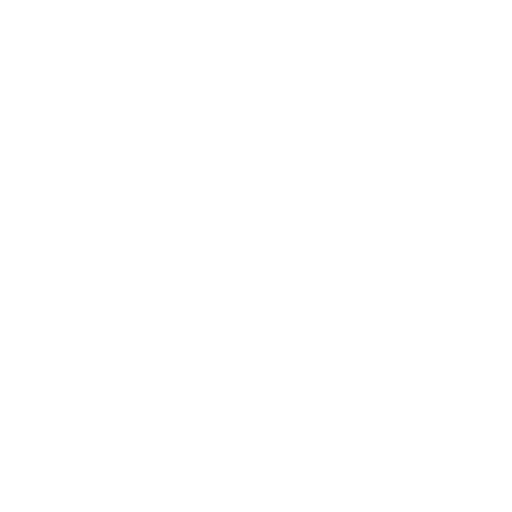

What is Operating Costing?
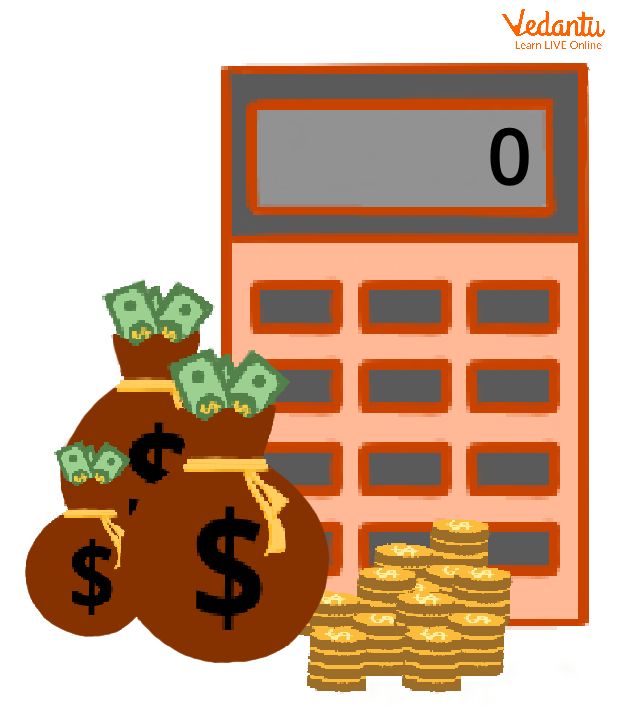
Operation Costing
The operating cost meaning is a technique used to determine a product's final price by analysing the associated overhead costs of a particular production run. This comprises the costs of goods, labour, and facility maintenance. For straightforward production models where items go through the same operating cost formula each time, businesses often employ process costing.
However, some companies could use operation costs to assist with their more complicated production models. For a better understanding of operating costs, let's take an example: a firm selling customised shirts may wish to compute expenses to compensate for varied expenditures.
Why is Operation Costing Important?
Accounting experts can better comprehend and manage expenses thanks to operation costing, which lets organisations account for the total cost of each process. As a result, companies strive to minimise operational expenses while keeping their output as steady and efficient as possible.
This strategy may help businesses increase their profitability by reducing the risk of charging more than necessary for their products because of excessive operating expenditures. In addition, companies that make both mass-produced and custom items may find this approach valuable since it works well in scenarios where products need both specialised and mass-scale manufacturing processes.
How to Calculate Operation Costing?
