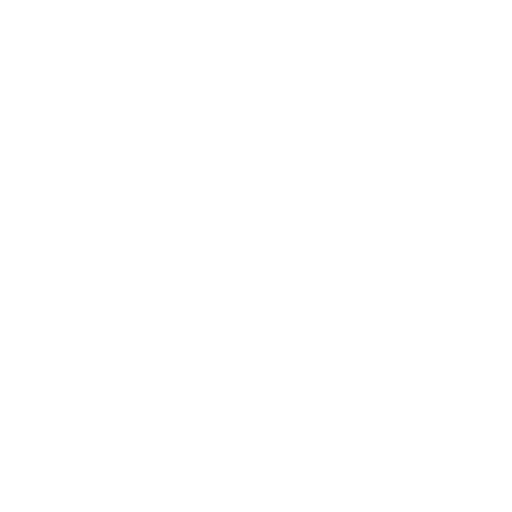

Modulus of Rigidity and the Dimensional Formula
The modulus of stiffness or shear modulus is denoted by G, or sometimes S or
Pascal is the SI unit for shear modulus. It is normally expressed in gigapascals or thousands of pounds per square inch. The dimensional form of the shear modulus is
Explanation of Shear Modulus
To measure the stiffness of materials, the shear modulus is one of many quantities. In Generalized Hooke's Law, all occur:
The strain response of the material to uniaxial stress in the direction of that stress (such as placing a weight on top of a column or pulling the ends of a wire, the wire s 'extending and the column loses height), described by Young's modulus E.
The retort in orthogonal directions to this uniaxial stress (the wire evolves thinner and the queue thicker), is described by the Poisson's ratio ν.
The hydrostatic (uniform) pressure of the response of the material (such as the pressure at the bottom of the ocean or a deep pool) is described by the mass modulus K.
The response of the material to shear stress (how to cut him with bevelled scissors) of the shear modulus is described by G. For isotropic materials they are related by the equations 2G (1 +υ) = E = 3K (1−2υ), and these moduli are not independent.
The deformation of a solid affects the shear modulus when it encounters a force parallel to one of its surfaces while its opposing face encounters an opposite force (such as friction). In the case of a rectangular prism, it will twist into a parallelepiped. Wood, paper, and even virtually all single crystals such as anisotropic materials show a different material response to stress or strain when tested in different directions. In this case, it may be required to utilise the full tensor term of the elastic constants, instead of a single scalar value.
Rigidity Modulus
The property of the material with a value equal to the shear stress divided by the shear strain is defined for the modulus of rigidity, also known as the shear modulus.
The general formula of the shear modulus is given below:
where the shear stress is τ in a given element, the unit of the force of which is divided by the area γ, which has no unit is the shear strain, and the shear modulus or stiffness modulus is G, which has the unit of force divided by the area. Shear modulus is another form of generalized Hook's law similar to the modulus of elasticity.
By performing a tensile stress test, it is possible to determine the modulus of rigidity, where the stress versus strain is plotted. The rigidity modulus is equivalent to the gradient of the line. Since the shear force over an area is equal to the shear stress and the strain is equal to the change in length divided by the initial length.
Shear Modulus
The modulus of rigidity or shear modulus which is denoted by G, or sometimes S or μ, in materials science, it is defined as the ratio of shear stress to the shear strain.
Pascal (Pa) is the SI unit of shear modulus, and usually, it is expressed in gigapascals (GPa) or in thousand pounds per square inch (ksi). Shear modulus dimensional form is
Explanation
For measuring the stiffness of materials the shear modulus is one of several quantities. In the generalized Hooke's law All of them arise:
The material's strain response to uniaxial stress in the direction of this stress (like putting a weight on top of a column or pulling on the ends of a wire, with the wire getting longer and the column losing height), described by the Young's modulus E.
The response in the directions orthogonal to this uniaxial stress (the wire getting thinner and the column thicker), is described by the Poisson's ratio ν.
Hydrostatic pressure (uniform) of the material's response (like the pressure at the bottom of the ocean or a deep swimming pool) is described by the bulk modulus K,
The material's response to shear stress (like cutting it with dull scissors) of the shear modulus is described by G. For isotropic materials they are connected via the equations 2G(1+υ) = E = 3K(1−2υ), and these moduli are not independent.
