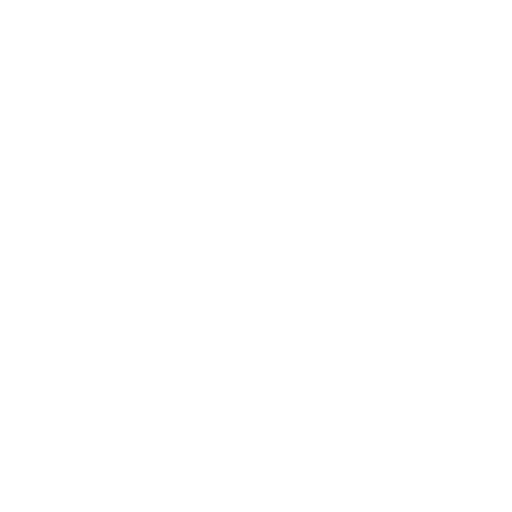

Vedantu’s Working of Boiler Concept Explanation Free PDF
Vedantu is the leader in the field of Digital education in India and is consistently pursuing its goal of bringing quality study materials for all students of India that is readily accessible to them. Continuing our mission of transforming the digital space in India, Write Ups and detailed explanation of topics have been provided to students so that students can find a one stop solution to all their academic woes.
What is a Boiler ?
The boiler is commonly defined as a closed vessel into which water is heated to the point it is converted into steam at the imperative pressure. The main function of the boiler is either to produce hot water or steam. The Hot water boiler heats water for the domestic or commercial purpose of heating and hot water supply, whereas Steam boilers generate steam to power turbines for power generation and other various industrial heating applications.
To understand the steam generation effects using a boiler, try thinking about the steam powering a turbine. When steam is made to flow through the turbine blades, the force turns the blades and accelerates the turbine.
Also, Steam has an enormous amount of energy as it consists of the energy given for raising the temperature of the water along with the latent heat of vaporization. So, it makes the turbine quite efficient and based on the fuel used to boil the water, very energy-efficient too. The Boilers work under pressure to heat any liquid types for external use by the combustion of fossil fuels or energy from the sun.
Parts and Accessories of a Boiler
The boiler parts are classified into two divisions, these are:
Boiler Mounting
They are the essential parts that define the boiler’s performance. The main components of boiler mounting include:
Pressure Gauge: The gauge type is used to measure the pressure inside the boiler, fitted at the boiler’s front.
Water Level Indicator: This is used to check the inside water level of a boiler, fitted in the front of the boiler having a glass tube and three cocks and
Stop Valve: We can control the flow of steam from the boiler to the steam pipe using this.
Safety Valve: The valve is fitted on the drum, which is used to prevent the boiler explosion due to high pressure, which blows off when the inside pressure exceeds the limit. There are always two of them present to ensure no explosion takes place in the boiler.
Blow Off Cock: It is used to blow off water and mud, and is used to empty the boiler. It is generally fitted at the bottom of the drum
Grate: It is the space in the furnace used for fuel-burning
Feed Check Valve: The valve is used as a Non-Return Valve, and is fitted on the drum slightly below the normal water level. It is useful to regulate the water supply.
These boiler accessories are responsible for boiler efficiency. The main components of the boiler include:
Super Heater: The heater is used to superheat the steam before it is passed in the turbine as saturated steam that causes corrosion
Feed Pump: This is to pump the water into the continuous boiler working. The Steam or electricity or turbine is used for the feed pump running
Air Preheater: It is also used to increase the boiler’s efficiency by preheating the air
Economizer: This component is used to increase the boiler’s efficiency as the flue gasses from the boiler is prepared to flow through the economizer before releasing it into the atmosphere
Working Principle of a Boiler
It is simple to understand how the boiler works. To understand it, let us have a look at it.
The boiler is a closed vessel, where the water is stored. Hot gasses are formed by burning fuel in the furnace. These glasses are made to come in contact with the water vessel, the point where the heat transfer takes place between the steam and water. Thus, the boiler’s basic principle is to convert water into steam with heat energy. There are various types of boilers available to use for different purposes.
Efficiency of Boiler
It is defined as the total percentage of heat exported by the outlet steam to the total supplied fuel.
