
The electroplating of chromium is undertaken because
A) Electrolysis of chromium is easier
B) Chromium can form alloys with other metals
C) Chromium gives protective and decorative coating to the base metal
D) Of the high reactivity of metallic chromium
Answer
434.4k+ views
1 likes
Hint: Electroplating is the term used to describe a method that involves using a direct electric current to reduce the cations of a metal to form a metal coating on a solid substrate. The cathode (negative electrode) of an electrolytic cell is the portion to be coated; the electrolyte is a solution of a salt of the metal to be coated; and the anode (positive electrode) is often a block of that metal or another inert conductive substance. An external power supply provides the current.
Complete answer:
Electroplating is frequently used in industry and the decorative arts to improve item surface properties like abrasion and corrosion resistance, lubricity, reflectivity, electrical conductivity, and beauty. It may also be used to increase the thickness of undersized or worn-out components, as well as to electroform metal plates with complicated shapes. It's also used to clean metals like copper. Occasionally, the term "electroplating" is applied to techniques that employ an electric current to accomplish an oxidation of anions on a solid substrate, such as the production of silver chloride on silver wire to create silver/silver-chloride electrodes. Electroplating a thin coating of chromium onto a metal item is known as chrome plating (or chromium plating). Chrome is the final result of chrome plating. The chromed coating might be attractive, offer corrosion protection, make cleaning easier, or improve the hardness of the surface. For cosmetic reasons, a less costly chrome imitator is sometimes employed. Higher cathode efficiency and throwing power are two functional advantages of trivalent chromium. Better throwing power equates to higher output rates. Because the current densities required are smaller, less energy is required. The following steps are usually followed when chrome plating a component:
Heavy soiling must be removed by degreasing.
Cleaning by hand to eliminate all traces of dirt and surface contaminants.
Depending on the substrate, several pretreatments are used.
Place it in the chrome plating vat and let it warm up to solution temperature.
To achieve the specified thickness, apply plating current for the needed period.
Hence option C is correct.
Note:
Depending on the type of substrate being plated, there are several variants to this technique. Various etching solutions, such as hydrochloric, hydrofluoric, and sulfuric acids, are required for different substrates. The etching of nimonic alloys with ferric chloride is very popular. When the component is electrically live, it may enter the chrome plating vat. A complying anode composed of lead/tin or platinized titanium is sometimes used in the component.
Complete answer:
Electroplating is frequently used in industry and the decorative arts to improve item surface properties like abrasion and corrosion resistance, lubricity, reflectivity, electrical conductivity, and beauty. It may also be used to increase the thickness of undersized or worn-out components, as well as to electroform metal plates with complicated shapes. It's also used to clean metals like copper. Occasionally, the term "electroplating" is applied to techniques that employ an electric current to accomplish an oxidation of anions on a solid substrate, such as the production of silver chloride on silver wire to create silver/silver-chloride electrodes. Electroplating a thin coating of chromium onto a metal item is known as chrome plating (or chromium plating). Chrome is the final result of chrome plating. The chromed coating might be attractive, offer corrosion protection, make cleaning easier, or improve the hardness of the surface. For cosmetic reasons, a less costly chrome imitator is sometimes employed. Higher cathode efficiency and throwing power are two functional advantages of trivalent chromium. Better throwing power equates to higher output rates. Because the current densities required are smaller, less energy is required. The following steps are usually followed when chrome plating a component:
Heavy soiling must be removed by degreasing.
Cleaning by hand to eliminate all traces of dirt and surface contaminants.
Depending on the substrate, several pretreatments are used.
Place it in the chrome plating vat and let it warm up to solution temperature.
To achieve the specified thickness, apply plating current for the needed period.
Hence option C is correct.
Note:
Depending on the type of substrate being plated, there are several variants to this technique. Various etching solutions, such as hydrochloric, hydrofluoric, and sulfuric acids, are required for different substrates. The etching of nimonic alloys with ferric chloride is very popular. When the component is electrically live, it may enter the chrome plating vat. A complying anode composed of lead/tin or platinized titanium is sometimes used in the component.
