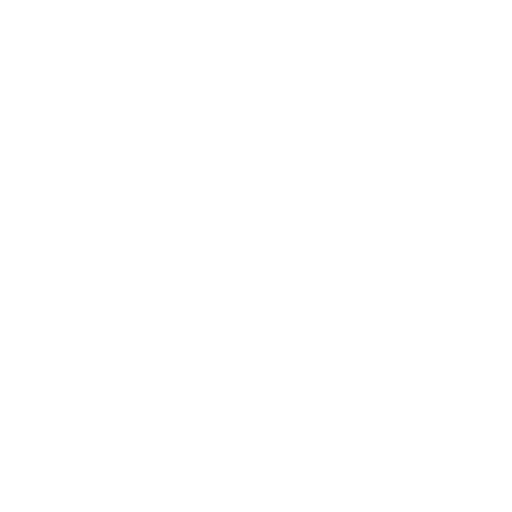

What Do You Mean By Scientific Management?
Scientific Management is another special sense of an approach to management in which it undertakes the responsibility for deciding the proper standards and all the methods of work which gives close supervision on the workers.
In simpler words, Scientific Management is the art of knowing accurately ‘what is to be done’ and ‘how this will be done’. Under this approach, the scientific techniques are applied in the recruitment, at the time of selection, and in training the workers and are also used in tackling various industrial problems. Also, we will know about the man behind these techniques in our next section and will be introduced to his scientific techniques.
FW Taylor
F.W. Taylor led to the emergence of the concept of ‘Scientific Management’. Frederick Winslow Taylor’s philosophy of scientific approach was developed and was popularized by his associates like Frank Gilbreth, H.C. Gantt, H. Emerson, and H.S. Person.
Taylor’s thinking on management is the subject-matter of the two books - Shop Management and the Principles of Scientific Management that were published in 1903 and 1911 respectively. For the efforts of Taylor, Scientific Management became popular in the U.S.A. at the beginning of the twentieth century.
“Scientific Management means knowing exactly what you want men to do and seeing that they do it in the best and the cheapest way”. —F.W. Taylor.
Techniques of Scientific Management by FW Taylor
Taylor has led down various techniques of Scientific Management which were as follows:
1. Work-Study
2. Standardization of Tools and Equipments
3. Scientific Task Setting
4. Scientific Setting of Wage Rates
5. Scientific Selection and Training
6. Functional Foremanship
7. Differential Piece-Rate Plan.
We will discuss all seven techniques in good detail.
1. Work-Study:
Work-study implies an organized based study. This objectifies, systematizes, the efficiency of various operations in an enterprise. All around, this technique analyses the whole system.
These techniques are also used in the examination of human work in all its context and which lead systematically to the investigation of all the factors.
2. Standardization of Tools and Equipment:
Taylor standardized tools and couplings, the cost system, and several other items. Thus, efforts are made to provide a standardized working environment with methods of production to the workers. Standardization techniques help to reduce the spoilage and wastage of the materials, improve the quality of work and thereby reduce the cost of production. This technique is also effective for improving fatigue among the workers.
3. Scientific Task Setting:
This is essential to set a standard task which an average worker will do during a working day. Taylor called it a fair day’s work. He put together the need for fixing a fair day’s work as this will prevent the workers from doing work that is much below their capacity.
4. Scientific Setting of Wage Rates:
Wage rates should be fixed in such a way that the average worker is induced to attain a standard output that is leveled up more than his level. Taylor thus suggested that the differential piece - wage system should be introduced.
5. Scientific Selection and Training:
The management is required to design the scientific selection procedure so that the right men are selected for the right jobs. The first step in this scientific selection is determining the jobs for which the workers are required. After this, the employees are appropriately qualified, trained, experienced and the level of efficiency for the post is then determined. The employees are selected according to the predetermined standards in an impartial way.