Boiler Efficiency (%) = (Heat Exported by Outlet Steam) / (Heat Supplied by the Fuel) * 100
Classification of Boiler
Boiler’s classification is based on the following criteria:
According to the Relative Passage of Hot Gasses and Water
Fire-Tube Boiler: This is the one where the hot combustion gasses are surrounded by the water
Water-Tube Boiler: In this, the water flows via the tubes, surrounded by hot combustion gasses
According to the Arrangement of Water Circulation
Forced Circulation: The is the circulation that happens by pumping the water present inside the boiler
Natural Circulation: This circulation happens because of the density difference
According to the Usage
Locomotive: Used in the railway engines
Marine Boiler: Used in ships
Stationary Boiler: Used for power plants
Portable Boiler: These are used temporarily in sites and are movable
According to the Boiler’s Position
Inclined
Horizontal
According to the Pressure Generated by the Steam
Medium Pressure Boiler: The maximum pressure is of 20-80 bars and is used to generate power
Sub-Critical Boiler: If the boiler produces steam at a pressure less than the critical pressure it is called sub-critical
Low-Pressure Boiler: The maximum pressure is of 15-20 bar and is used for the purpose of heating
High-Pressure Boiler: This boiler has a maximum pressure of more than 80 bars
Supercritical Boiler: These are used to produce steam at a pressure greater than the critical pressure
According to Charge in the Furnace
Pulverized fuel
Supercharged fuel
FAQs on Working of Boiler
1. Mention the Applications of the Boiler?
Boiler applications are indispensable in many industries. Hot water boilers can be used for hot water supply (like bathing hot water) and heating. It is also used in hotels, urban heating systems, accommodation areas, office buildings, farms, and planting greenhouses.
Steam boilers can be used for cooling, heating, cleaning, humidification, and in production processes and also can be used for power generation. Steam boilers can be used in industries like feed, food processing, textile, paper, building materials, metal smelting, heating engineering, and many more.
The cogeneration boilers application is gradually increasing, and steam boilers are also used for generating power, and auxiliary machines like heat exchangers are used for heating purposes. Now, biomass cogeneration is a new trend.
Some Additional Applications of the Boiler Can Be Given as the Following
Refineries and distilleries
Thermal power plants
Sugar plants
FMCG (Fast Moving consumer goods)
Health care industries
Pharmaceutical industries
2. What is the Difference Between an AFBC and the CFBC boiler?
Boilers are just a way of burning fuel or any liquids.
For example, a Travelling Grate Stoker can burn the fuel in Static Mode such that the fuel rests on the grate. Besides, the Pulverized Fuel firing burns the fuel in the Suspension Mode in the transport condition.
Between these, the two extremes lye on the Fluidized Mode.
According to 3T’s of combustion, there are two types of combustion beds, given as Residence Time, Temperature of Bed, and Turbulence.
CFBC (Circulating Fluidized Bed Combustion) - Higher residence time, combustion efficiency, and turbulence
AFBC (Atmospheric Fluidized Bed Combustion) - Comparatively lesser residence time, turbulence, lower desulfurization, and lower combustion efficiency.
(Image to be added soon)
We should also make a note that the primary reason to develop this combustion type is to limit the emission of hazardous gases such as SOx and NOx generated at higher bed temperatures.
3. What is the importance of boilers in the development journey of human beings?
The steam engine has been one of the cornerstones of human development in our history, in many ways it was the steam engines that led the industrial revolution. Some experts even go on to say that the steam engine was the biggest discovery in human history after the fire and the wheel which changed the course of history. The Boiler is an important part of the steam and hence very central to the development story of humans.
4. What is the principle of working of a steam engine?
A steam engine works on the principle of conversion of thermal energy into mechanical energy. The working of a steam engine is very simple where water is stored in a tank and then it is heated by fire using fossil fuels. As the fire raises the temperature of the water, steam starts generating in the tank. This steam is extremely powerful because it contains the latent heat of vaporization and when sufficient pressure is created the engine starts to move.
5. What is the use of boilers in the modern world?
Although steam engines are no longer widely prevalent in today’s world because of alternatives like diesel and electric engines, the boiler is still widely used in many applications like thermal power plants which generate a substantial proportion of India’s energy needs. Even in domestic use many people still use the pressure cooker which works on the same principle and has only become more important with time.