Recently Updated Pages
Master Class 12 Economics: Engaging Questions & Answers for Success
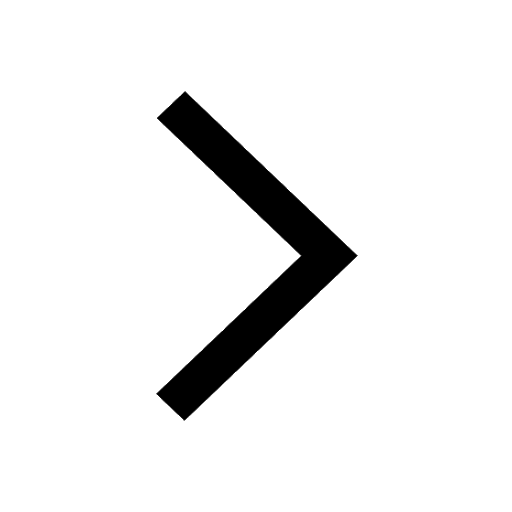
Master Class 12 Maths: Engaging Questions & Answers for Success
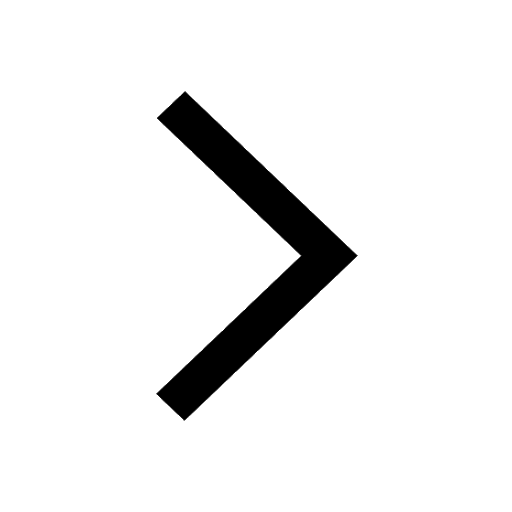
Master Class 12 Biology: Engaging Questions & Answers for Success
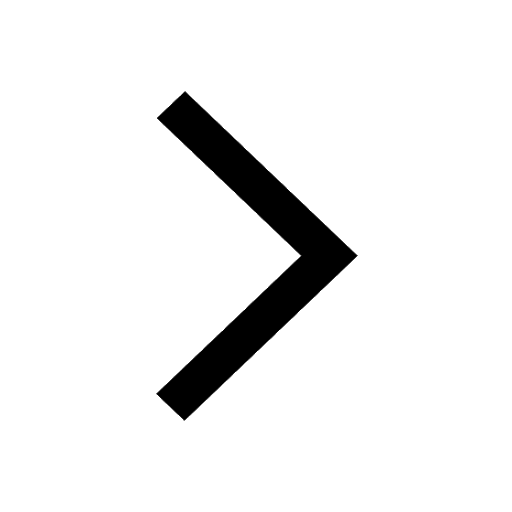
Master Class 12 Physics: Engaging Questions & Answers for Success
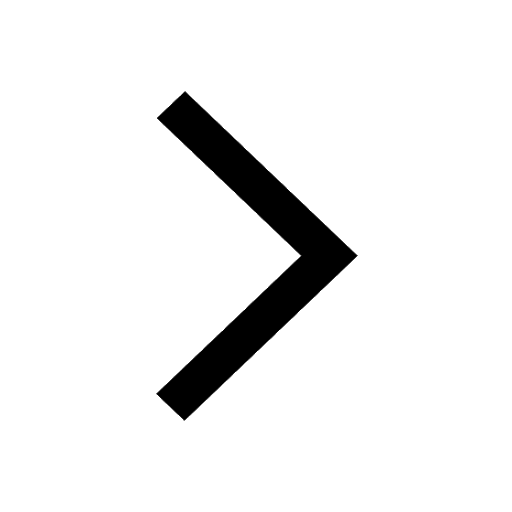