6. Functional Foremanship:
Taylor specified in this technique that specialization is to be introduced in a factory. He advocated ‘functional foremanship’ for this purpose. A functional foremanship is a form of an organization that involves supervision of a worker by several specialist foramen. Example - matters relating to the speed of work and repairs of machinery are to be supervised by the speed boss and the repair boss respectively in this case.
7. Differential Piece-Rate Plan:
This plan as suggested by Taylor is to attract highly efficient workers. In this plan, there are two-piece work rates, the one which is lower and the other is higher.
(Image will be uploaded soon)
Foremanship with a Purpose:
A factory administration system that allows for the presence of many foremen in independent, functional roles is known as functional foremanship. Traditionally, factories had only one manager to oversee operations. For manufacturing workers, this manager or foreman was their only point of contact. Frederick Winslow Taylor, the eminent engineer who revolutionized Scientific Management at the turn of the century, uncovered a major flaw in this method. When he compiled a list of all the qualities that a good supervisor must possess, he realized that no one individual could possibly possess all of them. As a result, the concept of working foremanship was conceived.
Workplace Standardization and Simplicity:
What is the Definition of Standardization?
Standardization refers to the process of setting standards for any industrial activity, such as the way things are done, the amount of time they take, the raw materials they use, the machinery they use, the products they make, the processes they go through, and the situations they go through. These examples serve as guidelines that must be followed throughout the process.
What Are Management Principles? Related Reading: What Are Management Principles?
What is the Definition of Simplification?
Simplification refers to the removal of non-essential kinds, sizes, and measurements, whereas standardization refers to the creation of new types rather than existing ones. The goal of simplification is to eliminate a variety of products that are redundant. Machines, tools, and labor costs are reduced as a result. It entails keeping inventory under control, making full use of commodities, and increasing turnover.
Study Method:
The goal of the research is to discover one vigorous method of accomplishing the job. The job can be done in a variety of ways. There are a number of variables to consider when determining the optimum path. Every endeavor, from obtaining raw materials to presenting the final product to the user, is part of method research. Using the technique research, Taylor came up with the concept of the assembly line.
Motion Analysis:
Motion analysis is the study of actions such as placing objects, lifting, changing positions and sitting that occur when doing a routine task. Random motions are encouraged to be reduced so that the job can be completed in less time.
Study of Time:
It reduces the amount of time it takes to execute a specific task. For each step of the task, time-keeping devices are used. Various readings are used to determine the standard time for the full task. The duration of the time study will be determined by the task's frequency and volume, as well as the process's cycle time and time measurement costs.
Fatigue Research:
If a person does not relax while working, he or she will get emotionally and physically exhausted. Rest periods will aid in the recovery of vitality and the ability to work at the same level again. As a result, the potency will be increased. The goal of fatigue research is to determine the amount and frequency of rest intervals required to complete a task.
FAQs on Scientific Management Techniques: Key Methods
1. What is Meant By the Differential Piece Wage System?
The Differential Piece Rate System was introduced by Taylor, who is known as the father of Scientific Management. The principle in this system is authorized to penalize the slow worker by paying him a low piece rate for low production and to reward an efficient worker by giving him the higher piece rate for higher production.
This is a method of wage payment whereby after the tests have been set, a standard time for a task the worker then receives a high piece rate for doing the job in task time and then a lower piece rate for taking longer than the task time.
2. What is the Purpose of this Scientific Management?
Scientific Management is defined as the theory of management that analyzes and synthesizes workflows. The main objective of Scientific Management is to improve economic efficiency, especially labor productivity. This was one of the earliest attempts to apply science to the engineering of processes to management. You can know about the purpose of this Scientific Management with the proper theory and analysis based on the free PDF on Vedantu.
3. What is the Limitation of Scientific Management?
Scientific Management has neglected to recognize the importance of workers somewhere. Subsequent studies to improve workplace productivity considered the importance of employees, their knowledge and needs. Poor treatment of workers led to the rise of unions which increased the strikes and unrest. This limitation is something that people should work on and get the pros and cons for the same. You can learn with the help of the PDF of Techniques of Scientific Management.