6. How do modern thermal power plants function?
The modern thermal power plants are humongous entities that produce many megawatts of energy and power our domestic and industrial needs. Although the scale of these plants is very large, at the core the basic principles are still the same, which is the conversion of thermal energy to electric energy. In these plants, coal is used as a fuel which fires up the water and converts it to steam, once the steam is generated it is connected to a turbine which rotates and generates electric energy.
7. How can the study materials along with exercise questions for Boiler be downloaded from Vedantu?
The Online resources at Vedantu can easily be accessed using 4 steps:
Open the Website of Vedantu on your Laptop or you can log in to the Vedantu App through your phone.
Search the subject of Thermodynamics and the topic of Boiler.
Click on Download PDF to download the solution in PDF format.
Enter OTP and then the solutions will be sent to your email ID.
Refer to Vedantu for free chapter-wise solutions and get free access to various other online resources and improve your learning in several folds.
(Image will be Updated soon)
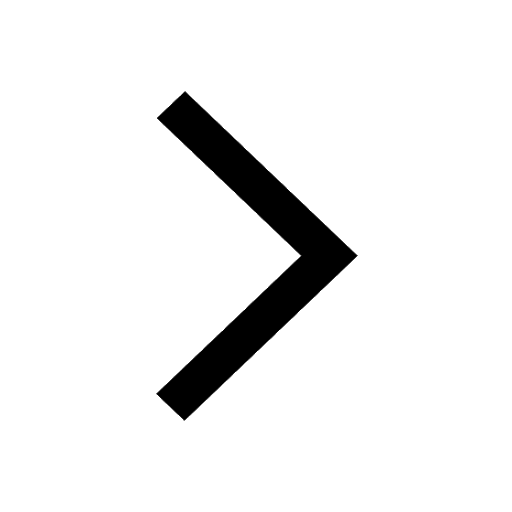
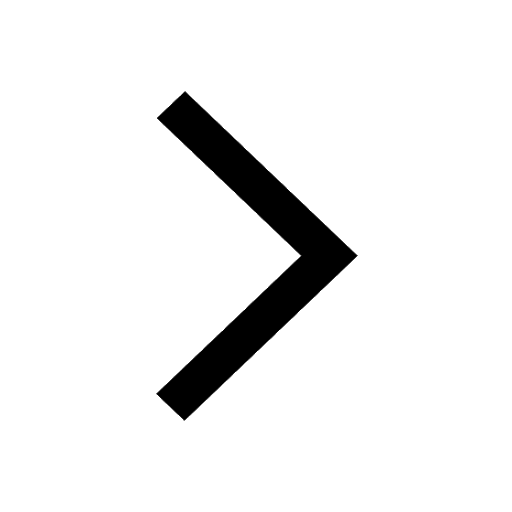
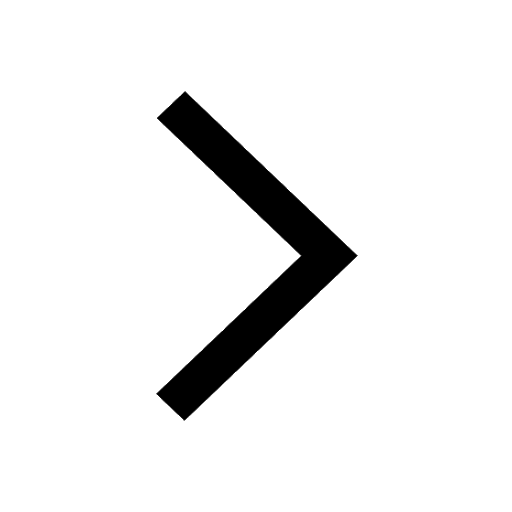
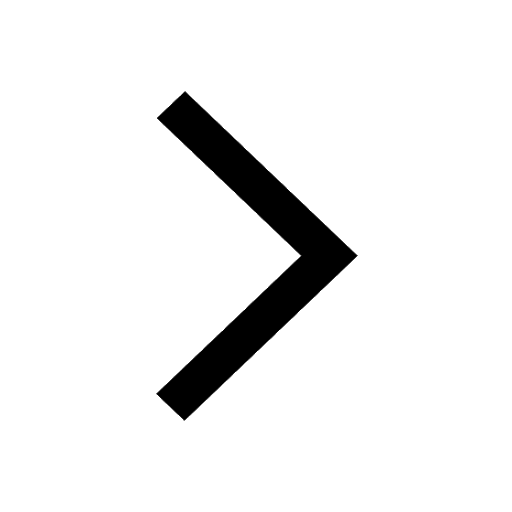
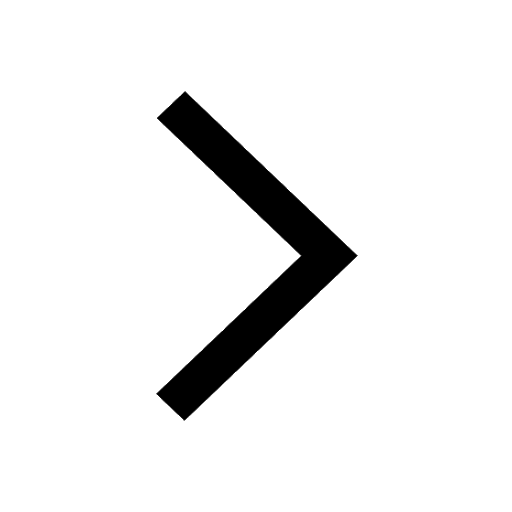
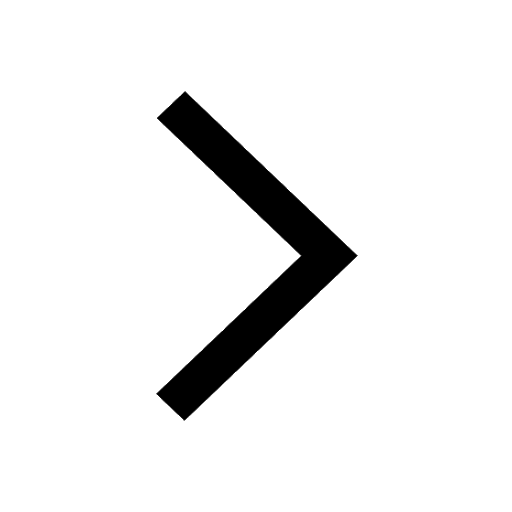