Master Class 12 Business Studies: Engaging Questions & Answers for Success
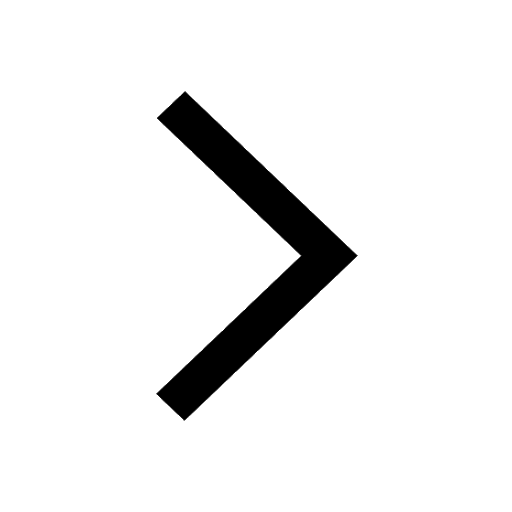
Master Class 12 English: Engaging Questions & Answers for Success
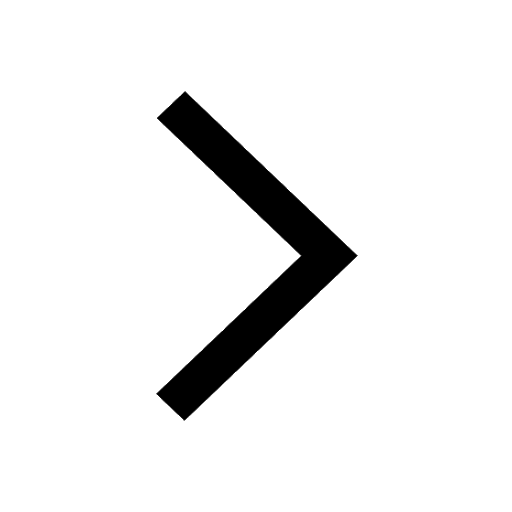
Trending doubts
Which are the Top 10 Largest Countries of the World?
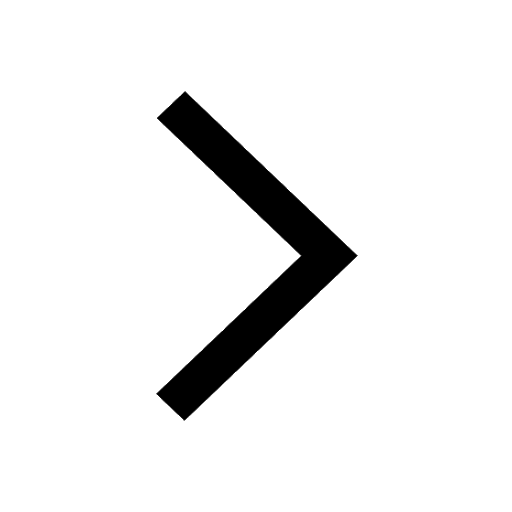
a Tabulate the differences in the characteristics of class 12 chemistry CBSE
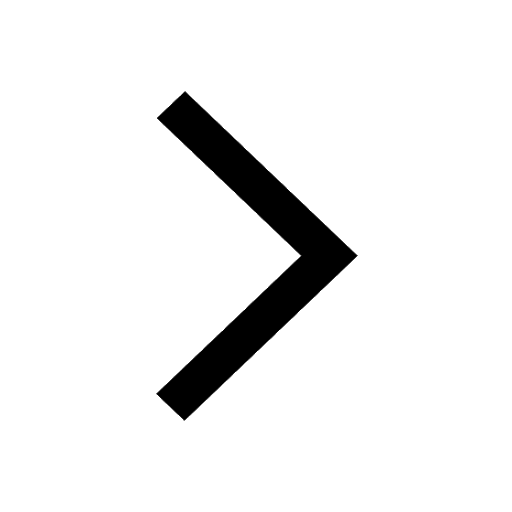
