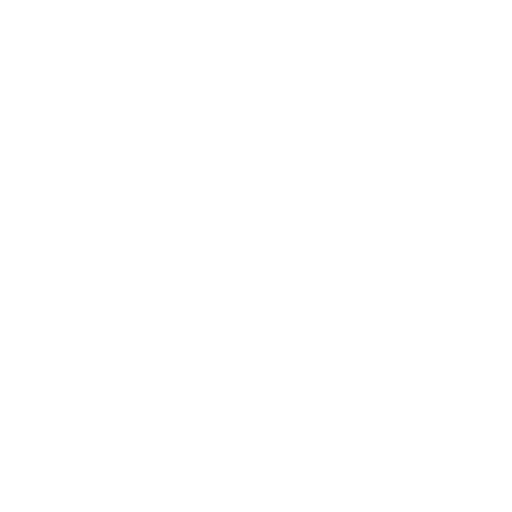

What is the Leaching Process?
The process of leaching is used to extract the substances from the solids. This process is carried out when the given substance is allowed to dissolve in a liquid. It is carried out either through a natural process or industrially.
The leaching process shows the release of both the organic as well as the inorganic radionuclides or contaminants from a solid-state to a liquid state when they get influenced by different processes like mineral dissolution, complexation, and desorption.
The process of leaching is known to be a universal process in which water tends to leach the material components that come in contact with it. This can be its surface or its interior depending on how porous the material is.
The ore of the given metal can be concentrated using this process when a chemical reaction is caused with the help of a reagent that would eventually lead to the ore getting dissolved and the impurities undissolved.
Leaching Process Examples
The leaching process example includes the leaching of bauxite or Al2O3 . 2H₂O with the concentrated and heated sodium hydroxide. The concentrated NaOH here tends to dissolve the aluminium present in the given bauxite, while on the other hand, the impurities like SiO2, TiO2, and Fe2O3 do not get dissolved. The chemical reaction of this leaching process is given as follows.
Another example of the process of leaching is leaching of the noble metals like silver and gold in the presence of the dilute aqueous solutions of either potassium cyanide or sodium cyanide in the presence of air. The chemical reaction for this process of leaching for silver is given below.
The leaching process also causes the loss of nutrients that are present in the soil because of heavy rainfalls.
Advantages and Disadvantages of Leaching Process
Advantages of Leaching are as Follows.
The leaching process is easier when it comes for the execution.
It is not a harmful process in comparison to the other pyrometallurgical methods.
It does not lead to any sorts of gaseous pollutants.
Disadvantages of Leaching are as Follows.
The residual liquid waste that is generated from the leaching process is highly acidic in nature.
The effluent of the leaching process is toxic.
The efficiency of the leaching process is entirely dependent on temperature.
Types of Leaching Processes in Metallurgy
The different kinds of leaching processes which are used in industrial purposes for metallurgy are given below.
Heap Leaching: It refers to a process which extracts uranium, copper and many other precious metals from their ores.
In-situ Leaching: It is a process which recovers uranium and copper.
Tank Leaching and Vat Leaching: They are the processes in which the ores are to be placed in vats or large tanks that consist of the leaching solutions. These processes are used for the extraction of the metals from their ores.
Leaching Process
Leaching is the process of releasing solid material constituents into a contacting water phase. Although some species may pose a greater environmental risk than others, the leaching process is indiscriminate, meaning that all constituents (e.g., major and minor matrix components, as well as inorganic, organic, and radionuclide contaminants) are released through a common set of chemical processes that include mineral dissolution, desorption and complexation, and mass transport processes. These events, in turn, are influenced by a variety of factors that can affect the rate and degree of leaching. These are some of the aspects to consider:
Chemical and physical responses within the body
external stressors imposed by the environment
Physical deterioration of the solid matrix as a result of erosion or cracking, as well as
The leaching process itself causes a loss of matrix elements.
The partitioning of pollutants between a solid and liquid phase (e.g., assuming local equilibrium) is combined with the mass transport of aqueous or dissolved elements in the leaching process. The sum of diffusion, impeded diffusion, tortuosity effects, and effective surface area effects through the material's pore structure to the environment is known as mass transport. Solution pH, redox, the presence of dissolved organic matter, and biological activity are all important chemical parameters that influence a constituent's liquid-solid partitioning (LSP).
Physical properties including relative hydraulic conductivity, porosity, and fill geometry all play a role in influencing how quickly constituents move through a solid and into a passing liquid phase.
The process is universal in nature, since any substance exposed to water may leach components from its surface or interior, depending on the porosity of the material
Process of Leaching
The solvent comes into touch with the solid matrix for the first time. A solvent is a liquid that dissolves a material or solute. A solvent dissolves a solute, which is an element. As a result, the solvent will turn into a liquid, while the solute will be the component extracted from the solid matrix. Furthermore, in our tea example, the solute would be the extracted green tea, and the solvent would be hot water.