The deformation of a solid is concerned with the shear modulus when it experiences a force parallel to one of its surfaces while its opposite face experiences an opposing force (such as friction). In the case of a rectangular prism, it will deform into a parallelepiped. Wood, paper and also essentially all single crystals like Anisotropic materials exhibit differing material response to stress or strain when tested in different directions. One may need to In this case, use the full tensor-expression of the elastic constants, rather than a single scalar value.
A fluids one possible definition of would be a material with zero shear modulus.
Dimensional Formula and Derivation
Modulus of rigidity dimensional formula of is given by,
Where,
M = Mass
L = Length
T = Time
Derivation
Since, strain = ΔL/L = Dimensionless Quantity . . . . (2)
And,
The dimensional formula of,
Area =
Force =
While substituting the equation (4) and the equation (5) in the equation (3) we get,
∴ The dimensions of stress =
While substituting the equation (2) and the equation (6) in the equation (1) we get,
The Universal Gravitational Constant is dimensionally represented as
Shear Modulus of Metals
With increasing temperature, the shear modulus of metal is usually observed to decrease. The shear modulus also appears to increase at high pressures, with the applied pressure. The vacancy formation energy, melting temperature, and the shear modulus correlations have been observed in many metals.
attempt to predict the shear modulus of metals (and possibly that of alloys) is existing in Several models. In plastic flow computations, the shear modulus models that have been used include:
Mechanical Threshold Stress (MTS) plastic flow stress model is being used in the MTS shear modulus model developed by and used in conjunction.
The Steinberg-Cochran-Guinan-Lund (SCGL) flow stress model is used in the Steinberg-Cochran-Guinan (SCG) shear modulus model developed by and used in conjunction.
Lindemann’s theory is used in the Nadal and LeSpac (NP) shear modulus model that determines the temperature dependence and the SCG model for pressure dependence of the shear modulus.
Modulus of Rigidity
Material property with a value equal to the shear stress divided by the shear strain is defined for The rigidity modulus, also known as shear modulus.
Shear modulus general formula is written as shown below:
where the shear stress is τ in a given member, which has the unit of force divided by area (
By performing a tensile stress test the modulus of rigidity can be determined, where stress vs strain is plotted. The modulus of rigidity is equal to the slope of the line. Since shear force over the area is equal to the shear stress, and strain is equal to the change in length divided by initial length, we get the equation.
FAQs on Dimensional Formula of Modulus of Rigidity
1. Explain how the modulus of stiffness is calculated?
The shear modulus or stiffness modulus is the rate of change of the unit shear stress from the unit shear strain for the pure shield condition within the proportional limit.
The formula for the modulus of rigidity is
2. Explain the modulus of rigidity.
Stiff modulus, also known as shear modulus, is defined as the ratio of the shear stress to the shear strain of a structural member. This property depends on the material of the element, the more elastic the element, the higher the stiffness modulus.
The shear modulus in materials science where the modulus of rigidity is denoted by G or S is described as the ratio of the shear stress, where the force is the shear stress acting in an area is shear strain.
3. Explain axial stiffness.
The axial stiffness can be obtained as the EA of the non-cracked session + reinforcement in the cracked session, in the non-cracked area since the reinforcement does not contribute to the axial stiffness. The EA product is known as Axial Bar Stiffness. The quantity AE / L is the rigidity K of an axially loaded bar and is put to the force directed to produce a unit deflection without overextending a specific value of the permanent set (typically 0.2% = 0.002 inch/inch).
4. Explain the rigidity.
Rigidity is also known as stiffness. It is a measure of elasticity and represents the resistance of a material to a permanent set. Stiffness is the resistance of a material to bending, while strength is the resistance of a material to failure. It is measured by finding Young's modulus of a particular material.
It is also defined as the property of the solid to change shape. That is why if we apply an external force to the solid material, there will be no change in shape. This shows how close the particles are to each other and the attraction between them.
5. What is the stress and strain formula?
Stress = (modulus of elasticity) × strain.
