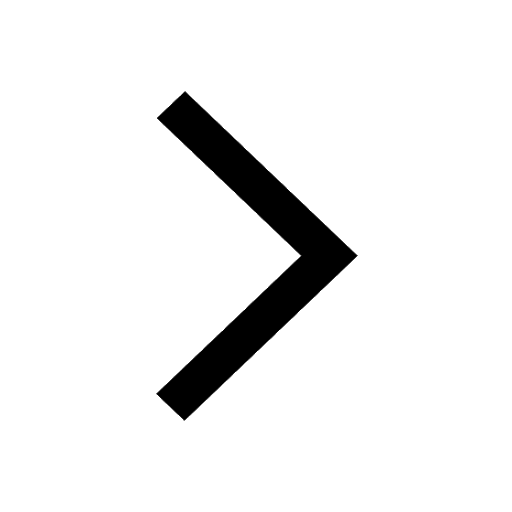