There are many different types of leaching processes, which are mainly categorized based on the reagents utilized, Such as Cyanide leaching (e.g. gold ore),Ammonia leaching (e.g. crushed ore),Alkali leaching (e.g. bauxite ore),Acid leaching (e.g. sulfide ore)
The reagents needed are determined by the ores or pretreated material being processed. Oxide or sulphide is a common feed for leaching.
FAQs on Leaching Process
1. What is heap leaching?
The heap leaching is a kind of industrial mining process which is useful for the extraction of precious metals, uranium, copper and several other compounds from their respective ores. This is done with the help of a series of chemical reactions that tend to absorb specific minerals and tend to re-separate them once they undergo a division from several other earth materials.
The process of heap leach mining occurs when the ore is placed on a liner and the chemicals are then added to it with the help of the drip system. This process is extensively used in today’s larger-scale operations of mining since it generates the desired concentrates at a comparatively lower cost when compared to the traditional methods of processing like vat leaching, agitation, and flotation.
2. What is vat leaching?
Vat leaching is a process which is carried out in the vats that have a capacity ranging from 30 - 1200 tons. The sand used for leaching gets separated from the slime in the cones, classifiers, V boxes and the collecting vats that are filled by the distributors. The overflow in each of the mentioned cases is either the finer portion of the ore or the slime.
Leaching is the process which involves the mixed and neutralized sand vat, water washes, enough contact with the weak and the strong cyanide solutions, the rapid filling and discharging, and the aeration of the solution and the sand.
This process is very effective and cheap to clean the ores wherein the process of fine grinding is not required for a better extraction.
3. What is in situ leaching?
The in-situ leaching is a leaching method in which the metal values are directly leached from their ores without the need to excavate the ore before leaching. The leaching reagents which tend to dissolve the metals that are desired get pumped to the deposit via the injection wells. The leachate gets collected in the centrally located underground wells or dumps and then later gets pumped to the surface via the recovery wells to undergo the further processing above the ground. The permeability of the body of the ore is essential and in case the ore does not have the natural porosity that is required, it gets fractured by the explosives. This allows the injected solution from through the deposit.
The ores that are suitable for the in-situ leaching are generally situated below the aquifer. This method is used for the extraction of the uranium, copper and several other soluble salts like potash, halite, boron and the magnesium minerals.
4. What is eco friendly leaching?
Leaching That Isn't Harmful to the Environment
We have had some success in determining if organic acids are suitable for the leaching of lithium and cobalt from batteries. Experiments with varied temperatures and metal acid concentrations have revealed that the best conditions are 2.0 m/L organic acid at a temperature of around 90 °C. The reaction has a high overall efficiency of over 90% and produces no hazardous byproducts.
5. What is chemical leaching ?
Leaching is referred to as extraction in the chemical processing sector. The extraction of metal from ore using acid and sugar from beets using hot water are two commercial applications of leaching.
The solid mixture to be separated in a typical leaching process consists of particles, inert insoluble carrier A, and solute B.All of the solute is dissolved by the solvent in an ideal leaching equilibrium stage, but none of the carrier is dissolved. The solid-to-liquid mass ratio in the underflow is determined by the type of equipment employed and the qualities of the liquid.
6. Which metal is not extracted by the leaching process?
Apart from aluminum, gold and silver mercury is not extracted by leaching because leaching is a widely used extractive metallurgy technology that transforms metals into soluble salts in aqueous conditions when the ore is soluble and the contaminants are insoluble.
Because bauxite, silver, and gold ores are usually soluble in various solvents, they are concentrated by leaching.
7. What are the disadvantages of leaching?
Leaching's disadvantages include its reduced efficiency and the large amounts of waste effluent and tailings produced, which are typically acidic or alkaline, as well as poisonous (e.g. bauxite tailings).The acidity of the remaining liquid waste produced by this method is considerable.This process' wastewater has the potential to be hazardous.Temperature has an impact on the efficiency of this process.
Either it is chemical leaching, or eco friendly leaching, we should avoid it.
8. In what type of industries leaching is used?
For the separation of sugar from sugar beets using hot water, or the extraction of oil from peanuts, soybeans, and sunflower seeds, leaching is widely employed in the biological and food processing industries.Most crucially, leaching is used in the metals processing sector to separate desired metals from their ores, which are typically made up of a variety of undesirable components. An aqueous cyanide solution, for example, is used to extract gold from its mine.