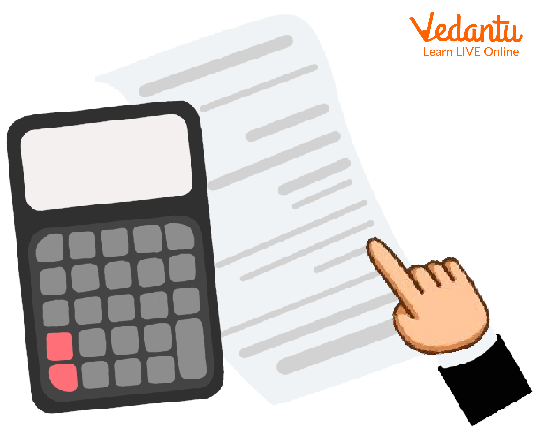
Calculation of Operation Costing
The complexity of a product's manufacturing process might affect how a business determines its production costs, as there are many types of operating costs. It's possible, for instance, that the operating stages of a furniture firm that lets consumers choose their materials, colours, and designs might be more complicated than those of a company that limits clients to a set of predetermined options. Some easy-to-follow guidelines for determining operational costs are listed below:
Cost Analysis of Processes - How much costs to manufacture a product in bulk is the starting point for any analysis of operational expenses. In addition, the sequence in which a business purchases and sells those purchases may significantly impact costs.
Estimate the Project's Price - Step two of gathering operating costs involves tallying up the money spent making a product. Those costs include salaries, supplies, and other similar overheads. Umbrella manufacturers, for instance, have to factor in the price of metals and fabrics, labour hours, rent or lease payments, utilities, and maintenance and repair of machinery and tools.
Determine the Whole Running Expenses - To calculate the total cost of manufacturing, you must first determine how much each task and procedure will cost. You may also keep track of the specifics of any variables or inputs that you believe may change in the future.
Review Sums for Each Procedure - Once you get the summaries, you may evaluate how much the firm spent on each activity. Profit margins, cost factors, and outliers may all help you figure out where your business might stand to improve.
Upsides of Learning about Operational Costs
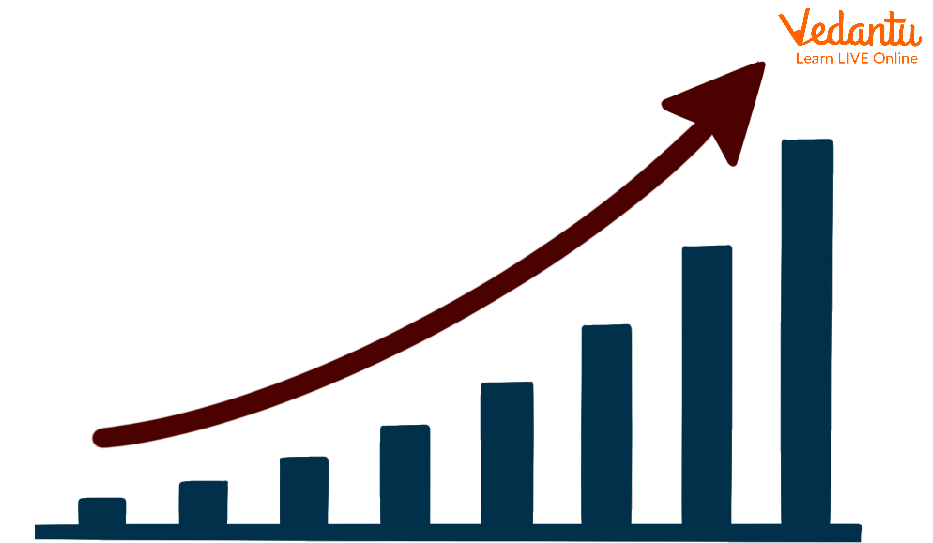
Benefits of Operation Costing
The following are just some additional benefits of learning about operation costing:
Restrain your Spending - Professionals might find savings by using operation costing to analyse where their money is spent in manufacturing. For instance, if the firm's accountants determine that too much money is being spent on rent for just a location that doesn't move much product, the corporation may choose to shut down that location and reallocate the stock elsewhere.
Control and Evaluate the Administration - A separate expert may oversee each manufacturing phase. By analysing these processes through operation costs, a business may determine where enhancements can be made, allowing relevant management to pursue more education and alter their methods accordingly.