Deformation = Modification of the original length
As the dimensional analysis of this relationship shows, the modulus of elasticity has the same physical unit as the stress because the strain is dimensionless.
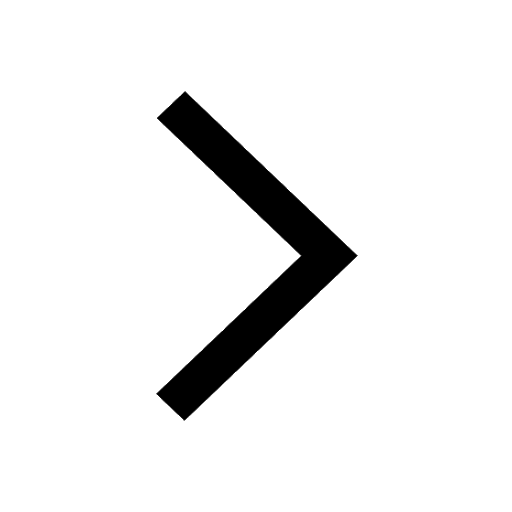
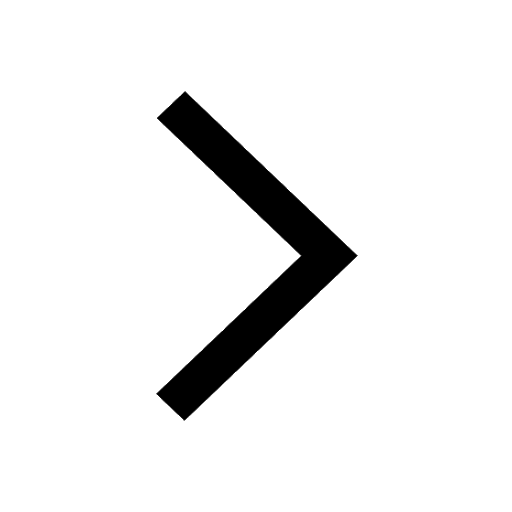
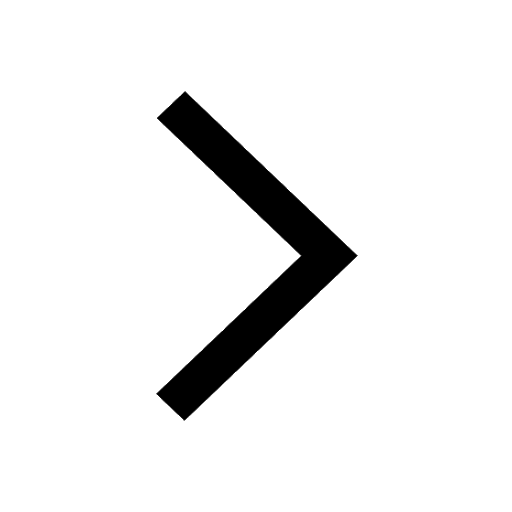
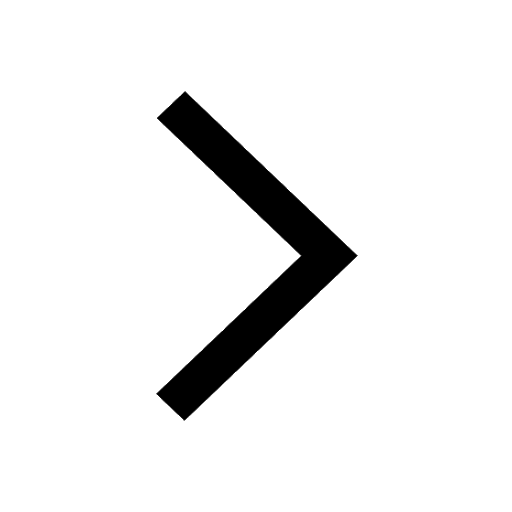
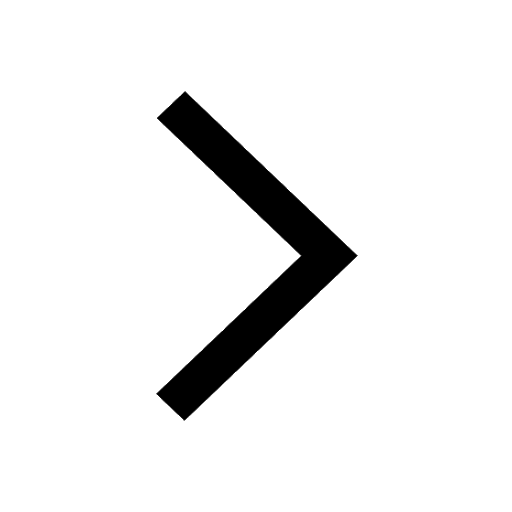
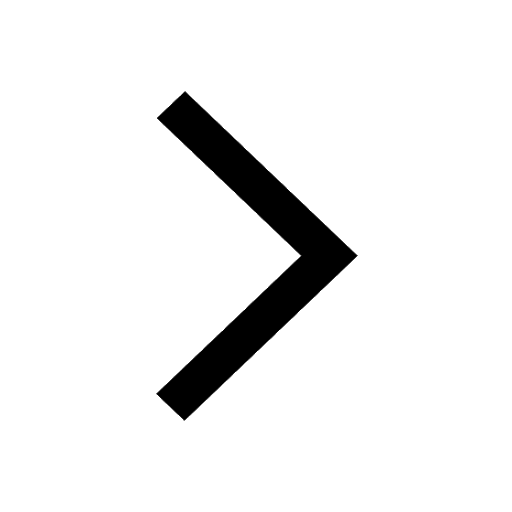