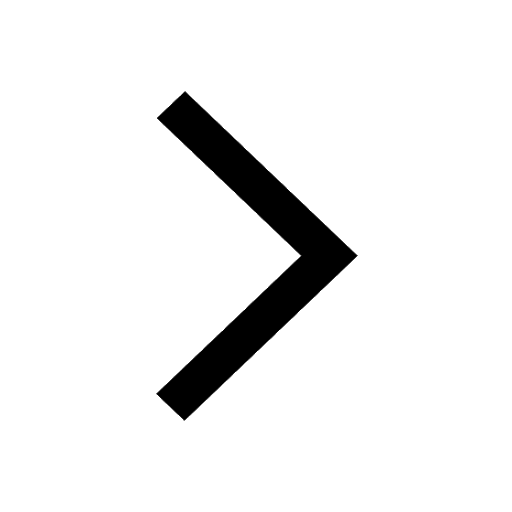
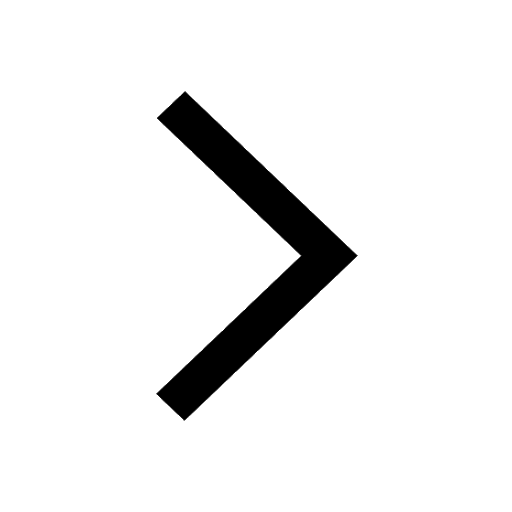
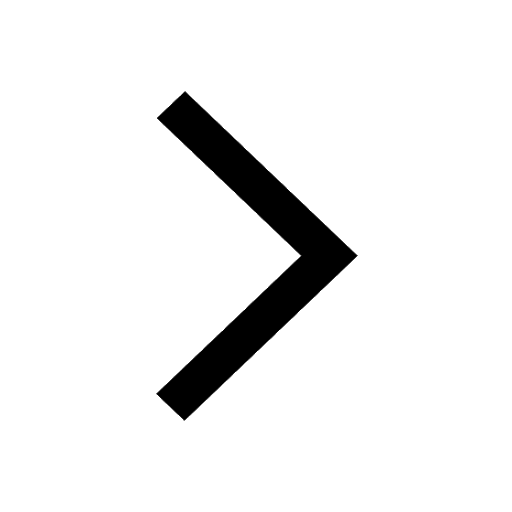
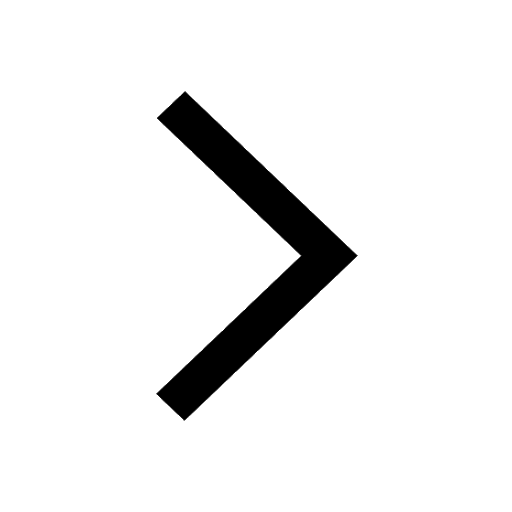
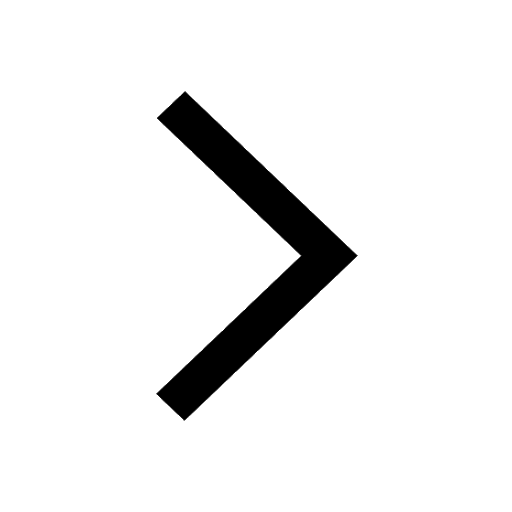
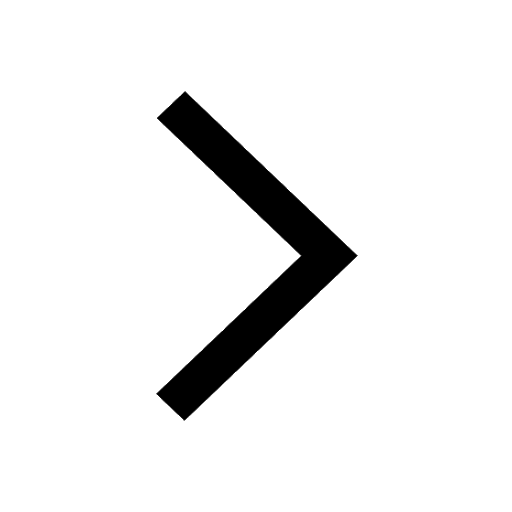