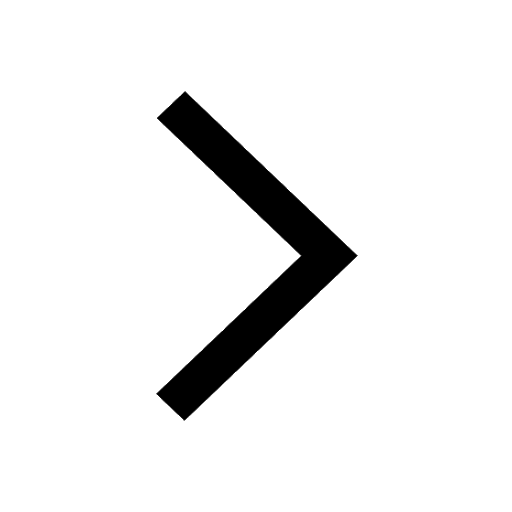
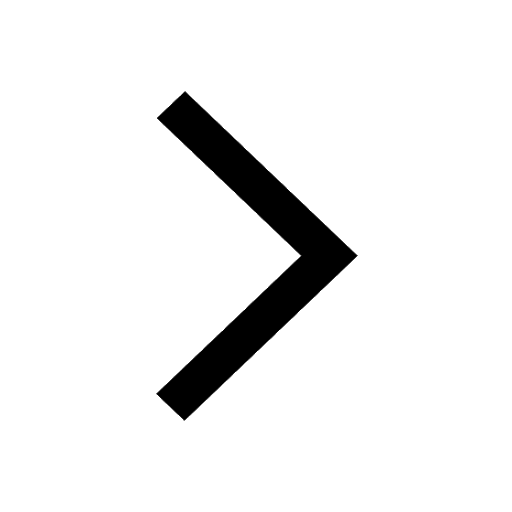
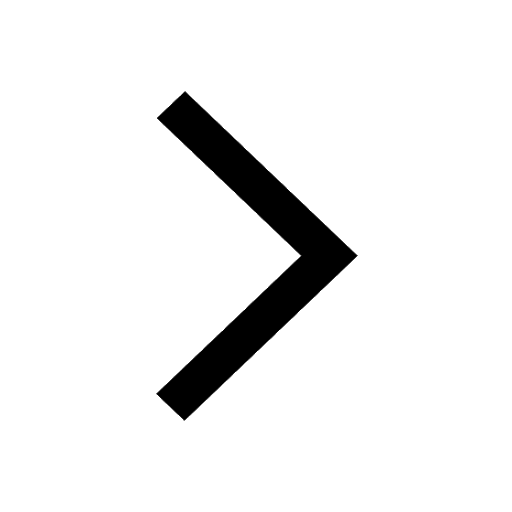
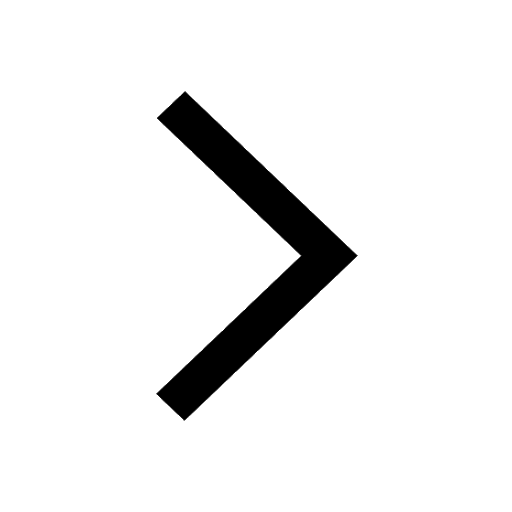
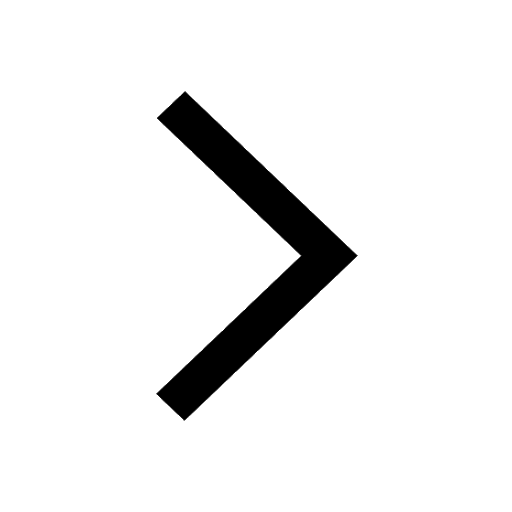
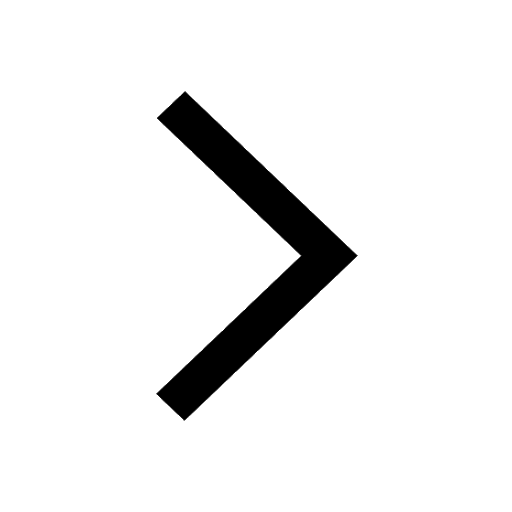
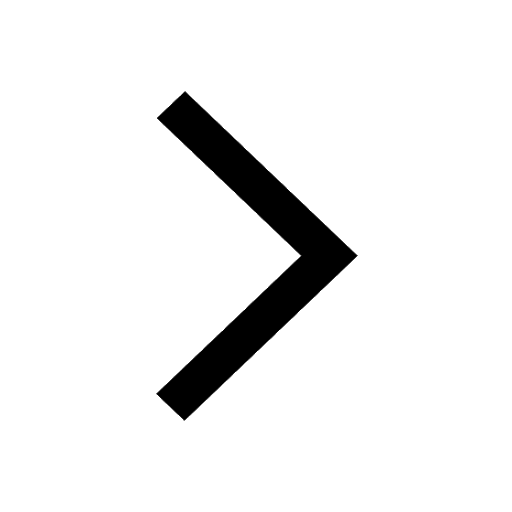
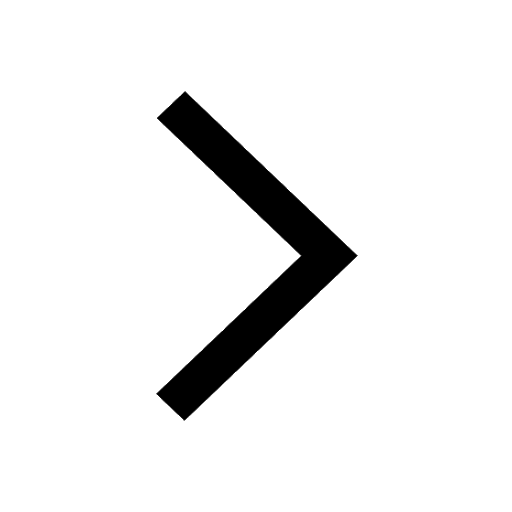
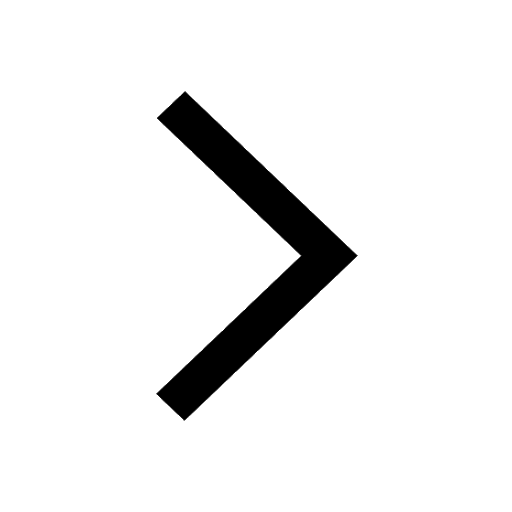
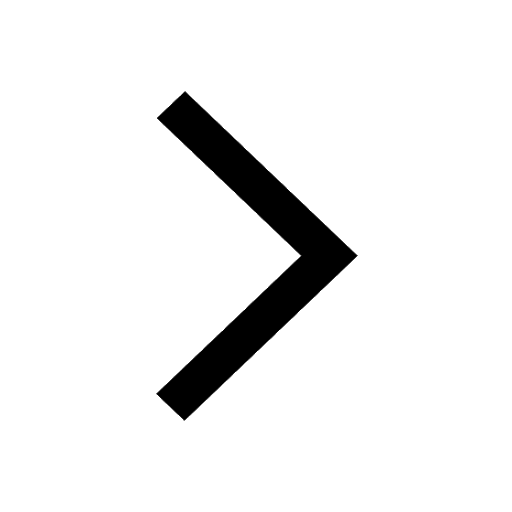
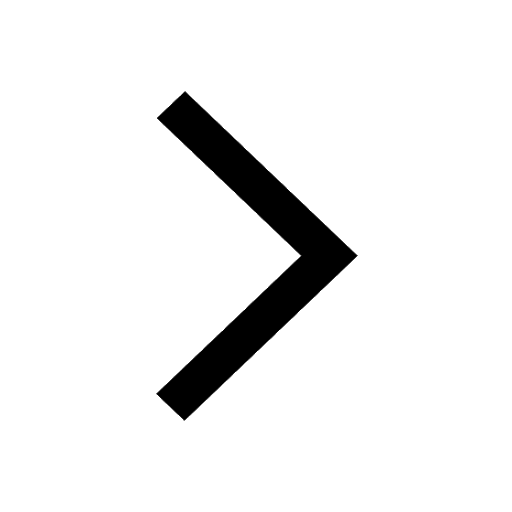
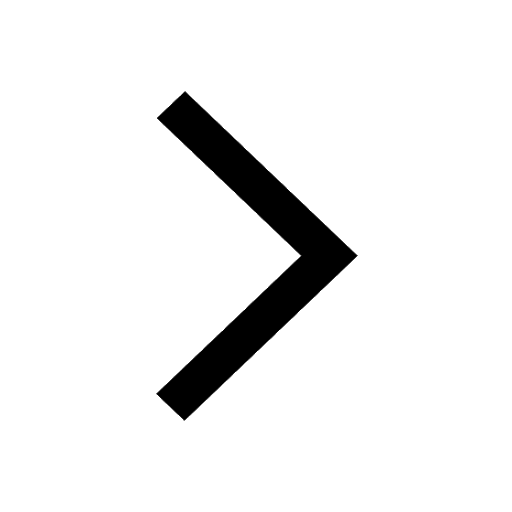