4. What is Scientific Selection and Training?
Management has an important role in selecting the people for the right job. You need to clear the main layer out of the pit and have the responsibility to obtain the best one for the right position. After the selection, the people are screened for their jobs and trained accordingly. This includes making them appropriately qualified, trained, experienced and the level of efficiency for the post is then determined. Employees can be selected later in an impartial way based on the above-mentioned factors.
5. What is Work-Study?
Work-study includes and is said to objectify, systematized, the efficiency of various operations in an enterprise. It is basically an organized group study and analyzes the whole system of an organization. The techniques used in the work-study techniques are also used in the examination of human work in all its context and which lead systematically to the investigation of all the factors. It can be well led by an individual if he is to use techniques of Scientific Management.
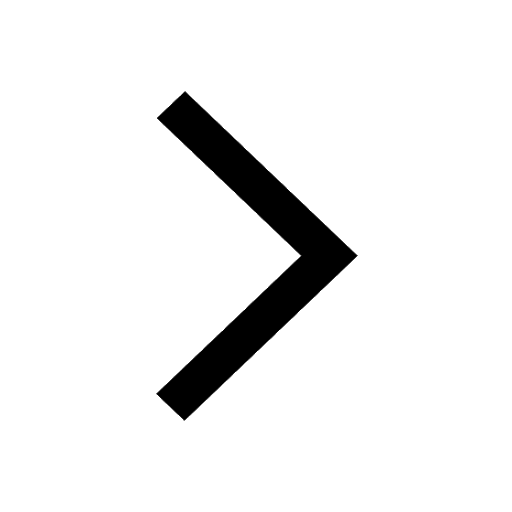
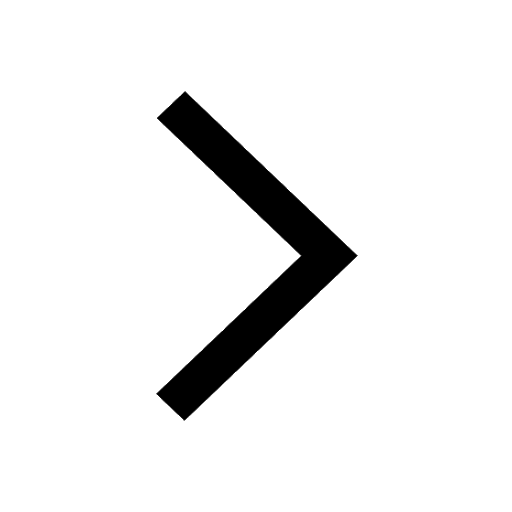
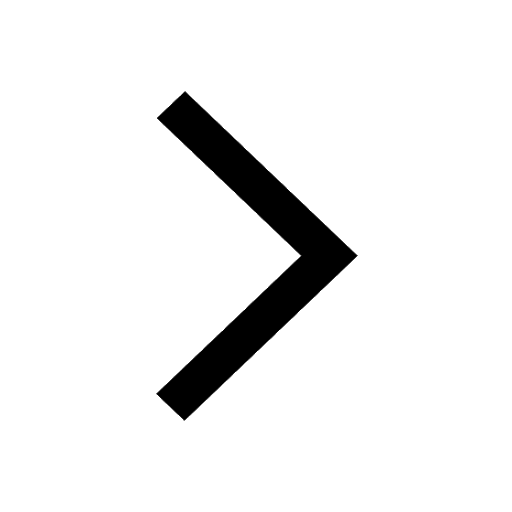
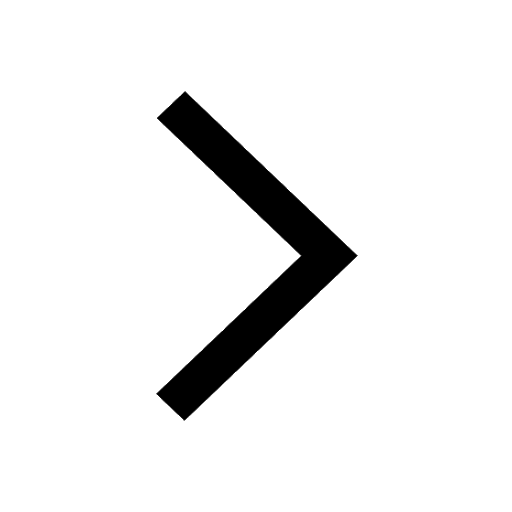
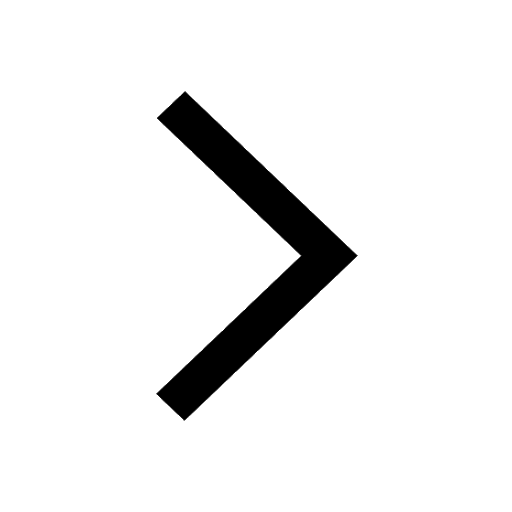
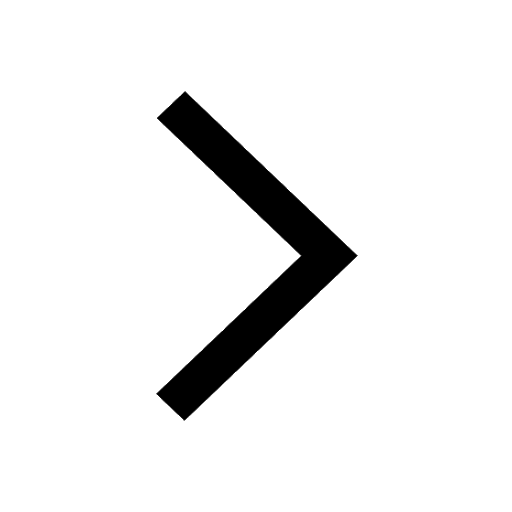
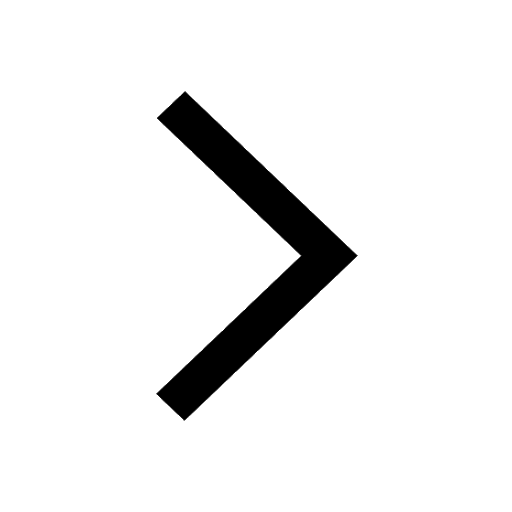
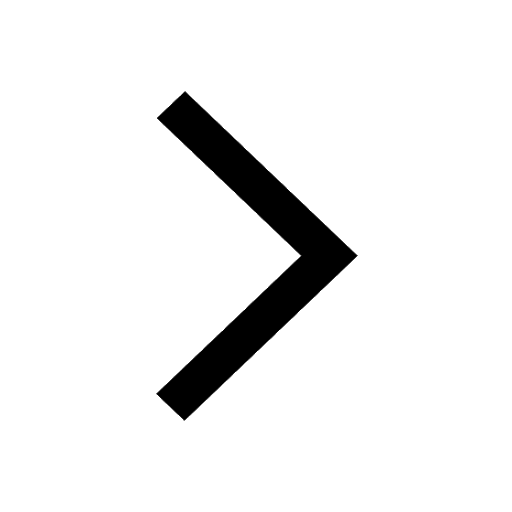
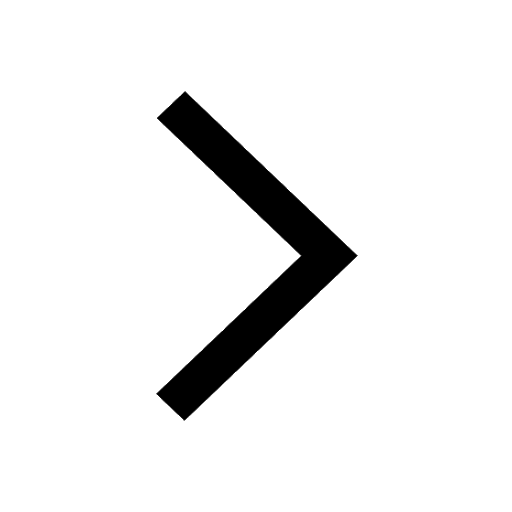
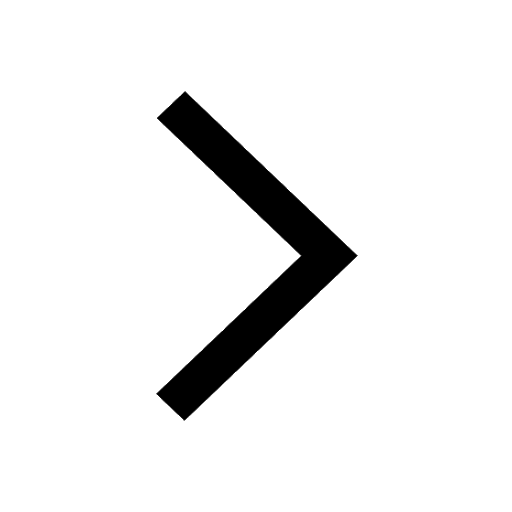
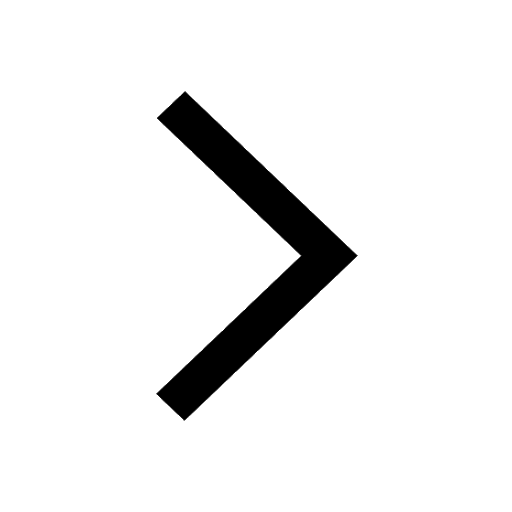
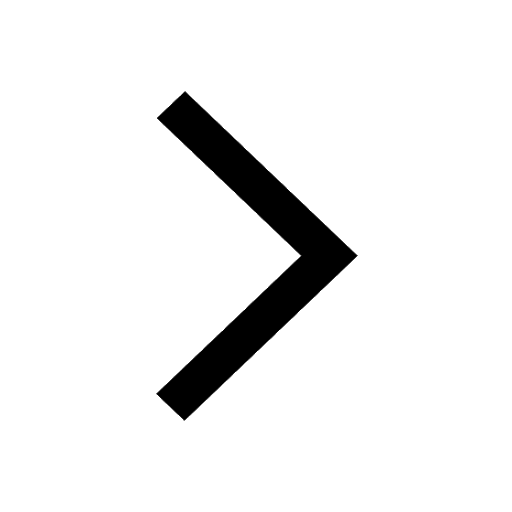