Save Time and Effort - The results of a cost estimate for running operations may be used to pinpoint inefficient steps in a company's workflow. For an example of operating cost, if an accountant sees a lag in orders slowing down inventory delivery, they could recommend changing the ordering software.
Fidelity Improvement - A company's total budget will reflect the operating expenses it has calculated. This might aid in their cost accounting and resource management.
Assume that the Market will Constantly be Changing - Product, labour, and maintenance costs may shift due to economic fluctuations. Knowing how much things have cost in the past might help a business prepare for future changes.
Conclusion
The costing technique, which determines the unit price of the product from each operation and is a step in the manufacturing process, determines the price per unit. A critical distinction between activity-based costing and process costing is the emphasis placed on treating each activity as its cost centre. This means that we keep track of the total cost of all the stuff we use and the people we pay to do it for each process. At the same time, each function receives its fair share of overhead costs.
FAQs on Operation Costing: Definition and Examples
1. In what contexts is an operational cost most useful?
Operating costing is applicable to the costs involved with providing a service that has a greater priority than the expenditures related to producing a physical commodity. This is because the costs associated with providing a service tend to be more variable. Providing a service has a greater overhead than making a tangible commodity. Businesses that operate in the following industries make use of it: transportation, utility services (including natural gas, water, and electricity), food and beverage services (including cafes, cafeterias, hospitals, dining halls, theatres, and other similar venues).