Why is the cell called the structural and functional class 12 biology CBSE
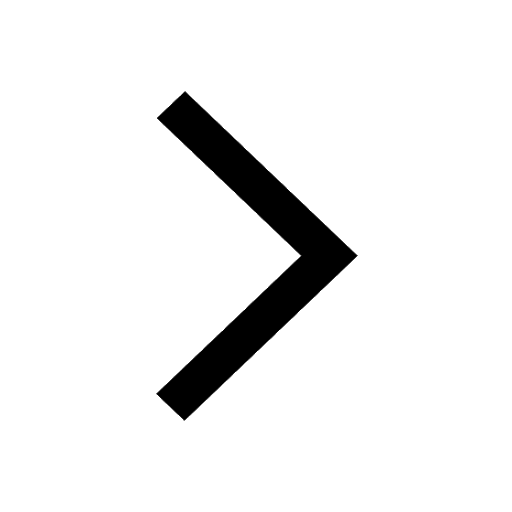
Differentiate between homogeneous and heterogeneous class 12 chemistry CBSE
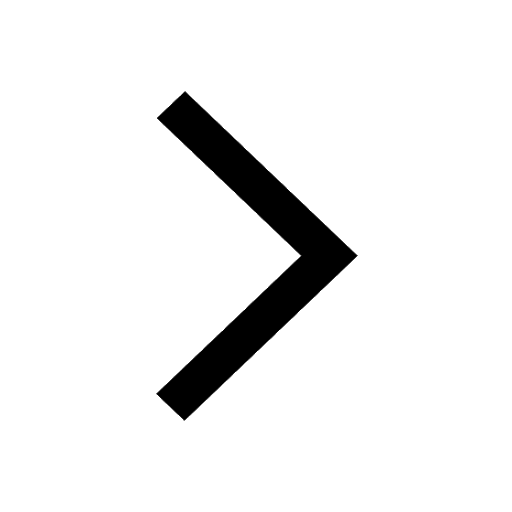
Derive an expression for electric potential at point class 12 physics CBSE
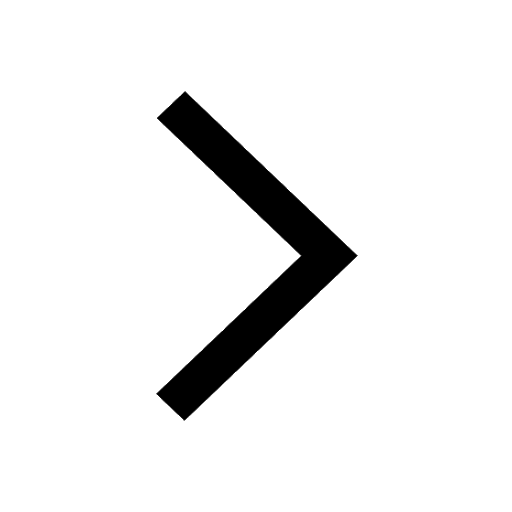
When was the first election held in India a 194748 class 12 sst CBSE
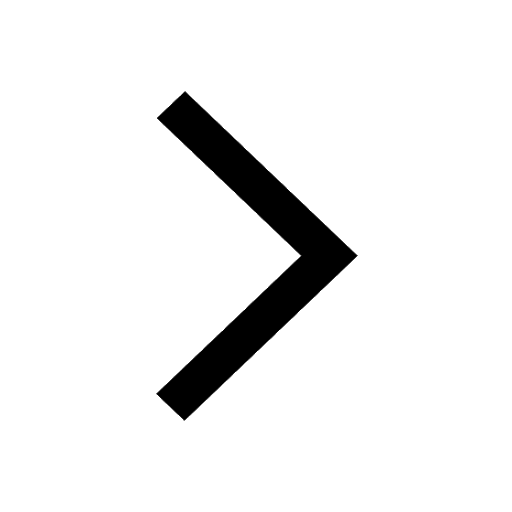