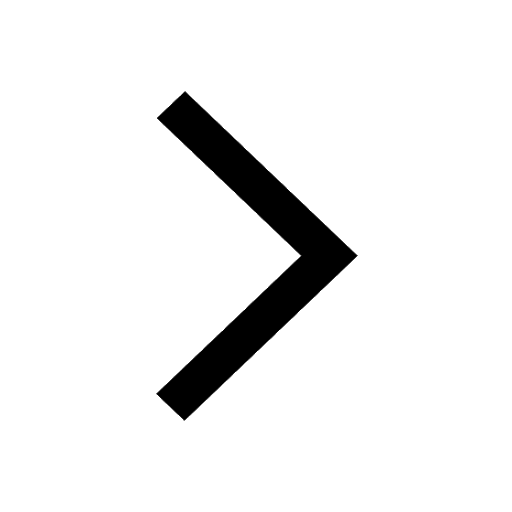
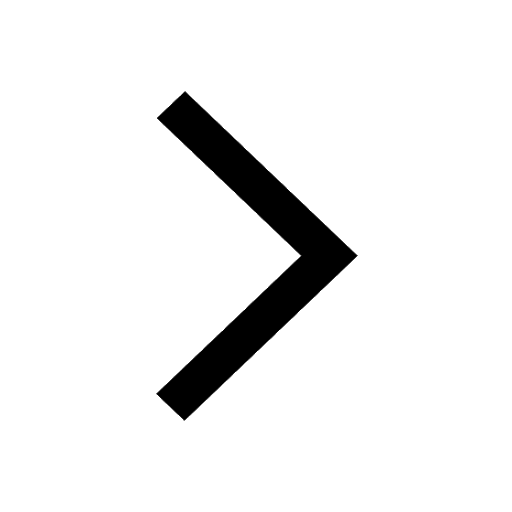
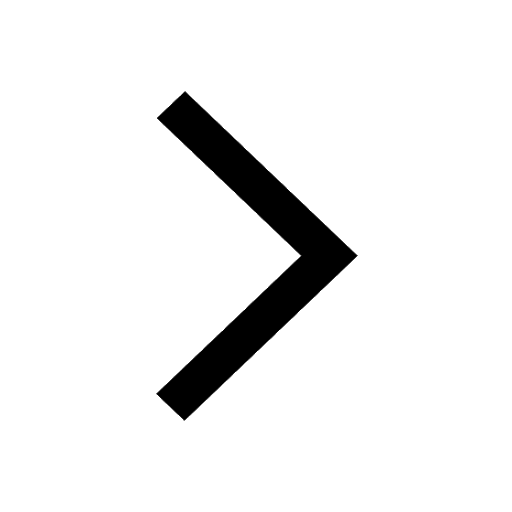
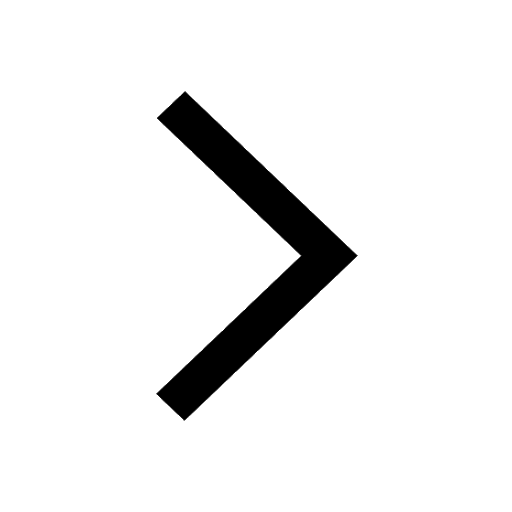
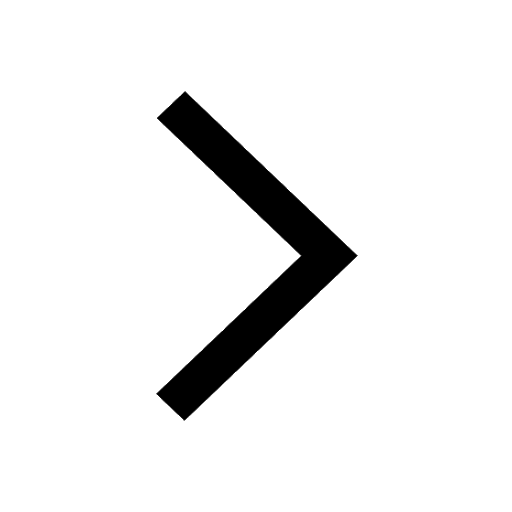
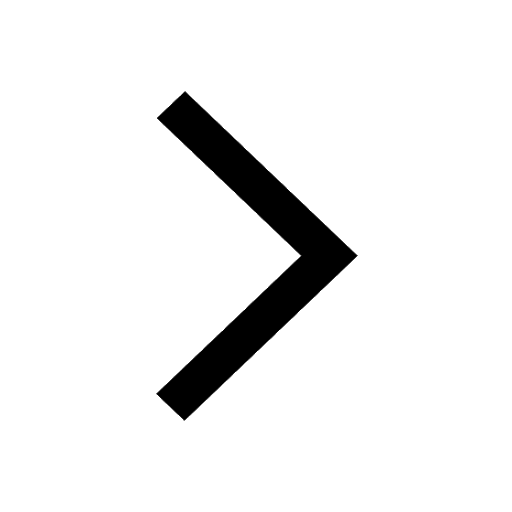