2. How do you calculate the cost of operations?
The Cost of Goods Sold (COGS) is the formula that is used to determine how much it costs to run a business. This operating cost formula consists of the following components: Initial Inventory, Buys, and Direct Expenses, less the Inventory on Hand at the End of the Accounting Period. After that, you should make an accurate count of all of the costs that are associated with running the business. You may determine your total operating price by first determining your cost of goods sold (COGS), and then adding that number to your operating expenditures.
3. How come it's crucial to take into account operational costs?
It is probable that the operating costs of a firm are the greatest measure of how effectively the company is managing its cash flow and assets. It illustrates the extent to which the firm must pay expenses in order to function, which should be the primary emphasis of any and all companies. The generation of a profit ought to be the main focus of any and all organisations that are run for profit.
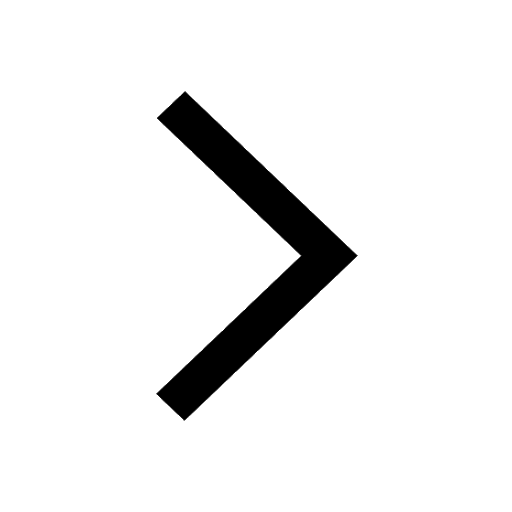
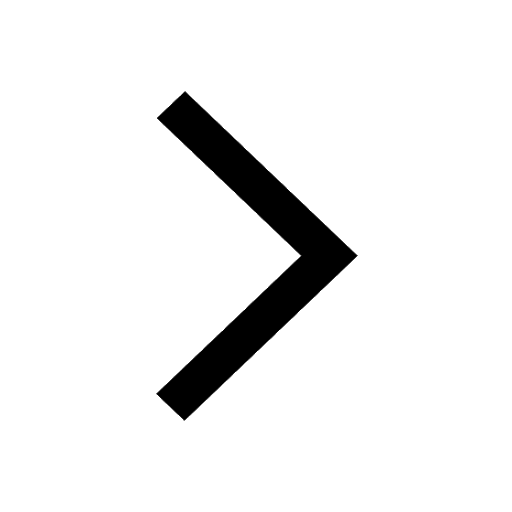
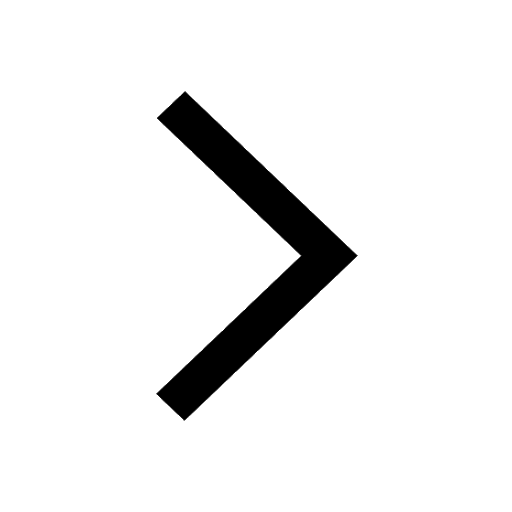
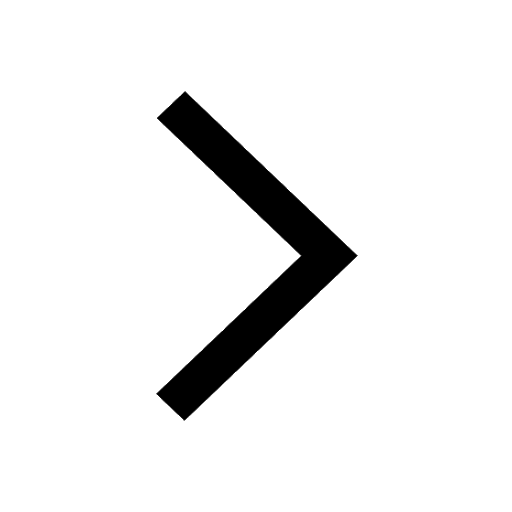
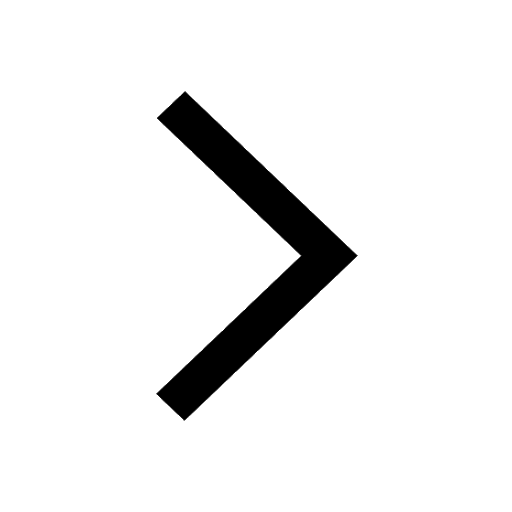
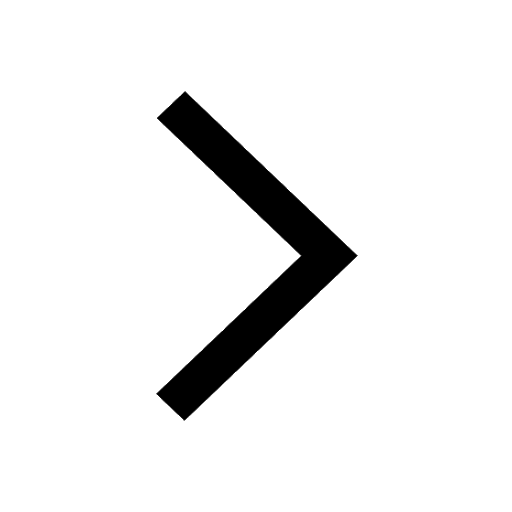
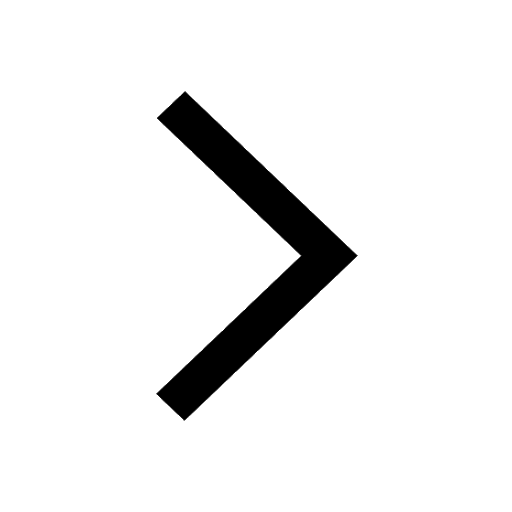
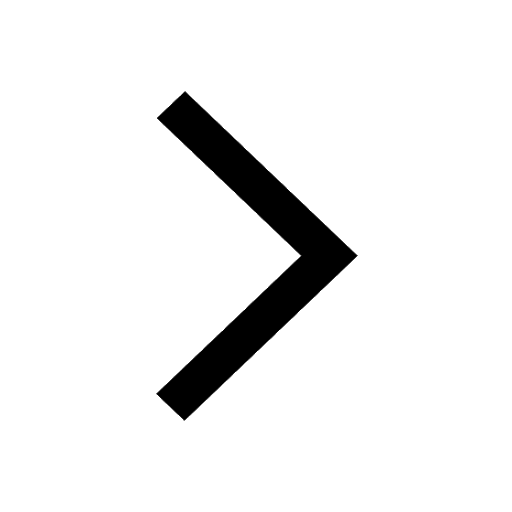
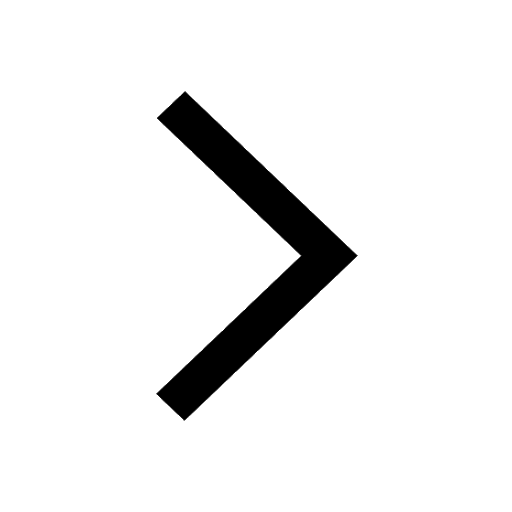
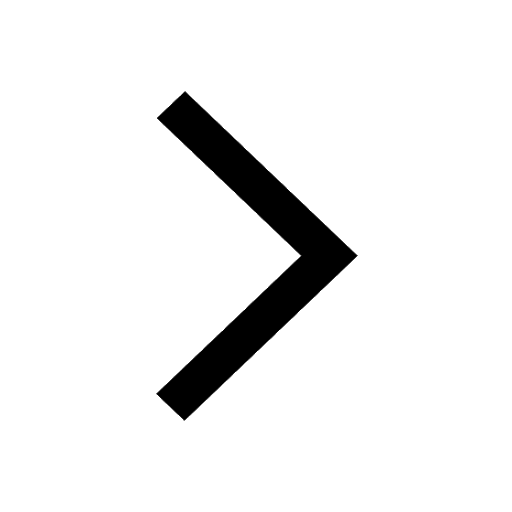
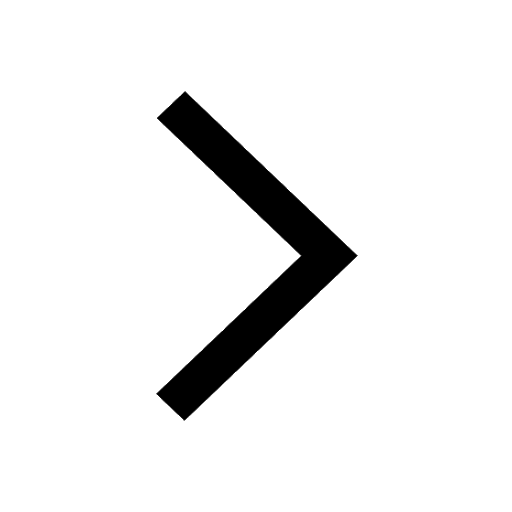
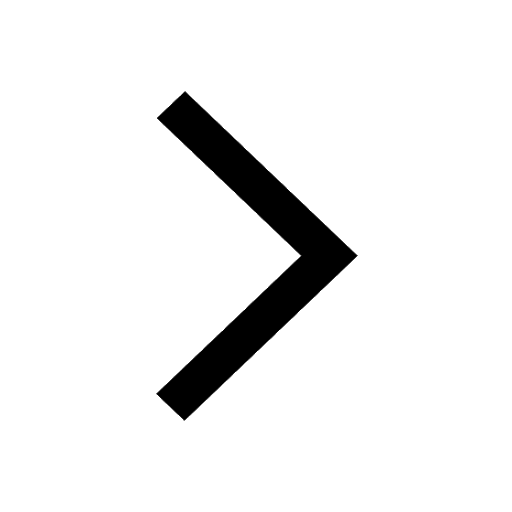
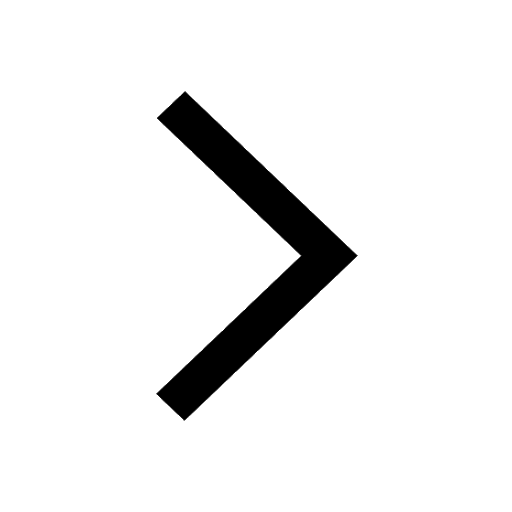
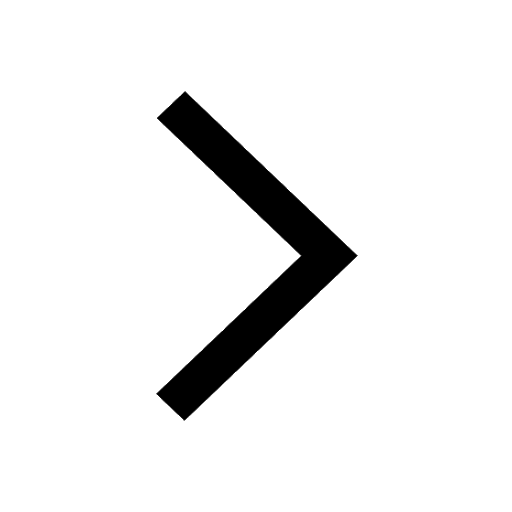
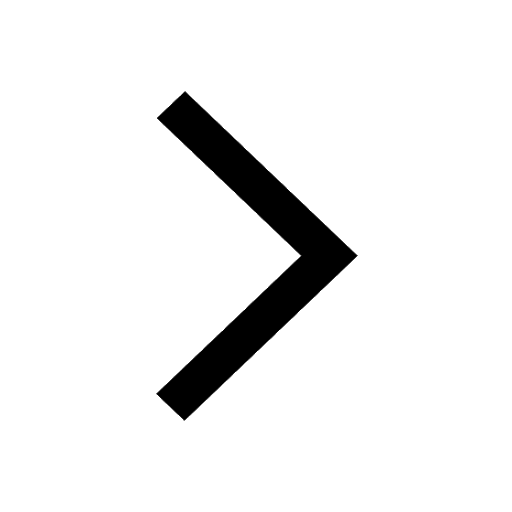