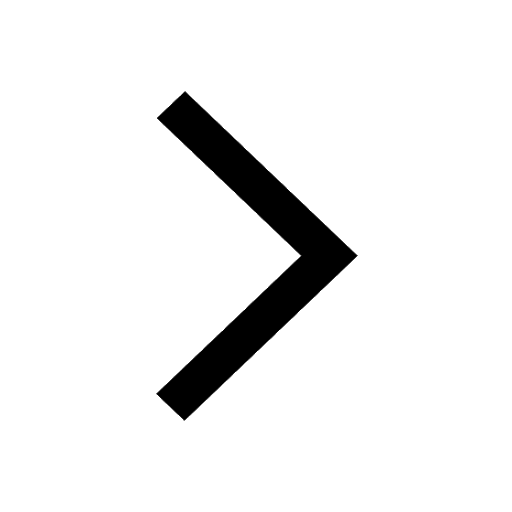
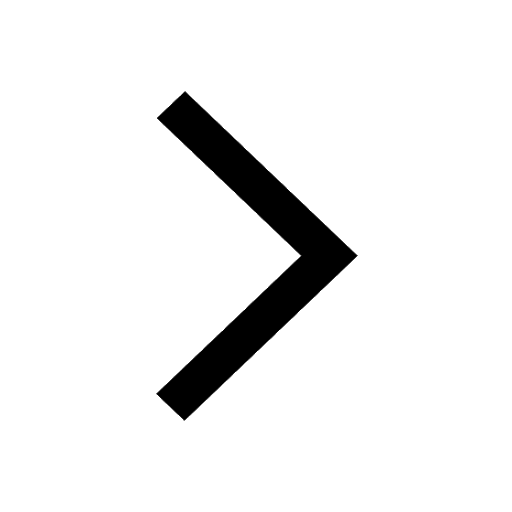
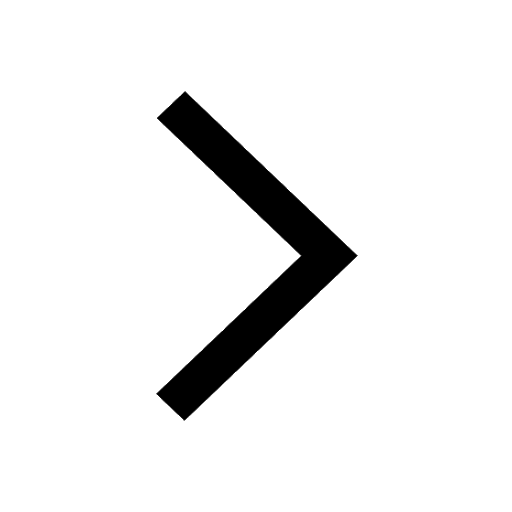
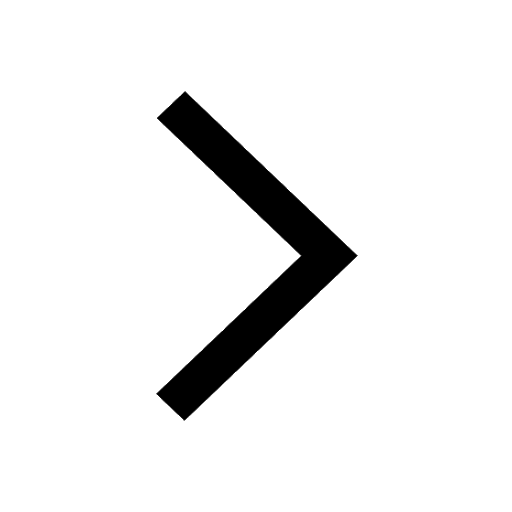
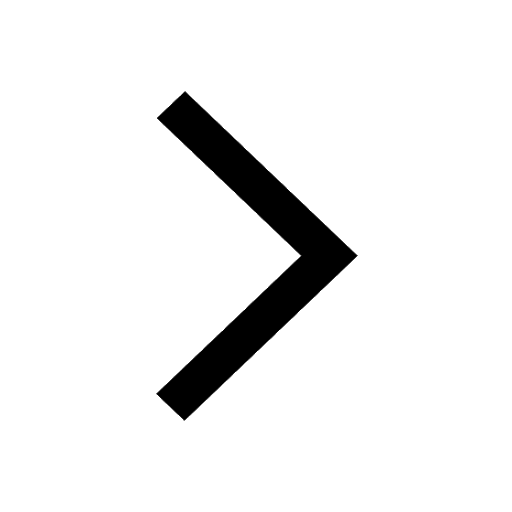
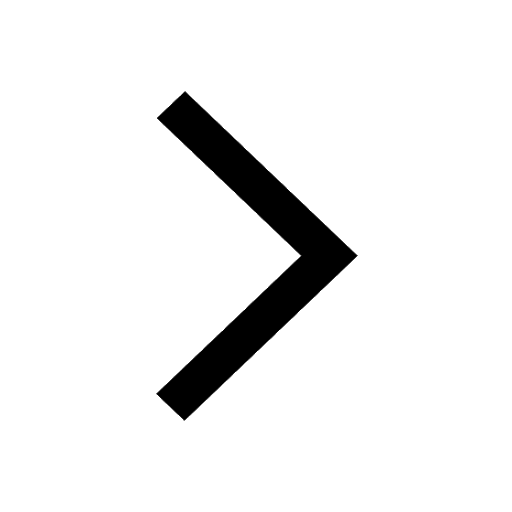